With the development of the modern steelmaking industry, the smelting conditions of ladle are becoming increasingly severe. The use conditions of refractory materials used in ladle linings are becoming more and more demanding, and traditional refractory castables can no longer meet the needs of technological progress. Therefore, it is imperative to research and develop new high-performance castables for the ladle. At present, corundum-spinel castables are widely used due to their good high-temperature performance. Therefore, corundum-spinel castable is also the mainstream material for refining ladle air-permeable bricks.
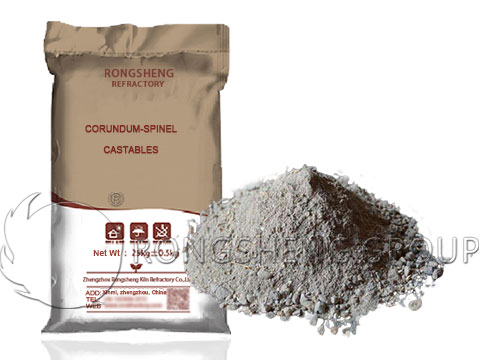
Characteristics and Application of Corundum-Spinel Castable
Al2O3-spinel castable, namely corundum-spinel castable. Alumina-spinel castable is made of fused or sintered corundum or tabular corundum as aggregate. The powder is composed of pure synthetic spinel powder, α-alumina micro powder, reactive alumina powder, pure calcium aluminate cement, and dispersant. It belongs to low cement combined castable.
The corundum-spinel refractory material combines the excellent properties of corundum and magnesia-alumina spinel. It has the advantages of good volume stability, excellent slag resistance, and high-temperature strength. It is widely used in refractory materials such as ladle lining, RH furnace, and breathable bricks.
The melting point of corundum is about 2050℃, and it has good wear resistance and erosion resistance. The spinel (theoretical composition is MgO28.3%, Al2O371.7%) has a melting point near 2135℃ and has good chemical stability, thermal shock stability, and corrosion resistance. The “pure” system composed of these two substances, after high-temperature treatment, forms three high-melting mineral phases, namely calcium Hexa-aluminate, alumina-magnesia spinel, and corundum, which is called the best matrix system. Among them, the average expansion coefficients of spinel and corundum at 0~1000K are 7.6×10-6/K and 8.8×10-6/K, respectively. The two will form complex toughening so that the castable has good thermal shock stability. The three mineral phases form a good combination with each other so that the castable has excellent slag resistance and thermal shock resistance, so it is widely used in ladle linings, ventilation elements, and spray guns.
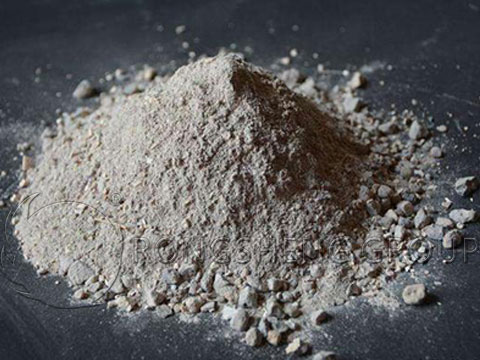
Problems of Corundum-Spinel Castable
Due to the increase in demand for clean steel and high-quality steel, refining technology outside the furnace has been rapidly developed, and the use environment of ladle air-permeable bricks has become increasingly harsh. The performance of the air-permeable brick, especially the thermal shock resistance, has become more important to ensure the reliability and safety of the refining process outside the furnace. Further improving the thermal shock resistance of corundum-spinel castables has also become a research hotspot. The existing corundum-spinel castable also has the following problems.
- The low adhesion rate will make the lining material easy to crack and fall off in the middle and late stages.
- The volume stability is poor.
- The thermal shock resistance is weak.
The reaction of castable and molten steel/slag
The reaction of the castable with molten steel and molten slag at high temperature and the structural spalling caused by the erosion and penetration of the molten slag are the main reasons for the damage of the corundum-spinel castable refractory. Molten slag contains a variety of chemical components, which easily react with the main components of refractory materials to form inclusions such as 2MnO·SiO2 ·Al2O3, 2CaO·SiO2 ·Al2O3. The particle size of this kind of inclusions is usually on the micro-nano scale, and it is relatively difficult to remove them from floating, which has become one of the main sources of inclusions in molten steel. In addition, after the high content of CaO in the refined slag penetrates into the castable, the continuous expansion reaction process of Al2O3 → CA6 → CaO·2Al2O3 (CA2) /12CaO·7Al2O3 (C12A7) will be triggered. This expansion process does not match the thermal expansion coefficient of the castable body, and finally causes cracks in the reaction permeable layer body material layer gradually. During the use of the ladle, the structure of the corresponding part is prone to peeling, resulting in the introduction of large-scale foreign inclusions into the molten steel.
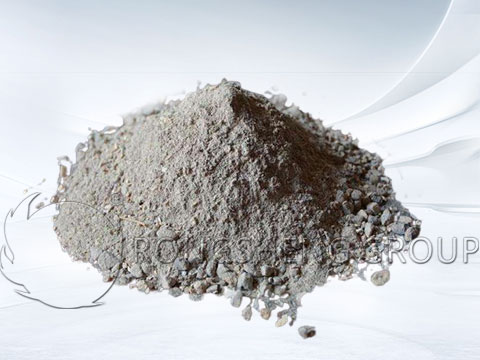
How to Improve the Performance of Corundum Spinel Castable
It has been reported in the literature and has been proved by the experiment of refractory manufacturers. The fused zirconia corundum particles of different sizes, compositions, and contents are introduced into the corundum-spinel castable. It can make the castable’s heating permanent linear change rate, normal temperature flexural strength, high-temperature flexural strength, and elastic modulus after the thermal shock has regular changes.
(1) According to the principle of zirconia martensite transformation, cracks can be generated in the corundum spinel castable by adding zirconium corundum raw materials. The size and number of cracks formed depend on the type, particle size, and content of the zirconia corundum introduced.
(2) Properly generate microcracks in the corundum spinel castable, although it reduces the strength and elastic modulus of the material, it has a certain positive effect on improving thermal shock resistance.
(3) The high-temperature flexural strength of the zirconia-containing corundum castable is higher than the normal temperature flexural strength. The main reason is that the thermal expansion coefficient of the castable matrix is larger than that of zirconium corundum at high temperature, and the matrix squeezes the wrong corundum particles, which reduces the number of internal cracks in the material or the extent of expansion.
Influence of particle size composition on corundum-spinel castable
Reasonable particle gradation makes the castable have excellent room temperature strength, construction performance, and proper porosity and pore size. When calculating according to Andreasen’s theoretical formula, the particle size distribution coefficient of the castable is generally between 0.2 and 0.3. To obtain a castable with good fluidity, the key is to optimize the material particle distribution (PSD) of the material.
The slag retaining wall is a prefabricated block of vibrating castable, so the construction performance in production directly affects its performance. Therefore, the choice of critical particles and particle composition is particularly important. At the same time, under the premise of ensuring smooth construction, its use strength cannot be reduced.
Thermal shock resistance
Focusing on the improvement of castable strength and thermal shock resistance, researchers mainly adopt methods such as adjusting raw material components and introducing additives. Add sintered spinel fine powder to improve the high-temperature flexural strength of corundum-spinel castable. The results show that the sintered spinel powder with a diameter of less than 0.038 mm has the highest high-temperature flexural strength and the best thermal shock resistance when the mass fraction of 5% is added. In addition, the type and particle size of spinel is very important to the performance of castables, depending on the distribution of these spinels and specific reactions at high temperatures.
The study found that the mass fraction of 0.9% SiO2 fine powder can maximize the thermal shock resistance of corundum-spinel. The reason is that the shrinkage caused by the sintering-promoting effect of the SiO2 fine powder on the sample and the expansion when the in-situ spinel is generated in the sample have reached a balanced state. Other studies have shown that the addition of α-Al2O3 powder can increase the strength of the castable, but it will reduce the thermal shock resistance of the material.
Linear expansion during firing
Because unshaped refractories have a series of advantages such as time-saving, labor-saving, and energy-saving, they are widely used in the fields of thermal engineering and metallurgy. As a new generation of advanced refractory material, corundum-spinel castables have been successfully applied to ladle and blast furnace hot air onlookers lining. The linear expansion rate of a castable is an important index to measure its high-temperature performance. Therefore, studying the effects of different factors on the linear expansion rate of corundum-spinel castables is of great significance for selecting suitable castables under different conditions of use.
Some experiments came to the following conclusions,
- (1) The addition of magnesia oxide has a significant effect on the linear expansion rate of corundum-spinel castables. When cement is used as the binder and the addition of magnesia oxide is 7%, the linear expansion rate of the castable after firing at 1450°C reaches 1.846%.
- (2) Decreasing the particle size of fused corundum can increase the linear expansion rate of the castable.
- (3) When the addition amount of magnesia oxide is constant, increase the addition amount of cement, and the linear expansion rate of the sample increases first and then decreases.
- (4) Under the condition that the addition amount of magnesia oxide and cement is constant, increasing the addition amount of silica powder can effectively inhibit the linear expansion of the castable.

Rongsheng Refractory Castable Manufacturer
Rongsheng is an experienced refractory castable manufacturer. Rongsheng’s advanced automatic unshaped refractory castable production line has an annual output of tons. The Rongsheng monolithic refractory production line has successfully completed the supply and construction of monolithic refractories for many large-scale turnkey projects. Our unshaped refractories mainly include various wear-resistant refractory castables, refractory spray coatings, refractory plastics, refractory ramming materials, etc. In addition, we can also provide customers with customized amorphous materials according to their specific working conditions. If you need to buy unshaped refractory materials, such as corundum spinel castables, etc. Or if you want to know our Rongsheng refractory manufacturer, please contact us. We will provide you with services according to your specific needs.