The temperature of the shell of industrial kilns varies, and the higher the operating temperature, the higher the temperature of the shell of the kiln. In recent years, due to the requirements of environmental protection and the advocacy of energy conservation, industrial kiln enterprises have paid more and more attention to the temperature of the outer wall of the kiln skin. So how to reduce the temperature of the outer wall of the kiln skin? To reduce the surface temperature of the kiln skin, how to use insulating castables?
Generally, if you want to lower the temperature of the kiln skin, you must improve the use of insulation materials, or thicken the insulation layer. There are many light clay bricks and light fiberboards, cotton wool, and blankets used for the insulation layer. If you use fiber insulation materials, you don’t need lightweight clay bricks, and you can’t use fiber insulation materials if you use lightweight clay bricks. However, if it is required to reduce the temperature of the kiln skin, it is necessary to do multi-layer insulation to reduce the degree of heat diffusion and reduce the temperature of the outer wall of the kiln.
What kind of material should be used as the insulation layer when the kiln skin temperature is required to be 50°C?
When the temperature of the kiln skin is required to be 50°C, insulating castable refractory can be used, and fiberboard can also be used as the insulation layer.
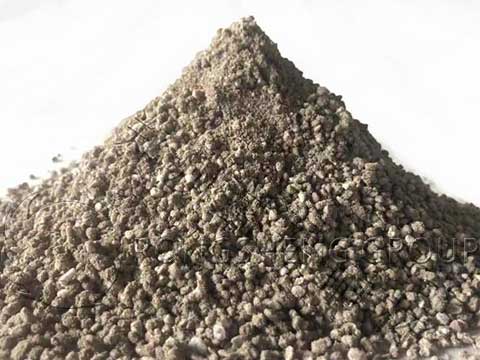
The kiln skin temperature is required to be 50°C, and the temperature requirement is relatively low. If you choose fiberboard, it is not enough to use ordinary aluminum silicate fiberboard, you have to use nanometer board as an insulation layer. And it doesn’t work if it’s too thin, the minimum thickness should be 100mm. It is uncertain whether the final kiln skin outer wall temperature reduction effect will reach 50°C on the outer skin. If it is winter, it should be able to meet expectations. If it comes to summer, the temperature of the outer wall of the kiln skin may be 50℃ higher due to the influence of sunshine and weather temperature. This is affected by certain weather factors. If you use a 150mm nanoplate, there is no big problem.
If you use lightweight castable refractory, some costs will be reduced, but the thickness should not be too small. Under normal circumstances, the thickness reaches 300mm, and the temperature of the outer skin can also be lower than 50 degrees Celsius. However, the thickness of the lightweight castable is too thick, which will affect the kiln diameter. Because the insulation layer with a thickness of 300mm, a total thickness of 600mm must be occupied on both sides of the kiln. Therefore, the usable kiln diameter will become smaller. However, from the perspective of heat preservation alone, if it is expected to reduce the temperature of the kiln skin, the temperature required by the kiln skin can also be achieved by pouring 300mm thick lightweight heat-insulating castables.
If the height of the kiln is too high, it is unlikely to use refractory bricks for the insulation layer or the working layer. Because there may be string joints in the middle, the working layer is most likely to be poured with dense castables as the working layer. It is possible to use nano-sheets or lightweight castables for the pouring working layer. Because the outer layer of the nano-plate is wrapped with plastic, no moisture will enter, and even if the castable discharges a certain amount of water, the thermal insulation layer will not be affected. If light heat insulation castables are used and dense castables are used in the working layer, they are all constructed by pouring, and there is no problem of water discharge affecting the use of the heat insulation layer.
Therefore, when the external temperature of the kiln skin is low, it is possible to use nano-plates and lightweight insulating castables. Only the thickness has certain requirements. The thickness of the nano-plate should not be less than 100mm, and the thickness of the lightweight castable must be constructed to a thickness of 300mm to meet certain usage requirements.
Can Lightweight Insulating Castables be Used Outside the Furnace Shell?
Lightweight insulating castables are used on the outside of the furnace shell and are not recommended. Because the lightweight insulating castable refractory plays the role of heat preservation and heat insulation, the main function is slowing the heat dissipation, which can save fuel and protect the furnace shell.
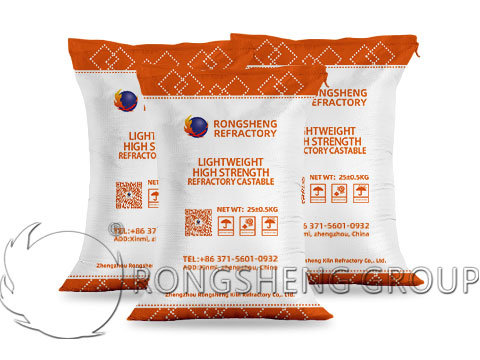
If the furnace lining is not used as an insulation layer during construction, it is not recommended to use it in this way. If there is a user unit that has not made an insulation layer and has been put into production, under such conditions, in order to avoid overheating of the furnace shell, it is not advisable to make an insulation layer on the outside of the furnace shell, and then add a layer of the iron sheet on the outside.
The reason is that there is no insulation layer and the temperature of the furnace shell is high. The insulation layer can be used for the next maintenance. If an insulation layer is made on the outside of the furnace shell and a layer of iron sheet is added, the furnace shell will also be attacked by high temperature and the service life will be shortened.
There is a furnace type with heat-insulating material coated on the outside of the furnace shell. Due to the high temperature of the boiler, heat-insulating castables or heat-insulating bricks are used as heat-insulating layers on the inner lining. Some manufacturers also apply a layer of fabric on the outside of the furnace shell, which also slows down the temperature and heat dissipation process. This saves fuel and protects the furnace shell. There are also manufacturers who use a layer of epoxy paint on the outside of the furnace shell, but not many use this method. On the contrary, more fabrics are used.
If the inner lining is made of light-weight insulating castable or light-weight bricks as the insulation layer, if the insulation layer is made outside the furnace shell for remedy, it will not play any role in the protection of the furnace shell, and it is of little significance to make the insulation layer. Even doing it with nanoplates doesn’t make much sense.
Therefore, the selection of lining materials must be determined according to the temperature of the lining. Whether to use lightweight insulating castables refractory or lightweight refractory bricks or use insulation cotton and boards as insulation layers. If the furnace lining temperature does not exceed 200°C, there is no need to make an insulation layer. If the temperature exceeds 1000 ℃, it is necessary to make an insulation layer. If the temperature exceeds 1400°C, high-grade lightweight materials should be used as the insulation layer.

Solutions to Reduce Kiln Skin Surface Temperature
Rongsheng refractory material manufacturer is a manufacturer with rich production and sales of refractory materials. Our monolithic refractory materials offer reliable performance. It has a long service life on the refractory lining of various industrial kilns. Extend the service life of the refractory lining. Recently, our technical team is also working on the research of refractory materials that reduce the surface temperature of the kiln skin, providing cooling solutions for industrial kilns. Contact us for a free solution.