For some large rotary kilns, the heat load on the lower part of the Kiln Hoods is relatively high. If the general high alumina castable refractory is not well maintained and temperature rise controlled, they are prone to bursting and falling off. The top of the Kiln Hoods is close to the tertiary air duct, and the dust-laden airflow is relatively serious. Moreover, the construction of the top castable is relatively difficult, and the fluidity and early strength of the material are relatively high. Rongsheng refractory castable cement manufacturer recommends that the Refractory Material for Cement Rotary Kiln Hoods adopts high-strength wear-resistant castables with good high-temperature performance, strong thermal shock resistance, and wear resistance.
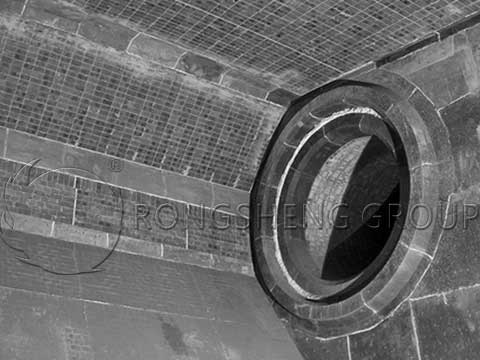
Why use the same refractory material for cement rotary Kiln Hoods and Coolers?
The Kiln Hoods is the kiln head part of the rotary kiln, and the cooler is supporting equipment for the rotary kiln. The top of the cooler has a high working temperature and large temperature changes. The low walls on both sides of the front end are long-term abraded by the high-temperature clinker coming down through the kiln mouth and also endured by certain mechanical and thermal stresses. The operating environment of these two parts is similar. Therefore, refractory manufacturers generally recommend the use of refractory materials of the same material. Rongsheng refractory manufacturers generally recommend the use of refractory castables in these two parts.
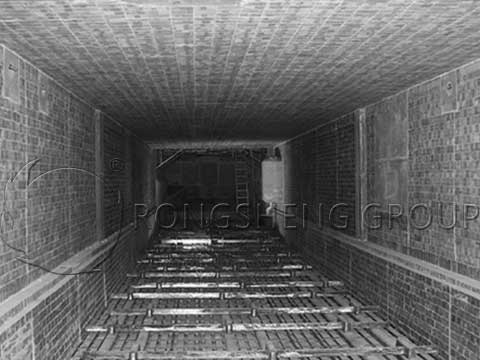
Why should refractory castables be used for kiln hoods and coolers?
According to the use conditions of the Kiln Hoods and coolers described above, the reasons for the use of refractory castables in the Kiln Hoods and coolers can be roughly summarized.
- The refractory castable at the bottom of the kiln hood is subject to the rebound thermal shock of the high-temperature clinker coming down from the kiln mouth. For some large cement kilns, the daily output of the clinker is large, and the heat load on the premises is relatively high.
- The top of the Kiln Hoods is close to the tertiary air duct, and the dust flow is relatively serious, and the castable has better wear resistance at high temperatures. Moreover, the construction of the top castable is more difficult, and the fluidity and early strength of the material are relatively high.
- The bottom of the front end of the cooler is subject to the rebound thermal shock of the clinker, and the working temperature is relatively high and changes greatly. The low walls on both sides of the front end have been long-term abraded by the high-temperature clinker coming down through the kiln mouth and also endured certain mechanical and thermal stress damage.
<To sum up> According to the operating characteristics of the above parts of the cement rotary kiln, it is recommended to use high-strength wear-resistant castables with good high-temperature performance, strong thermal shock resistance, and wear resistance.
Rongsheng refractory material manufacturer provides special kiln hoods refractory castable products for cement kilns. Moreover, Rongsheng manufacturers can adjust the refractory formula of the kiln hoods according to the specific production needs of customers. Let every customer be able to do it in the production process, minimizing costs, and maximizing benefits.
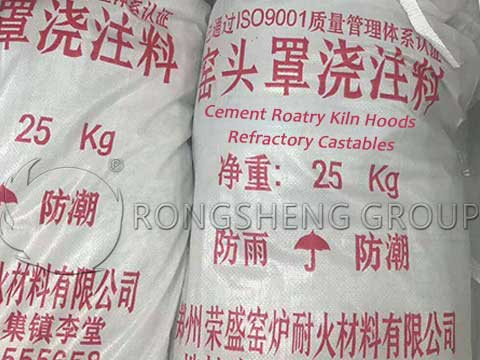
Construction of refractory material for cement rotary Kiln Hoods
General refractory construction plan for Kiln Hoods
- Exhaust holes should be left during the construction of the wall castables, and the holes should be drilled with a gas drill with a distance of 300*300mm. And it is embedded with Φ5mm wooden strips, the depth is half of the castable.
- After the pouring hole of the Cement Rotary Kiln Hood is closed, 8 ventilation holes should be reserved and waterproof function should be ensured.
Construction scheme of kiln hoods ceiling
- Use hanging anchors. Weld it on the L70*70 angle steel at a distance of 250mm*250mm. The angle steel is welded to the longitudinal I-beam of the original Kiln Hoods steel structure. The angles are arranged at a pitch of 250mm.
- The mold is supported from below. Before supporting the mold, paste F10D aluminum silicate fiber cotton on the vertical surface of the surrounding old castable with high-temperature bonding powder (BP-1).
- When pouring, pouring the castable in the order of ABCDEF. Then paste F10 aluminum silicate fiber cotton on the end surface with high-temperature bonding powder (BP-1).
- During the pouring process, use the H100 calcium silicate board for laying. Or after pouring, use high-strength lightweight heat-insulating castable (HN-1.3 or Q1.3) for complete covering pouring (δ=1000mm).
- After all, pouring is finished, use ordinary steel plate with δ=3mm to cover the surface (pay attention to the waterproof of the lap joint). And cut holes and weld steel pipes to leave several ventilation holes.
The technical scheme of brick masonry for kiln door cover vault
- Brick supporting board at the bottom of the arch on both sides of S and N. When the brick supporting board at the bottom of the arch on both sides of S and N burns more than 1/2 the thickness of the brick, the brick supporting board should be replaced in time. Its specifications: 4150mm*330mm*10mm. If time permits, remove the old board before welding. If time is tight, weld directly on the original pallet. The fixed three sides are required to be fully welded and the working surface is flat.
- Refractory brick masonry. The vault has a total of 17 rings of refractory bricks, which are built with the refractory mortar, and the mortar joint is controlled at 1mm. Before laying, the line must be laid out, three in the axial direction, three in the circumferential direction, and four in the circumferential direction. The masonry of refractory bricks must be based on this line.
Masonry of insulation bricks
- Build a layer of 114mm thick insulation brick on the above refractory bricks, using insulation refractory mortar. There are 3 models (230*114*55/65mm or (60/65 or 65/65)) to match and concentrically build with refractory bricks.
- The masonry of insulation bricks should be synchronized with refractory bricks. The upper gap is filled with aluminum silicate fiber cotton to facilitate the wedging of the rear refractory bricks.
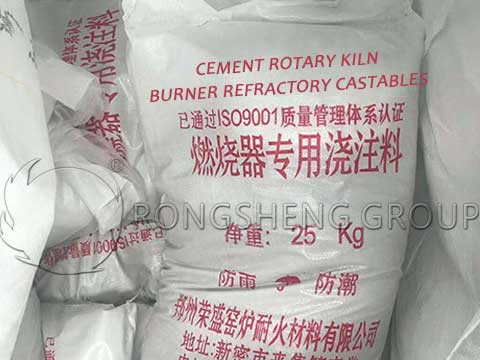
Rongsheng Refractory Castable Manufacturer
Rongsheng is an advanced refractory castable manufacturer with a fully automatic and environmentally friendly refractory castable production line with an annual output of 80,000 tons. Has served customers in more than 60 countries and regions, for example, India, Pakistan, Kuwait, South Africa, Malaysia, Vietnam, Netherlands, Philippines, Singapore, Egypt, Russia, etc. Rongsheng has customized kiln hoods’ refractory castables, burner refractory castables, high-alumina high-strength refractory castables, and high-strength wear-resistant castables for cement rotary kilns. The product quality and customer service of Rongsheng’s unshaped refractories are leading in the industry. Get more product quotations on refractory material for cement rotary kiln hoods. Please leave your contact information and specific requirements on our website page. We will provide you with refractory materials that best suit your production needs according to your actual working conditions. Save production costs and improve economic efficiency.