When configuring the refractory castable, in order to improve its wear resistance, in addition to adding corundum, an appropriate amount of silicon carbide can also be added. Silicon Carbide Refractory Castable is the development of SiC refractory products. Generally, SiC refractory castables are designed with low cement and ultra-low cement formulations. Use SiC as the main raw material, high alumina cement (CA-70C or CA-80C, etc.), nf-SiO2, and Al2O3 fine powder as the binder.
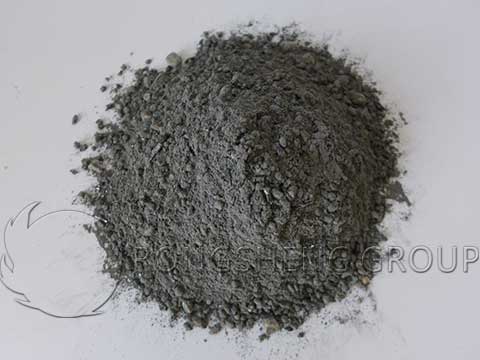
Rongsheng Silicon Carbide Refractory Castables
In the field of monolithic refractories, silicon carbide castables have always been a product that has attracted much attention. To understand the advantages and disadvantages of silicon carbide refractory castables, Rongsheng Refractory Castable Cement Manufacturer can analyze from raw materials to research and development, from production to use. In addition, why can silicon carbide refractory castable resist slag erosion? We can also learn about it in the next article.
Advantages and Disadvantages of Silicon Carbide Refractory Castables
The biggest advantage of silicon carbide refractory castable is that it has high thermal conductivity, low thermal expansion, and does not react with slag. It has been used very early in the kiln parts where slag reaction and high temperature spalling are serious.
The biggest disadvantage is that the chemical properties are very unstable in a certain atmosphere. It is easily corroded in oxidizing gases (such as oxygen, water vapor, carbon monoxide, carbon dioxide), iron oxide, etc., and is easily oxidized and decomposed in molten iron and vacuum. The second disadvantage is that silicon carbide refractory castables have poor water solubility. In water-based unshaped refractories such as castables, sometimes the fluidity is poor, which is likely to cause poor compactness of the silicon carbide refractory castables. The third disadvantage is the lack of sintering and it is difficult to obtain high strength.
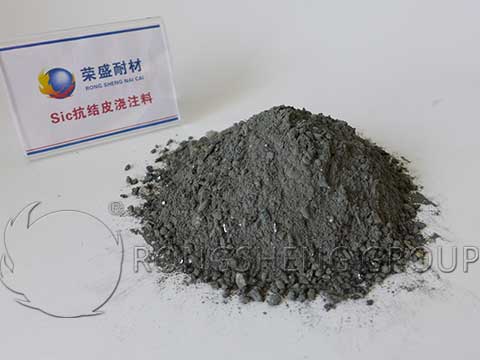
Resistance to Slag Corrosion of Silicon Carbide Castables
The slag resistance and slag resistance of silicon carbide refractory castables need to be considered from the following aspects:
- The wettability to slag (contact angle),
- The invasion of slag,
- Reactivity with slag,
- The melting point and viscosity of the product after the reaction.
The reason why the silicon carbide refractory castable is difficult to be wetted by the slag is the factor of the silicon carbide itself. SiC has two crystal types, α and β, and β-SiC crystal structure. Therefore, the conversion between various types of silicon carbide does not produce a volume effect. SiC is a compound with strong covalent bonding, and it maintains high bonding strength at high temperatures. Therefore, SiC has high hardness, large elastic modulus, excellent wear resistance, and will not be corroded by most acid and alkali solutions. For the intrusion of slag and the low melting point formed after the reaction with the slag, when compared with the refractory castable of oxide raw material, the slag resistance is obviously better.
Types and Applications of Silicon Carbide Refractory Castables
Silicon carbide is widely used in refractory castables, especially aluminum-silicon carbide castables and high-aluminum-silicon carbide-carbon castables. Mainly used in the steelmaking industry.
aluminum-silicon carbide castables
Aluminum silicon carbide castables are mainly made of high alumina bauxite and silicon carbide with an aluminum content of more than 75%. It is a castable made of pure aluminate cement and silica micro powder composite bonding agent, adding explosion-proof fiber, kyanite, anti-shrinking agent, and other additives. Aluminum silicon carbide castables are often used in the lining of ladle, so it is also called steel ladle castable.
The main features of this refractory castable applied to the ladle are: high-temperature resistance, hot metal erosion resistance, resistance to chemical corrosion of iron slag, resistance to rapid cold and rapid heat, and strong resistance to thermal shock and spalling. It has strong adaptability to the working environment of the ladle. Therefore, the aluminum-silicon carbide castable can be used as the lining of the molten iron ladle.
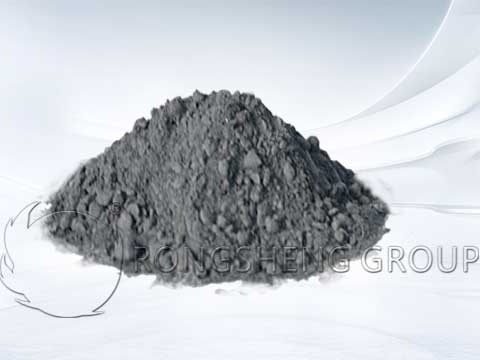
high-aluminum-silicon carbide-carbon castables
Rongsheng High aluminum-silicon carbide-carbon castable, also known as A-S-C refractory castable. It is mainly a castable refractory castable composed of corundum/super high-bauxite clinker, silicon carbide and carbon, binder, and admixture. It is mainly used for the inner lining of the taphole of the blast furnace, so it is also called the tapping refractory castable. Among them, those made of corundum as the main raw material are called corundum-silicon carbide-carbon castables; those made of high alumina bauxite clinker are called high-aluminum-silicon carbide-carbon castables.
Due to the poor air permeability of the castable, the lining bursts due to improper temperature control during the baking process. Therefore, explosion-proof fiber or metal aluminum powder must be added as an explosion-proof agent when configuring. The amount of anti-explosive agents should be appropriate. Excessive addition will cause a decrease in bulk density, strength, erosion resistance, and erosion resistance.
Because the lining of the tap chute of the blast furnace is mainly divided into four channels: main slag line, main ditch iron line, branch iron ditch, and slag ditch, and the use temperature and chemical corrosion are different. Therefore, different casting trough castables need to be selected for different use parts. For silicon carbide castables, the amount of silicon carbide added varies according to different parts of use. For example, the amount of addition of the iron tap and the slag line is 18%-30%; the amount of silicon carbide below the slag line is 12%-15%. Due to the high price of silicon carbide, the amount of castable is also different, and the price of silicon carbide castable is quite different.
What Effects Does the Addition of SiC on the Performance of Castables?
SiC is a high-grade refractory raw material, which plays the role of alkali resistance, corrosion resistance, high thermal conductivity, thermal shock resistance, and anti-skinning in refractory castables. Just like Silicon Carbide (SIC) anti-skinning castable, it forms a glaze on the surface of the material at high temperatures to prevent the penetration of the glass phase in the cement raw material, thereby playing the role of anti-skinning. This material is mainly used in the crusted parts such as the lower slope of the cyclone preheater, the rising flue, and the preheater cone.
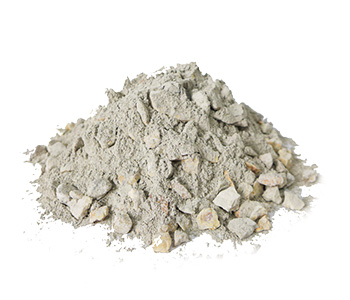
Adding a small amount of silicon carbide to the corundum-mullite castable can improve the performance of the castable in many aspects:
- (1) It can reduce linear shrinkage after firing and maintain volume stability.
- (2) Low porosity, dense structure castables can be obtained, which helps to improve corrosion resistance.
- (3) Mullite crystal phases are widely formed inside the matrix and between the matrix and the aggregate. As mullite grows up, it is staggered distribution, which improves the bonding strength between the matrix and the aggregate of the castable.
- (4) It can significantly improve the high-temperature flexural strength of refractory castables.