When selecting refractory materials, the technical performance requirements of refractory materials must be put forward according to the specific conditions of the furnace. The Rongsheng refractory castable manufacturer believes that the technical performance of the refractory used in the bloom heating furnace should be considered. Such as high softness, resistance to rapid cold and heat, small linear change, high strength at room temperature, medium-temperature, and high temperature, and slag resistance in several aspects. Therefore, high-strength and high-alumina mullite castables are the best choices. In this castable, part of mullite and additives are added. In order to promote the formation of a large number of mullite as much as possible, and to ensure high strength at room temperature, medium-temperature and high temperature, and good construction performance. The properties of high-strength and high-alumina mullite castables are shown in Table 1.
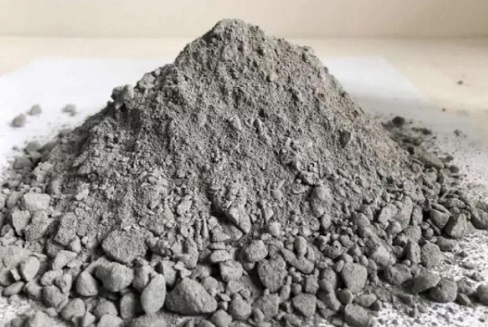
Performance of High-Strength and High-Alumina Mullite Castable
Table 1 Performance of High-strength and High-alumina Mullite Castable | ||
Al2O3 (w/%) | 70 | |
Drying at 110℃, Bulk Density (g/cm3) | 2.5 | |
1350℃ × 3h, Linear Change Rate | -0.2 ~ +0.3% | |
Flexural Strength (MPa) | 110℃ × 24h | 4 |
1350℃ × 3h | 10 | |
Compressive Strength (MPa) | 110℃ × 24h | 22 |
1350℃ × 3h | 90 | |
Max Use Temperature (℃) | 1600 | |
Refractoriness (℃) | 1790 |
Requirements for On-site Construction of High-Strength and High-Alumina Mullite Castables
In order to obtain the expected effect of mullite castable, in addition to reasonable design and good quality of the castable itself, the construction quality is also an important factor.
(1) Preparation before construction
High-strength and high-alumina mullite castables are formulated with multiple components. Active composite ultrafine powder and a small amount of pure calcium aluminate cement are added, which is more active. Therefore, the storage conditions and time requirements are relatively high, and it must be strictly protected from moisture. If the packaging is damaged or affected by moisture, it is not allowed to use. Its storage period should not exceed two months from leaving the factory. Construction machinery must be cleaned up to ensure the normal operation of construction machinery, such as forced mixers, vibrating rods, scales, and drill drills.
(2) Installation of anchor bricks
The arrangement of anchor bricks in the refractory castable lining must be horizontal and vertical. The proper distance is 400~500mm. The anchor bricks should be fixed during construction, and they should not be displaced due to construction forces. In order to prevent displacement, wooden wedges can be used for positioning.
(3) Setting of expansion joints
Expansion joints are determined according to the linear rate of change of mullite castable and experience. The high-strength and high-alumina mullite castable is reserved for 4 to 5 mm per meter of cast body. After pouring, the outside of the expansion joint should be covered and sealed with clay bricks. After putting into production, there should be no fire, and the plugging material should be easy to melt.
Learn More about the High Strength Mullite Castables For Sale, Email Us Now!!!
(4) Construction of mullite castable
Before construction, the operator should be able to grasp the operating points and quality requirements of each process. After the ingredients are added to the mixer, dry mix and mix for 1 minute, and then add water. If the material is too dry or too thin, it will affect the quality. Generally, it can be kneaded into a dough and made into a slurry by hand. It is strictly forbidden to add water temporarily when pouring out of the tank. Once the amount of water added is determined, it should not be changed easily to ensure the consistency of each mixing.
Generally, the stirring time is 5 minutes, too long or too short is not good. The mixed castable should be poured immediately, and parked in the middle should not exceed 20 minutes. The pouring material should be laid evenly at the construction site, and the formwork, expansion board, anchor brick, and other facilities should not be touched and dislocated due to excessive force.
Generally, the vibrating rod is used to vibrate the material about 300mm, and each part should be re-slurried. When pulling out the vibrator, you should lift it slowly to avoid leaving holes. If you find that there is no vibration, dig out and re-tighten it. After pouring, the surface of the pouring body does not need to be polished.
Normally, it is naturally maintained for 2 to 3 days, and it is strictly forbidden to step on or touch it during the maintenance period. When the castable is solidified, vent holes should be pierced in time to help eliminate water vapor. The mold can be demolded after confirming that it has sufficient strength.
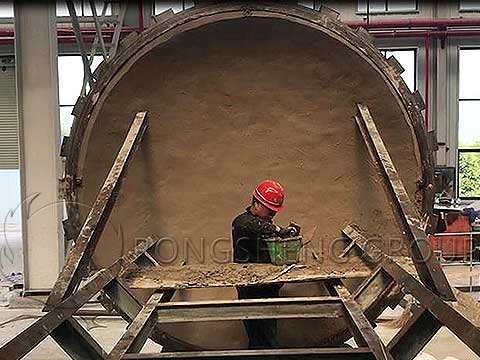
Oven-drying after On-site construction of high-strength and high-alumina mullite castable
The quality of the lining on-site pouring is of course very important, but the baking quality of the lining is directly related to the success or failure of the castable application. The pouring body contains a large amount of free water and crystal water, which need to be fully removed by the oven-drying, which is an extremely important link for the longevity of the furnace lining. As the volume and pressure increase sharply when the moisture becomes water vapor, if the baking temperature rises too fast, it will cause the furnace lining to crack, peel off or explode.
High-strength and high-alumina mullite castables are dense and high-strength types, with low porosity, and it is not easy to remove moisture. Especially in the removal stage of a large amount of free water in the temperature range of 100-300 ℃, it is easy to cause excessive steam pressure and cause the furnace lining to peel off or explode. Therefore, special attention should be paid, and sufficient time should be given for elimination. As the temperature continues to rise, free water and crystal water are continuously removed. When it reaches 500 ℃, the moisture content of the castable only accounts for about 10% of the total water content.
Therefore, the temperature of the castable should be slow before 600℃, and there should be enough holding time. After 1000 ℃, mullite began to form in large quantities. After the formation of the primary crystals of mullite is basically completed at 1300 ℃, the mullite grains continue to grow so that the castable is densified, the bonding force increases, and the strength increases. On the basis of summing up the experience of the last few oven-drying, we assigned four working teams to oven-drying. Record the temperature changes and fuel consumption of the heating section, soaking section, and preheating section every hour. Finally, through everyone’s joint efforts, the oven-drying task was completed satisfactorily. It can be seen that the oven-drying after the on-site construction of high-strength and high-alumina mullite castables is a very important step, and it is also a step that requires more attention and careful operation!

Rongsheng Refractory Castable Manufacturer
Rongsheng refractory material manufacturer is an experienced manufacturer of refractory castables. Rongsheng’s refractory products have been sold to more than 60 countries around the world. Rongsheng’s advanced monolithic refractory castable production line has an annual output of 80,000 tons. We not only have strong strength in the production of refractory castables but also have rich experience in providing customers with solutions for uncertain refractory linings. If you want to buy high-strength and high-alumina mullite castables, Corundum mullite castable, mullite insulating castable, etc., or want to get more information about Rongsheng refractory manufacturers, and learn more about the prices of monolithic refractory products, please contact us. We will provide you with services according to your specific needs.