Rongsheng Refractory Castables is a refractory material manufacturer with rich production and sales experience. Rongsheng, based on years of production and sales experience, can customize refractory lining solutions for high-temperature industrial furnace linings. The determination of the thickness of high-temperature refractory castables mainly depends on the working environment temperature, material properties and usage requirements. Contact Rongsheng for detailed information.
Working environment temperature: The working environment temperature is the most important factor in determining the thickness of refractory castables. The higher the temperature, the greater the castable thickness required to withstand the thermal stress at high temperatures.
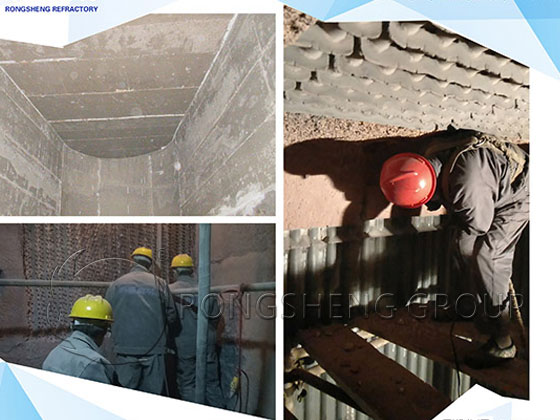
Material properties: Refractory castables of different materials have different refractory properties and thermal expansion coefficients, and the differences in these properties will directly affect the choice of thickness. For example, the thickness design ranges of light and heavy materials are 10-200mm and 200-300mm respectively.
Usage requirements: Usage requirements are also an important factor in determining thickness. Some projects may require that the castables not only withstand high temperatures but also have corrosion resistance, which requires a more sophisticated design.
Recommendations on the thickness of refractory castables in different application scenarios
Ladle: The thickness of the working lining is usually 100-150mm, and the thickness of the coating layer is 10-15mm.
General furnace type: The thickness is generally 200-230mm, and there are also designs of 150-200mm thick according to the location conditions.
Special requirements: If the furnace weight needs to be reduced, it can be designed to be 80-100mm thick, but the service life will be shortened accordingly.
As the amount of refractory castables continues to increase, the scope of use is also getting larger and larger. However, the thickness of different refractory castables and the thickness of spray coatings and coatings are different.
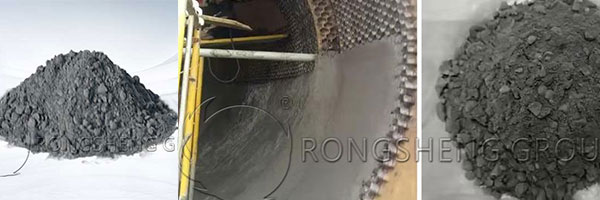
The thickness of heavy refractory castables or refractory concrete cannot be less than 100mm. If it is less than 100mm, the service life of heavy castables will be affected. The most suitable thickness is 200mm. When there are certain restrictions on the use of some parts, it is also possible to pour at a thickness of not less than 100mm, and of course 150mm is also possible. If conditions permit, it is best to pour 200mm.
Of course, some user manufacturers require that refractory castables be poured at 220mm? Of course. Generally, 200mm is suitable. If 220-250mm is OK, the service life will be longer. If the user requires the refractory castable to be poured at a thickness of 50mm, be sure to tell the user that 50mm castables are not possible. Not only does it affect the service life, but also because the particles of the refractory castables are large and the thickness is too thin, it will not work at all.
The pouring thickness of lightweight refractory castables cannot be less than 80mm. If there is no specific restriction on the location of use, pouring 100-150mm is most appropriate.
There are also some user manufacturers who cannot distinguish whether to use refractory castables for pouring, coating or spraying. They should first ask the required thickness of pouring or spraying, and give users suggestions on using castables or spray coatings and coatings. The thickness of spray coatings and coatings is 30-50mm, usually 50mm is the most suitable. Too thick spray coatings or coatings will cause delamination, and too thin will affect the service life.
Therefore, as long as the user requires 30-50mm thickness, spray coatings or coatings must be used.
There are also refractory plastics, and the thickness is the same as spray coatings and coatings, 50mm is the most suitable. If 80mm is used for a specific temperature and environment, it can also be used, but the thickness cannot exceed 80mm. Too thick will also cause delamination and affect the service life.
Suggestions for the construction and maintenance of refractory castables
- During construction, adjustments need to be made according to the specific parts and conditions to ensure the versatility of the construction parts.
- In actual construction, the thickness selection needs to be adjusted and optimized according to the specific situation to ensure the quality and safety of the project.