The basic mechanism of micro-powder in refractory castables is filling and lubrication. The micro powder can be used to fill the gap between aggregate and powder, reducing the amount of water used. After the molded body removes water, there are fewer holes left, which can increase the bulk density and reduce the apparent porosity. Thereby improving the structural strength of the material and optimizing material performance. In addition, the fine powder particles can form colloidal particles in water. When there is a dispersant, the particle surface forms an overlapping electric double layer to generate electrostatic repulsion, which overcomes the van der Waals force between the particles. Reduce the interface energy and prevent the particles from adsorption and aggregation. At the same time, the dispersant is adsorbed around the particles to form a solvent layer. Therefore, the fluidity of the castable is also increased, and the performance of the refractory castable material is optimized.
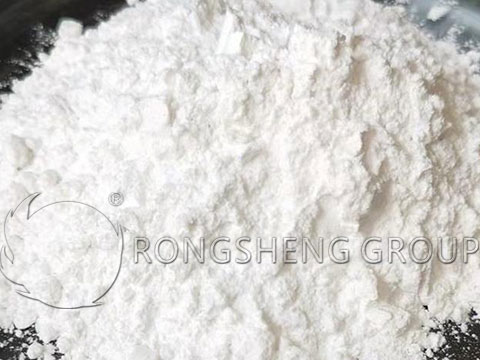
Micro-powder Used in Refractory Castables
In refractory castables, the most used micro powders are active SiO2 powder and a-AL2O3 powder. Followed by SiC powder, high alumina powder, white corundum powder, brown corundum powder, zircon powder, and spinel powder. The function of micro-powder in refractory castables is to fill and lubricate and increase fluidity.
The Silica Powder Added in the Refractory Castables
The SiO2 powder used in the refractory industry is mainly micron-sized. There are many types of SiO2 micro powders, among which silica fume has good performance and a wider range of applications. It is a by-product of ferrosilicon alloy plants and metal silica plants. In addition, there are natural mineral powder quartz, SiO2 powder milled by a grinder, and white carbon black powder. Electronic industry by-products, active SiO2 powder on the surface treated by silane coupling. Fused silica powder. When using zircon to produce desiliconized zirconium dioxide, the collected by-product-silica powder, and the silica powder collected in the production of metal silica.
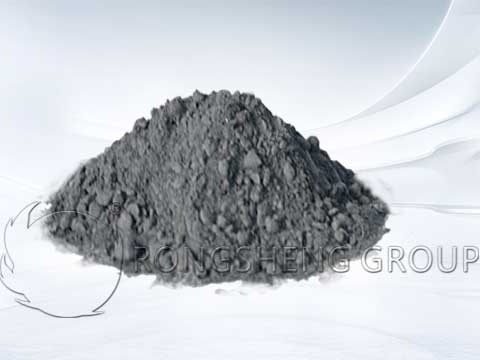
What is the role of silica powder in refractory castables?
Silica powder is added to the refractory castable to supplement the tiny pores. Through the precise particle gradation of ultra-fine powder, the strong performance of the castable is improved.
The strength of refractory castable comes from high alumina cement, and the CaO in high alumina cement reaches 5% to 8%. It will reduce the medium temperature strength of refractory castables. If the amount of low melting material is large at high temperature, it will also reduce the high-temperature performance of refractory castable. The CaO in high-alumina cement will produce hydration, and the amount of water used will increase after hydration. If the amount of water is large, the castable structure will become loose. If the superfine powder is added, the cement content in the castable can be reduced to 6%. Reduce the CaO and water consumption in the high alumina cement, thereby increasing the strength of the castable. This is the importance of silica powder in refractory castables.
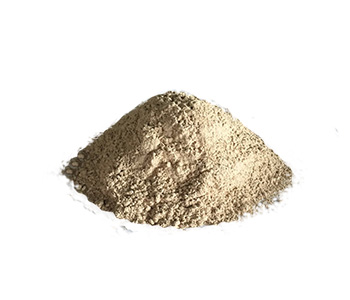
Silica powder is an essential raw material in refractory castables. Adding silica powder to the castable will increase the flow value of the castable. The silica powder has a small particle size and is a spherical particle, which is extremely easy to enter the tiny voids of the castable. Therefore, adding silica powder has good water reducing effect. It can also increase the density of refractory castables and reduce porosity. So that the strength of the refractory castable is better.
The compressive strength of the refractory castable after adding silica micro powder will also change significantly at different temperatures. The initial strength is 110°C, and the medium temperature strength is 1100°C. Due to the fineness activity of SiO2 powder and the fluxing effect of CaO and other impurities in the refractory castable, a strong ceramic bond will be produced. When the high-temperature strength is 1450℃, the silica powder and the alumina powder will form mullite at high temperatures. The porosity of the refractory castable is reduced and the high-temperature strength is better.
α-Al2O3 Powder
The α-Al2O3 micro powder is made after calcining industrial alumina. Its characteristics are good dispersibility, small particles, easy sintering at high temperature, and small volume effect. Adding a certain amount of α-AL2O3 micro powder in refractory castables has a significant impact on its construction performance. Adding an appropriate amount of α-AL2O3 micro powder to the castable can improve the refractoriness of the refractory castable, and cause caramelization and multimerization reactions at high temperatures. On the other hand, it plays the role of filling micro powder and reduces the porosity of the castable. This reduces structural defects in the castable, improves its strength and resistance to slag erosion, and improves the overall performance of refractory materials.
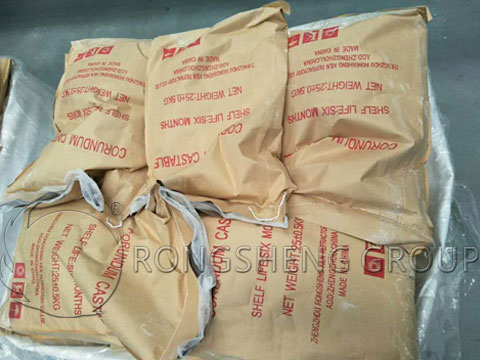
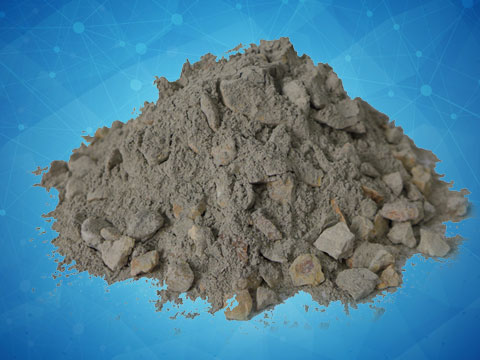
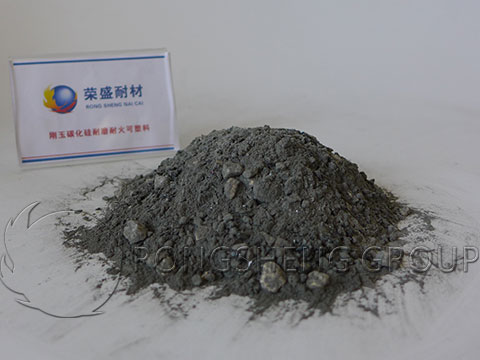
Rongsheng Refractory Castable Manufacturer
As a manufacturer of refractory castables, Rongsheng’s unshaped refractory workshop is equipped with advanced, fully automatic production lines. The annual output of 80,000 tons. According to different kiln types and operating conditions, we configure exclusive monolithic refractory formulations for customers. The types of products we have sold include wear-resistant refractory plastics, corundum castables, corundum mullite castables, refractory mortar, refractory ramming materials, etc. Want to know more about Rongsheng refractory manufacturers, or you need to buy monolithic refractory products. Please contact us, we will provide you with services according to your specific needs.