Low cement castable refers to a castable with low cement content. The cement dosage of refractory cement castables is generally 15% to 20%, and the cement dosage of low cement castables is about 5%, and some even reduce to 1% to 2%. Application of Low Cement Castable. The purpose of reducing the amount of cement is to improve the fire resistance of the castable. After molding and curing, less cement hydrate is formed. During heating and baking, there is no problem that a large number of hydration bonds are destroyed and the medium temperature strength is reduced. Instead, as the heat treatment temperature increases, it gradually sinters and the strength gradually increases. The water requirement of the castable is greatly reduced, so the porosity is low and the volume density is high. From the refractory castables manufacturer, it is very suitable for all kinds of heating furnaces and soaking furnace refractory lining materials.
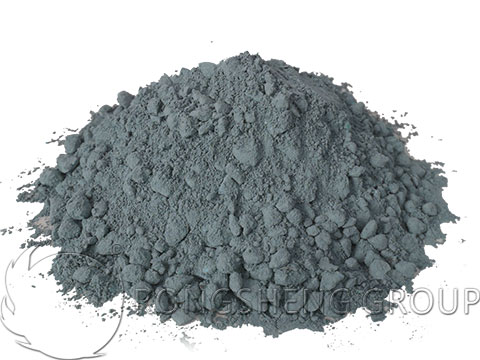
Construction of Low Cement Castable on Soaking Furnace
Low cement castables and ordinary castables are both refractory castables combined with calcium hard aluminate cement, which are widely used in thermal equipment in metallurgy, petroleum, chemical, and other industries, and have achieved good results. In the overall pouring of the soaking furnace, the installation of anchoring bricks, the retention of expansion joints, and the 20 Pa pressure operation of baking below 200 ℃ for 4 days are the key points.
When low-cement castable is cast as a whole, it is poured layer by layer from the bottom of the furnace wall up. Take the height of two anchor bricks as one layer, paste ceramic fiber felt, build light clay bricks, and support the template. The mixed low cement castable can be poured into the formwork through the funnel. Flatten and shake with a vibrating rod, which is very important. Whenever it is poured to the horizontal position of the anchor brick, it is best to be 20 mm higher than it. Then the anchor bricks are kneaded, squeezed, and hung by hand so that they are stably placed on the required horizontal position. When pouring to the furnace mouth, spread two layers of oil felt paper to ensure easy removal during intermediate repairs. It can be demoulded 2 days after pouring.
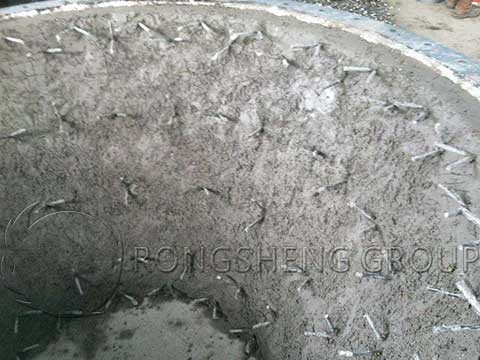
Hardening Mechanism of Low Cement Castable
Low cement castables rely on the addition of several special raw materials to obtain good performance. In the Application of Low Cement Castable, First, pure calcium aluminate cement, due to the high content of effective mineral CaO·Al2O3, can obtain the required strength with less mixing. The second silica fume is glass beads with a SiO2 content between 93% and 98% and an average particle size of about 0.5 μm. After adding silica fume, the castable has good fluidity, low molding water requirement, and low sintering temperature, which improves the performance after heat treatment. Third, alumina powder is easier to participate in the reaction and improve the fire resistance of the material. Fourth, the water reducing agent, which can be adsorbed on the surface of the powder, and then generate electrostatic repulsion to disperse the powder, so as to further play the role of fine powder.
Oven-drying after Casting Low Cement Castable
The oven-drying is an important part that directly affects the service life of the soaking pit of the low cement castable. During the Application of Low Cement Castable, they contain ultrafine oxide powders, so they have the weaknesses of poor air permeability and poor chipping resistance. Cracking is a phenomenon produced when the internal steam pressure of the castable increases beyond its strength during the drying period. It is closely related to the diffusion rate of steam, that is, the air permeability of the pouring body. For this reason, the oven-drying curve should be controlled within 200°C in the first 4 days, and the temperature should be lower at the beginning, and the oven-drying should be operated with slight positive pressure. The practice has proved that this method effectively overcomes the cracking and lays an extremely favorable foundation for the subsequent heating of the oven-drying.
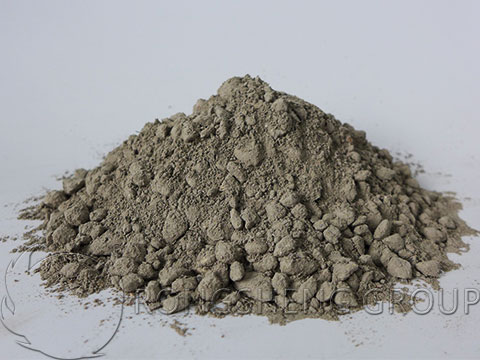
The Effect of Using Low Cement Castable
Since the first furnace pit was poured, more than 2,400 tons of low cement castables have been successfully used. From construction, oven-drying to formal production, low-cement castables have the characteristics of good pressure resistance, high flexural strength, good high-temperature volume stability, and good thermal shock stability at low, medium, and high temperatures. The average life of each furnace pit is more than 3 years. Practice shows that low cement castables are good materials for soaking furnace pits. For more information, please contact rs low cement castable manufacturers.