The castable for ladle, in terms of material, was originally based on “Zirconia-Silicon” stone. However, with the requirement of clean steel and the increase of secondary refining, the high-durability alumina spinel is gradually adopted. During this period, tests were also done on magnesia-based alkaline materials, but they were not put into practical use due to the inability to suppress structural peeling. Therefore, in terms of extending the service life of the ladle, understanding the damage mechanism of the castable for the ladle is a very important link. Refractory manufacturers and steel mill customers have conducted a series of studies on the damage pattern of the castable for ladle.
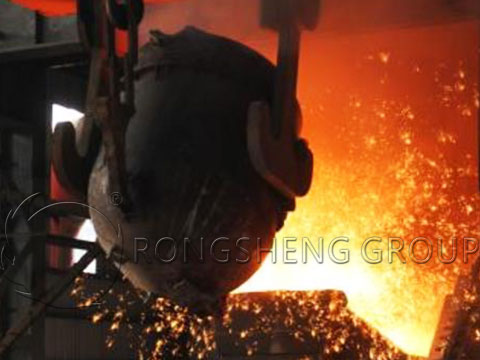
The Damaged Appearance of Castable for Ladle
Regardless of shaped or unshaped refractories for ladle, the slag line, molten steel parts, and the bottom of the ladle will be damaged to varying degrees.
Damage to the slag line
At the position equivalent to the “slag-steel” interface, the damaged surface is smooth and deep with a clear outline. The reason for making it smooth is that the damage is mainly corrosion, but there are also cracks. Recently, due to the use of alumina spinel castables, satisfactory durability has not been obtained. Therefore, magnesia carbon bricks are mostly used. The damage rate is 1~2mm/furnace, and it needs to be repaired after about 100 furnaces are poured.
Damage to the molten steel
The corrosion damage is very small under the current materials and uses conditions, and the cracks and the peeling caused by their expansion are the main damages. Repeated peeling affects the life span. On average, the damage rate of “zirconium-silica” stone is 1 mm/furnace, and alumina spinel is 0.3~0.5mm/furnace. Now the most durable alumina spinel has a life span of 250 to 300 furnaces. Since the molten steel part is the main part that determines the life of the ladle, the damage of this part needs to be paid attention to.
The bottom of the package is damaged by the steel part
Due to the impact of molten steel, the steel parts during pouring steel wear and then develop into cracks, where molten steel penetrates to affect the service life. Use alumina castable prefabricated block, which needs to be repaired after about 100 times of pouring.
Damage Patterns of Refractory Materials for Ladle
The characteristics of the damage of the castable are that although there is no damage to the brick joints, cracks of varying sizes and seldom occur hot spalling instead. The damage of ladle castables is also the same as before, which can be divided into the following three aspects.
- Corrosion, continuous loss caused by surface or internal melting.
- Mechanical wear, loss caused by the impact of molten steel, etc.
- Spalling, falling of refractory lining caused by high temperature, machinery, structure, etc.
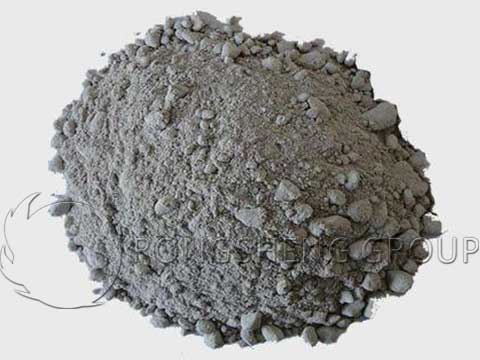
It is rare that corrosion is the main factor in molten steel. At the part of the molten steel where the working face is spalled in layers, the structural spalling caused by slag penetration, that is, the cracking caused by the structural thermal stress is the main cause of damage. However, for alkaline materials and some alumina spinel castables, cracks also occurred in the original layer, and thermal spalling occurred, mainly due to the cracks caused by the concentration of thermal stress.
The temperature of molten steel, the composition of slag, and the residence time of molten steel have a great influence on the damage of refractory materials. After discovering the damage of the refractory layer of the ladle, the analysis of the related damage mechanism will be of great help to prolong the service life of the ladle. To purchase refractory castable for ladle, please contact the refractory castable manufacturer.