Alumina Magnesite Refractory Castable is a refractory castable with corundum as the aggregate, spinel and corundum powder as the matrix and pure calcium aluminate cement as the binder. Its chemical composition is Al2O3 89%~93%, MgO 5%~8%. It has good corrosion resistance and slag penetration resistance and can be used as a large ladle lining for continuous casting.
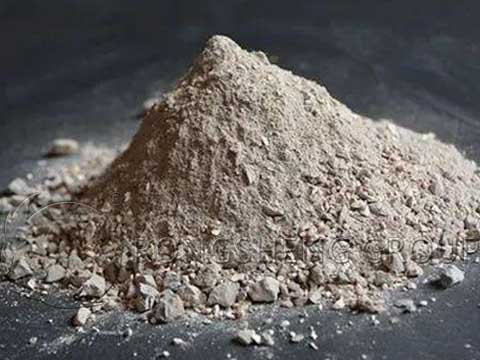
Application of aluminum-magnesium refractory castable
Aluminum-magnesium refractory castables have been widely used in ladles for medium and small die-casting. The average package age is 60 to 80 times. Compared with clay ladle bricks, the refractory material consumption per ton of steel is reduced by about 70%.
The raw materials of aluminum-magnesium castables for ladles are basically the same as that of aluminum-magnesium refractory ramming materials. In order to obtain normal temperature strength, sodium fluorosilicate should be added as coagulant. The load softening temperature of the ladle aluminum-magnesium castable is low, which is due to the combination of some low-baking substances formed by adding magnesia powder and the joint action of water glass and sodium fluorosilicate.
The solution to cracks in aluminum-magnesium castables during use
Aluminum-magnesium castables crack during use, which reduces the service life. The specific manifestation is: when the ladle is used for 5 heats, cracks begin to appear on the inner wall of the ladle, covering the entire ladle wall. As the number of uses increases, the cracks become deeper and wider. When more than 20 furnaces were used, they had to be forced to stop using them. In order to solve the problem of castable cracks, the following methods have been tried.
- (1) Replace the bauxite clinker calcined by the shaft kiln with the bauxite calcined by the downdraft kiln, so that the sinterability and bulk density of the bauxite are increased. The theory was that this might reduce volume shrinkage caused by incomplete calcination of alumina and re-sintering during use, but without success.
- (2) It is believed that the cracks are related to the total amount of fine powder in the castable. Try to reduce the fine powder in the castable to less than 30% (mass fraction), the lowest to 25%. Didn’t solve the problem either.
- (3) Start to solve the crack from the chemical reaction. Because Al2O3 and MgO can generate aluminum-magnesium spinel under high temperature, accompanied by large volume expansion. After a series of experiments, adjusting the ratio of Al2O3/MgO did not achieve satisfactory results. Even when the MgO content is too high, peeling occurs instead.
Solution: Finally, the following method was adopted to basically solve this problem.
- (1) The upper limit of the aggregate particle size was raised from 15 mm to 5 mm, of which 20-25 mm accounted for 7.2% (mass fraction) of the total. This is due to the existence of super-large particles, which not only act as a skeleton, but also can change the direction of long cracks, helping to prevent the expansion of internal cracks.
- (2) Add zircon powder into the matrix. This zircon powder is produced in Australia, and the ZrO2 content is about 66%. Since ZrO2 itself has a high melting point, it can absorb CaO in slag during use to generate CaZrO3 with high melting point and high corrosion resistance, which can close pores and cracks and strengthen the matrix. At the same time, due to the existence of zircon, micro-crack structures can also be formed in the castable, improving the high-temperature performance of the castable.
- (3) Reduce the amount of active silica fume powder as much as possible. Since the quality of silica fume powder is unstable, if the amount added is large, there will be many impurities brought in, which is unfavorable for use. It is better to control the amount of silica fume in the castable below 1.5% (mass fraction).
- (4) When pouring, it is also critical to strictly control the amount of water added and ensure uniform vibration.
Rongsheng Refractory Castable Manufacturer
Rongsheng refractory castable manufacturer is a powerful monolithic refractory manufacturer. Rongsheng Environmental Protection’s advanced fully automatic monolithic refractory production line has an annual output of 80,000 tons. Provide high-quality monolithic refractory products for thermal equipment of various furnace structures such as circulating fluidized bed boilers, gasification furnaces, fluidized furnaces, and waste incinerators. Our refractory products have been sold to more than 70 countries all over the world, such as South Africa, the Philippines, Chile, Malaysia, Indonesia, Vietnam, Kuwait, Turkey, Zambia, Peru, Mexico, Qatar, Egypt, Russia, Kazakhstan, etc. To purchase high-quality aluminum-magnesium refractory castables and get free refractory castable lining configuration solutions, please contact us. We will provide you with the configuration of refractory lining material that best suits your production needs.