The basic material composition of ordinary refractory ramming refractories is basically similar to refractory castables and plastics, and it is also composed of refractory aggregates, powders, binders, and additives in proportion. The difference between them is that the amount of powder in the ramming compound is more, and the amount of binder is less. Usually, soft clay is added to increase the viscoplasticity and sinterability of the material, and the construction is carried out by ramming. Therefore, this type of unshaped refractory is also called ramming refractory material.
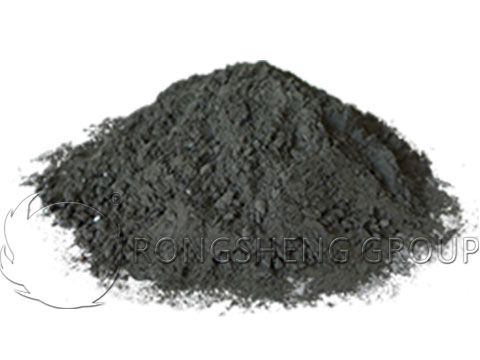
Composition of Ramming Refractories Material
The composition of ramming refractory material is generally 60~65% refractory aggregate and 35~40% refractory powder. In this way, a larger bulk density can be obtained, and the density of the lining body after ramming is also larger. The critical particle size of refractory aggregate is 10mm, and 5mm is also useful, and the mass ratio of coarse and fine aggregate is 3:7~4:6. More fine aggregate is easier to ramming and compact.
Quality requirements of constituent materials for refractory ramming mass
(1) The variety and brand of the finished refractory ramming material shall meet the design requirements.
(2) The quality of the refractory ramming materials prepared on site shall meet the following requirements.
- ①Strictly inspect the quality of each component material, and prepare it according to the designed mix ratio.
- ②The high-aluminum ramming material is made of a high-aluminum aggregate, powder, water glass, and sodium fluorosilicate in proportion, and the material should meet the requirements.
- ③ Magnesium ramming material is composed of metallurgical magnesia, clay refractory mud, iron bauxite, iron oxide powder, brine, or coal tar. The constituent materials should meet the quality standards of related materials.
- ④Dolomite ramming material is composed of dolomite and anhydrous tar.
- ⑤Graphite ramming material is composed of metallurgical coke powder, dehydrated coal tar, and coal pitch. The constituent materials should meet the quality standards of related materials.
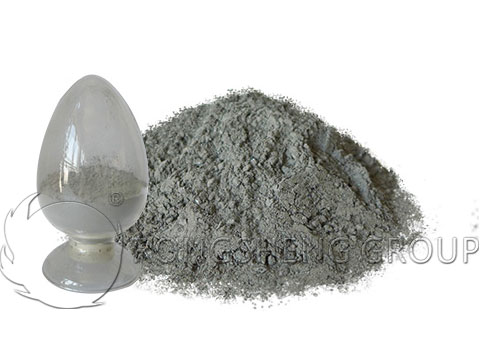
Classification of Refractory Ramming Mass Materials
According to different types of refractory aggregates, refractory ramming mass materials can be divided into clay, high alumina, mullite corundum, siliceous, magnesia, and silicon carbide. According to the different types of binders, it can be divided into phosphoric acid and phosphate, aluminum sulfate, water glass, cement, bonded clay, and organic binders. After the maintenance of the samples of common refractory ramming materials expires, the main performance inspection indexes are shown in Table 1.
Table 1 Main Performance Indexes of Commonly Used Refractory Ramming Materials | |||||||
Items | High Alumina Ramming Material | Magnesia Alumina Ramming Material | Alumina Zircon Ramming Material | Corundum Chrome Zircon Ramming Material | Magnesia Chrome Ramming Material | Magnesia Ramming Material | |
Chemical Composition | Al2O3 | 88 | ≤ 15 | 68 | 74 | 6 | 2.3 |
ZrO2 | 1.1
(Fe2O3) |
55~60
(MgO) |
11 | 6.6 | 59
(MgO) |
93
(MgO) |
|
Cr2O3 | – | 15~20 | – | 15 | 16 | – | |
Crushing Strength / MPa | 110℃ | 38.5 | 74.1
(150℃) |
26.5 | 5.0 | 43.5 | 62 |
1000℃ | 47.6 | 32 | 42.6
(1200℃) |
62.2
(1200℃) |
25.8 | 54 | |
1600℃ | 67.2 | 53 | 38.4
(1400℃) |
123.2
(1500℃) |
38.5 | – | |
Refractoriness Under Load (4%) / ℃ | – | – | 1340 | >1700 | 1500 | – | |
Line Changes after Burning / %
(1600℃) |
+0.60 | -0.14 | +0.93
(1400℃) |
– | -0.60 | -0.1
(1000℃) |
|
Apparent Porosity / % | – | – | 23 | 15 | 13 | 14 | |
Bulk Density g/cm3 | 2.70 | 3.05 | 2.70 | 3.33 | 2.70 | 2.95 |
- High-alumina ramming material uses a bauxite clinker containing 82% aluminum oxide as aggregate and powder. And add more fused corundum powder to improve the performance of the matrix. At the same time, clay is added as a plasticizer.
- Magnesium-aluminum-chromium refractory ramming material is prepared with fused magnesia-chromium composite materials and aluminum-magnesium spinel.
- Aluminum-zirconium ramming material is made of bauxite clinker containing 85% of aluminum oxide as refractory aggregate and powder. Zircon powder and coking mud containing 64% zirconium dioxide are added.
- The proportion of magnesia-chromium refractory ramming materials. The brick magnesia aggregate and powder containing 91% magnesium oxide are 55% and 15% respectively. The chromite aggregate and powder containing Cr2O347% are 15 each. The water glass solution is 4~5%.
- High-strength magnesia refractory ramming material uses fused magnesia containing 97% magnesia as an aggregate material. The critical particle size is 5mm, four-level ingredients, and the ratio of aggregate powder is between 7:3 and 6:4. Phosphate is used as a binding agent, the amount is 2~4%, plus composite metal powder.
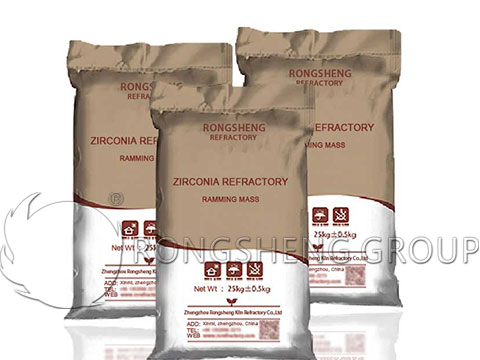
Basic Characteristics of Ramming Refractories Materials
- (1) It has thermosetting, peeling resistance, abrasion resistance, and erosion resistance. Adding tar to dolomite ramming material can enhance the hydration resistance. Graphite ramming material is added with tar as a binder, which has good workability.
- (2) It has a higher operating temperature, generally between 1450~1700℃.
- (3) The volume density of silicon carbide ramming material should not be less than 2.2t per cubic meter. The bulk density of tar-added dolomite and magnesia ramming materials is not less than 2.9t per cubic meter. The body density of high-aluminum and magnesium ramming materials should not be less than 2.95t per cubic meter.
- (4) The construction ramming material should be the finished material produced by a specialized manufacturer, and the finished ramming refractories material should have a factory certificate and instruction manual.
- (5) The particle size of the ramming mass material should be evenly matched. The ratio of the coarse, medium and fine particles is roughly 4:2:4, and the maximum particle size is between 5 and 7 mm.
The Application Range of Ramming Refractories Material
- (1) High-aluminum ramming material is suitable for electric furnace roof and rotary kiln discharge port.
- (2) Magnesium ramming material is suitable for the bottom of electric furnace, open-hearth, and converter.
- (3) Dolomite ramming material is suitable for the bottom of the converter and ferroalloy electric furnace.
- (4) Graphite and silicon carbide ramming materials are suitable for blast furnaces and molten iron ditch.
Construction of Refractory Ramming Material
The refractory ramming material is constructed on-site. It can be rammed with pneumatic picks and other mechanical methods, and the wind pressure should not be lower than 0.5MPa. Small or unimportant parts can also be rammed by hand. The inner lining of refractory ramming mix material has a low moisture content. If ramming is compact, the performance is better than the refractory castable of the same material. The construction speed of refractory ramming mass material is slow and labor-intensive.
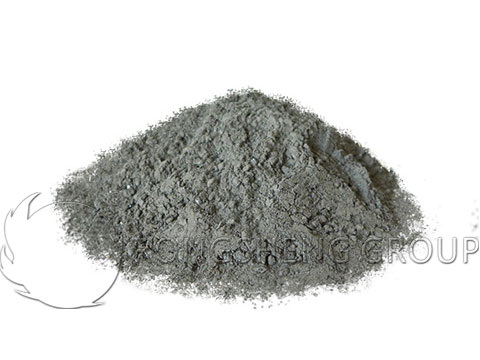
Paving and ramming
Before ramming the ramming mix material, spread the material evenly. For example, when tamping with a pneumatic hammer, one hammer should be used to press half a hammer, and the tamping should be continuous and even layer by layer. The second spreading should be done after the surface of the knotted ramming mass material is messed up. The working wind pressure of the pneumatic hammer shall not be less than 0.5MPa.
The Construction Method of Carbon Ramming Material
The carbon ramming material can be constructed by cold ramming or hot ramming. Before ramming the furnace bottom, the furnace base should be dried and cleaned.
The temperature of cold ramming carbon material when ramming should be about 10℃ higher than the softening temperature of its binder.
The hot ramming carbon material should adopt the finished material. Before ramming, the carbon material must be crushed and heated evenly. The heating temperature should be determined by the mixing temperature of the finished material. There should be no hard lumps in the heated carbon material. A hot hammer should be used when ramming, and the material temperature should not be lower than 70°C.
When ramming with a pneumatic hammer, the thickness of each layer should not exceed 100mm. The tamping density of each layer of carbon ramming material should be checked according to the specified bulk density or compression ratio. The compression ratio is reduction/thickness of loose paving×100%, the value should be 40~45%.
When the ramming of the carbon ramming material is interrupted, the surface of the ramming solid should be cleaned, roughened, and coated with coal tar.
Ramming Refractories Material Construction Method Using Coal Tar as a Binder
The magnesia or dolomite ramming material that uses coal tar and coal tar pitch as the binder should be rammed with a hot hammer. Coal tar, coal tar pitch, and aggregate should be separately dehydrated and heated and mixed and mixed well.
Main points of construction of magnesia ramming material with tar pitch as binder
- ①The magnesia used should be dried and heated, and the material temperature during ramming should be 80~130℃.
- ②The temperature of the masonry surface should be heated to 50~60℃.
- ③Before ramming, the surface of the masonry should be cleaned and painted with a layer of tar pitch.
- ④Pave the material in layers when ramming, and the thickness of each layer should be 20~30mm. Pound until the surface is smooth and you feel the wind hammer has rebound force and can make a metallic sound.
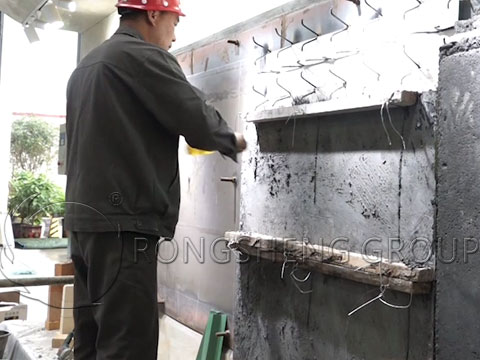
How to choose a suitable construction template?
For ramming construction, formwork should be set as required, and formwork should have sufficient strength and rigidity. The connecting parts and reinforcement must not be disconnected when ramming.
For the template with a small area and complex shape, a wooden mold should be used. For larger areas and regular surfaces, steel formwork should be used. Wood formwork should be supported by wood, and steel formwork should be supported by section steel. The combined template should be connected by bolts.
The Difference between Ramming Refractories Material and Refractory Castable
Compared with refractory castable, ramming refractories material is semi-dry and loose. Under normal circumstances, the ramming mix material has no cohesiveness before forming, and only a strong ramming can have a dense structure. The strength of refractory ramming mass material at room temperature before sintering is relatively low, and the strength is not very high even at medium temperature. Only when the carbon compounds in the bonding agent are coked during heating can a strong bond be obtained.
Compared with castables and plastics refractory, ramming refractories materials have higher stability and corrosion resistance at high temperatures. However, the service life of the ramming material actually depends on the amount of pre-sintering before use or the first sintering. If the heating surface of the ramming mass material is sintered as a whole without cracks and does not stratify with the bottom layer, its use effect will be much improved.

Rongsheng Monolithic Refractories Manufacturer
Rongsheng is an experienced manufacturer and distributor of monolithic refractory castables. Rongsheng’s refractory products have been recognized by customers in more than 60 countries around the world. For example, Vietnam, Laos, Thailand, Malaysia, Singapore, Indonesia, Philippines, Turkey, Kuwait, South Africa, Egypt, Russia Uzbekistan, etc. Rongsheng’s advanced fully automatic unshaped refractory production line has an annual output of 80,000 tons. Obtain high-quality unshaped refractory materials, such as corundum castables, wear-resistant refractory castables, refractory ramming mass materials, refractory plastics, refractory mortar, refractory spray coatings, etc. To get the price for free, please contact us. We will provide you with services according to your specific needs.