Recently, a user of Rongsheng Refractory Material Factory consulted that a batch of refractory plastics purchased before could not solidify after ramming, and wanted to ask what was going on. Rongsheng Factory, based on years of production, sales, and construction experience, analyzed from the following aspects to help customers solve the problem. Rongsheng Refractory Castable Factory, a professional technical team, and an environmentally friendly fully automatic amorphous refractory production line provide material guarantees for the overall refractory lining of high-temperature industrial furnaces. Contact Rongsheng to get free solutions and quotes for refractory linings.
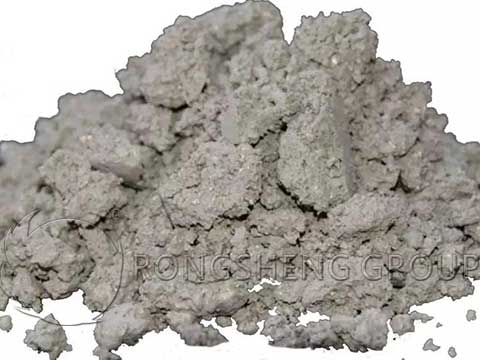
As we all know, the components of refractory plastics are made of granular and powdered aggregates, plastic clay, and other binders and plasticizers, and then a small amount of water is added. After fully mixing, it is a hard mud-paste-like amorphous refractory material that maintains high plasticity for a long time.
-
What aggregates and binders are refractory plastic components divided into?
According to the type of aggregate, it can be divided into clay, high aluminum, mullite, corundum, chromium, silicon carbide, and zirconium-containing refractory plastics. According to the type of binder, it can be divided into refractory plastics combined with aluminum sulfate, phosphoric acid, phosphate, water glass and resin.
-
The plasticity index of refractory plastics requires that the amount of water added must be limited when adding binders
Plastic clay is an additional binder for plastics. It only accounts for 10%~25% of the total weight of plastics, but it has a great influence on the bonding strength between plastics and their hardened bodies, the plasticity of plastics, the volume stability and refractoriness of plastics and their hardened bodies.
The plasticity of refractory materials is related to the characteristics of clay, the amount of clay used and the amount of water. It mainly depends on the amount of water, which increases with the increase of water. However, too much water will bring adverse effects, generally 5%~10% is appropriate.
-
Necessity of adding appropriate amount of plasticizer to refractory plastic
In order to control the amount of clay in plastic and reduce the amount of water, it is necessary to add appropriate amount of plasticizer. Its plasticizing effects mainly include: increasing the hygroscopicity of clay particles. Dispersing clay particles and wrapping them with water film. Dispersing humus in clay and making clay particles sol. Increasing the electrostatic repulsion between clay particles in clay-water system. Stabilizing sol. Excluding ions that hinder solification from the system as insoluble salts, etc.
-
Considering the hardening and strength of plastic, it is necessary to correctly select the binder
Plastic without any added chemical binder is called ordinary plastic. This kind of plastic has very low strength before sintering, but as the temperature rises, water escapes and the strength increases. After high-temperature sintering, the cold strength increases. But the hot strength at high temperature decreases with the increase of temperature.
The strength of plastic with sodium silicate increases faster with the increase of temperature after construction, and the mold can be removed faster after construction. However, during the drying process, this binder may migrate to the surface of the structure or product, preventing the smooth removal of moisture and causing stress and deformation of the surface.
Aluminum phosphate is the most widely used thermosetting binder in plastics. After construction, it can obtain high strength after drying and baking.
In order to improve the shortcomings of plastics with soft clay as binder, such as slow hardening after construction and low strength at room temperature, it is often chosen to add an appropriate amount of air-hardening and thermosetting binders and their polymers.
-
High-quality plastics also need to have excellent thermal shock resistance
The good thermal shock resistance of plastics mainly depends on the following aspects: Plastics made of aluminum silicate refractory raw materials as granular and powdered materials will not produce serious deformation caused by crystal transformation during heating or when used at high temperatures. The mineral composition near the heating surface is fine crystals of mullite and cristobalite, with less glass, and transitions along the heating surface to the low-temperature side. The structure and phase of the plastic are gradual rather than drastic. Due to the uniform porous structure in the plastic component, the expansion coefficient and elastic modulus are generally low.
-
Correct construction method of refractory plastics
The construction of plastics requires a tamping machine or manual tamping. The thickness of each addition is 80~100mm. After tamping, the surface is loosened, and then the material is added to continue tamping until it is completed. According to the type of binder, temperature and humidity conditions, the plastic should be naturally dried for a period of time before demolding. Because demolding too early will cause cracks on the stress surface of the anchor brick. When the temperature is around 25℃, the plastic combined with phosphoric acid should be demoulded after 48 hours of natural drying. The plastic combined with aluminum sulfate and clay should be demoulded after 72 hours of natural drying.
-
The shelf life of refractory plastic should not be too long
Refractory plastic generally has a shelf life of 15 days. Experienced manufacturers do not use hydraulic binders to ensure that the plasticity of plastic does not decrease significantly during its shelf life. Rongsheng Refractory Material Manufacturers recommends that users use up the products in one construction within 3-5 days after the arrival of the goods, and do not store them for a long time.
Rongsheng Refractory Material Manufacturer recommends that you purchase high-quality refractory plastic products and read the instructions for the construction and use of refractory plastic in detail. Strictly follow the construction instructions for construction. Choose a professional construction team to carry out the construction of the refractory furnace lining. After the construction is completed, reasonable maintenance of the refractory furnace lining can effectively extend the service life of the furnace lining.