Plastic is a refractory material that was developed and applied earlier and is mainly used in heating furnaces, electric furnace tops, and other parts. Due to its shortcomings such as short storage time and poor fire resistance, its application range is limited. However, this refractory material has some irreplaceable advantages, such as the high-temperature strength of the furnace body constructed with plastic, excellent thermal shock resistance, low thermal conductivity, and flexible construction methods.
Selection of Refractory Plastic Aggregates
Refractory plastics should have excellent plasticity, moisture retention, and high-temperature performance. To meet these conditions, it is very important to select suitable raw materials. The raw materials should have good volume stability. During the heating process, they can be well-sintered and reacted with binders such as clay. Aggregates should have appropriate particle size and grading. Generally, the critical particle size of refractory plastic aggregates is less than 10 mm, the aggregate content is 55% to 65%, and the powder content is 35% to 45%. Through strength tests and moisture retention tests, it was found that although the plastic produced with grade 3 high aluminum and grade 2 high aluminum as the main raw materials has a higher strength after burning, the moisture retention of the material is poor. Therefore, it is determined to use special grade high aluminum alumina as the main raw material, and it is required to be sintered densely and have a low impurity content. In order to improve the moisture retention performance, the iron oxide content in the material should be strictly controlled.
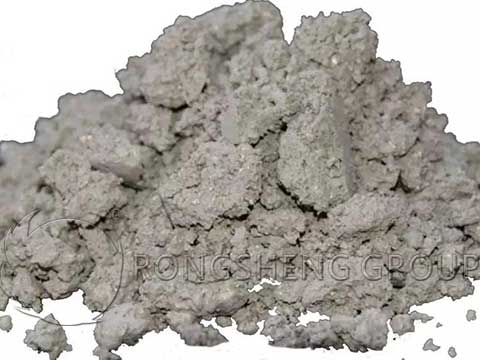
Effect of Clay and Powder Addition on the Performance of Refractory Plastic
Binding clay is added to plastic, which mainly plays a bonding role and improves its plasticity and sintering performance. The particle size of clay should generally be less than 200 mesh. Its dosage should be minimized while ensuring the plasticity and bonding ability of plastic. If too much is added, the linear shrinkage of plastic will increase after high-temperature firing, the load softening temperature will decrease, and the high-temperature creep will increase. If the amount added is too little, the plasticity of the material cannot be guaranteed. Through experiments, it is determined that the amount of clay added is 5% to 15%. In order to reduce the linear change of plastic after firing, an appropriate amount of kyanite is added. Since kyanite produces volume expansion at high temperatures, it can offset part of the shrinkage of plastic. Its fineness is 150 mesh, and the amount added is controlled at about 5%. In order to improve the plasticity and thermal shock resistance of plastic and further reduce the impurity content in the raw materials, alumina powder, and silicon powder are added. This can not only improve the construction performance of the material but also increase the medium and high-temperature strength of the product. The total amount of the two is generally controlled at 6% to 12%, which is more reasonable.
Through experiments, it is found that when the plastic index is around 14%, the plastic is relatively hard and the construction performance is poor. When the plastic index is around 26%, the plastic feels softer and the construction is easier. In order to facilitate construction and meet the requirements of other performance indicators. Through repeated experiments, it is confirmed that the plastic index of the plastic is about 28%.
Selection of Fire-Resistant Plastic Binder
In order to make plastic have higher strength and excellent moisture retention performance, various binders were tested, such as phosphoric acid, water glass and aluminum sulfate. Through experiments, it can be proved that plastic with phosphoric acid as binder has higher strength index. However, due to the strong acidity of phosphoric acid and the high iron oxide content in the raw material, phosphoric acid can easily react chemically with iron oxide, which makes the moisture retention performance of plastic worse. Using aluminum sulfate as a binder, plastic has a longer moisture retention performance, but the strength index of plastic cannot meet the use requirements. Using water glass as a binder, the moisture retention performance of the material is better in the short term, but after a long storage time, the construction performance of plastic deteriorates. In addition, when the plastic combined with water glass is baked, the hard shell produced on the surface will have an adverse effect on the strength of the plastic construction body. Through repeated experiments, it was determined that the two binders of phosphoric acid and aluminum sulfate were used in combination, so that the moisture retention performance and strength index of the plastic can meet the use requirements.
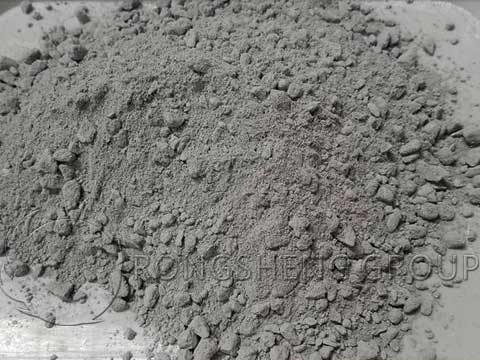
Factors Affecting Moisture Retention Performance
Influence of aggregate types
Through continuous moisture retention experiments, it was found that the moisture retention performance of plastics with high-aluminum from special downdraft kilns as aggregates is significantly better than that of plastics with other low-grade aggregates. This is due to the dense sintering of special-grade aggregates and the low water absorption rate of particles.
Influence of binder types
Binders have the greatest impact on the moisture retention performance of plastics and also play a key role in other properties. If improperly selected, plastics will not meet the requirements of use.
Through experimental research on the moisture retention performance and compressive strength performance of the test blocks, as well as comprehensive considerations such as raw material costs, phosphoric acid, and aluminum sulfate were finally selected as composite binders. This can not only meet the moisture retention performance requirements of plastics but also meet the requirements of medium and high-temperature strength.
Effect of admixture types
Experiments show that adding organic acids (such as oxalic acid) and dextrin and other admixtures can prevent or delay the reaction between the binder and the refractory material, and play a role in extending the moisture retention of plastic. Some admixtures are oily and can effectively reduce the agglomeration of plastic, which mainly extends the moisture retention of the material from a physical aspect. Oily moisturizers and main binders such as phosphoric acid are not miscible but can reduce the chance of chemical reactions between phosphoric acid and raw materials, making the moisturizing effect better.
When used in furnaces such as heating furnaces and annealing furnaces, plastic has certain advantages over castables. It does not require on-site mixing equipment and can be directly constructed. It has a large viscosity and does not flow. It is easier to combine with the old lining during repair, and local repairs can be performed without templates. Because it has a low water content, the requirements for baking conditions are not very strict.
Conclusion
- (1) Using high-grade downdraft kiln high-alumina bauxite as the main raw material can significantly improve the moisture retention performance of plastics.
- (2) Using phosphoric acid and sulfuric acid in a composite form, and adding an appropriate amount of additives, plastics with relatively good moisture retention and strength indicators can be produced. The effect of using a single combination is not ideal.
- (3) Select high-grade high-alumina bauxite with dense sintering and low impurity content to minimize the iron oxide content in the material. In addition, adding an appropriate amount of moisturizing agent can significantly extend the moisture retention period of plastics.
Rongsheng amorphous refractory castable manufacturer can provide high-quality amorphous refractory lining materials for high-temperature industrial furnaces. If you need to purchase refractory plastics to extend the service life of refractory furnace lining materials. Please contact Rongsheng for free solutions for high-temperature industrial furnace linings.