Circulating fluidized bed boiler refractory lining. Material circulation path in circulating fluidized bed furnace. Pulverized coal (generally with a particle size of 0~10mm) and limestone powder are fed into the fluidized bed combustion chamber (dense phase area) through a feeder, and the fuel boils and burns in this area. The flue gas rises, passes through the dilute phase zone to the separator inlet and enters the cyclone separator. The coarse particles sink and return to the combustion chamber through the return valve for combustion again. The flue gas carries the fly ash and rises through the convection flue into the external heat exchanger. Refractory materials are mainly lined in the combustion chamber, ceiling, separator inlet, high-temperature cyclone separator, and return valve.
Taking a 220t circulating fluidized bed boiler in a certain factory as an example, the working conditions of the refractory materials in each part are as follows.
- (1) Dense phase area. The depth of this area is 220~1530mm. A 2100mm long sandy medium (pulverized coal and limestone powder) is boiled here. The pressure in this area is 13818~20580pa, the flue gas flow rate is about 1.2~1.8 m/s, and the normal operating temperature is 820~900°C.
- (2) Dilute phase area. The area above the secondary air outlet is where the fine particles of fuel combustion are concentrated. The solid material concentration here is about 12~16kg/m3, the flue gas flow rate is 1.2~3 m/s, and the normal operating temperature is 930~980℃.
- (3) Stovetop area. The normal operating temperature is 850~1100℃, and the flue gas flow rate increases by 18m/s at the separator inlet.
- (4) Cyclone separator. The normal operating temperature is 850~930℃, and the flue gas flow rate at the cyclone outlet can reach 29m/s.
- (5) Cyclone separator air outlet main pipe. The dust content of the flue gas here is 70~530g·m-3, the normal operating temperature is 850-930°C, and the maximum flue gas flow rate is 18m/s.
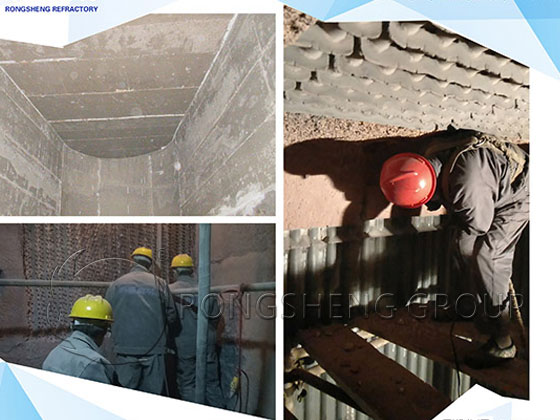
According to the design requirements, the average working time of the boiler is 8600 hours, and the boiler starts and stops 2 to 10 times a year. Each ignition takes 12 to 24 hours. After ignition, the temperature is raised to 800°C at a rate of 65°C/h and kept warm for 8 hours. The service life of the furnace lining is required to be at least 2 years.
Circulating Fluidized Bed Boiler Refractory Materials
(1) Medium temperature, the working temperature of each part of the circulating fluidized bed boiler lining is 800~1000℃. From the perspective of refractory materials, this belongs to the medium-temperature range. When selecting refractory materials, first consider the medium-temperature physical and chemical properties of the material. For fired products, the sintering temperature is generally higher than this temperature range, so its physical and chemical properties at high temperatures can be directly used as a basis for selecting refractory materials. For unshaped refractory materials and unfired products, the physical and chemical properties at mid-temperature must be examined. Organically bonded materials or hydration-bonded hydraulic materials tend to have the worst strength at medium temperatures. These materials create a ceramic bond at high temperatures, which greatly increases their strength. Therefore, its physical and chemical indicators at high temperatures cannot be used as a basis for selecting refractory materials.
(2) Thermal shock. Under normal operating conditions, circulating fluidized bed boilers start and stop 2 to 10 times a year. In the early stages of operation, due to improper operation, the refractory lining was subjected to a strong thermal shock every year when starting and stopping. If the refractory material has poor thermal shock resistance, the spalling of the refractory material caused by thermal shock will become a fatal factor in its damage.
(3) Sand blasting wear, flue gas flow rate in circulating fluidized bed boilers is high (up to more than 29m·S-1), and solid material concentration is high. At medium temperatures, high-speed flue gas entrains a large number of solid particles, causing strong erosion and wear on the refractory lining. Especially in the impact zone of the cyclone, the erosion is most serious. For circulating fluidized bed boilers and cyclones with single-side return, the cyclic flow of materials causes wear areas on the refractory lining walls.
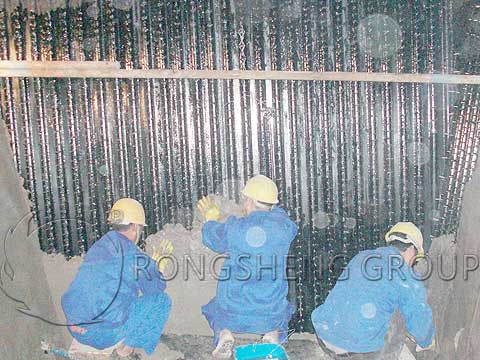
Causes of Wear of Refractory Materials in Circulating Fluidized Bed Boilers
(1) Wear caused by thermal stress and thermal shock. Wear caused by thermal stress and thermal shock mainly manifests as cracks and spalling of refractory materials caused by temperature cycle fluctuations, thermal shock, and mechanical stress.
(2) Wear caused by erosion of solid materials. The wear caused by the erosion of solid materials is mainly the damage caused by the strong erosion of refractory materials by materials. The wear areas of refractory materials in circulating fluidized bed boilers include corner areas, cyclone separators, and solid material return paths. In general, refractory material wear increases with the increase of impact angle.
(3) Wear caused by changes in the properties of refractory materials. Wear caused by changes in the properties of refractory materials is mainly manifested as damage caused by the deterioration of refractory materials and the reduction of physical and chemical properties. The main manifestation is that the penetration of alkali metal causes the deterioration of refractory materials. Some refractories and bonds have lost strength, and some ovens have not met requirements, causing linings to delaminate and collapse.
The above technical guidance on refractory materials for circulating fluidized bed boilers mostly summarizes the requirements for the use of wear-resistant refractory materials from the combustion temperature of the fuel, wear values, theoretical data, etc. Start from the overall performance.
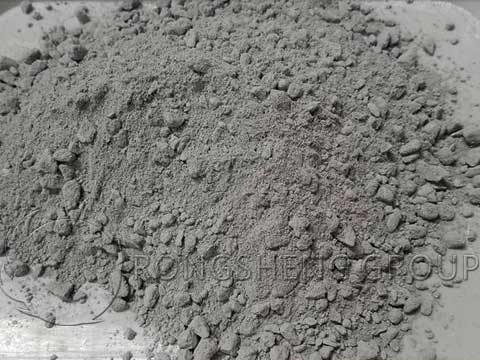
Refractory plastic for circulating fluidized bed boiler repair
Refractory plastics are suitable for the construction of thin parts such as furnace water-cooled walls. It is mainly used in the dense phase area of the furnace and steam-cooled and water-cooled cyclone separators.
The wear-resistant refractory material in this area is designed as a single-layer ramming structure and is fixed with wear-resistant pins. Its design thickness is thin and can be laid directly on the construction surface.
In the application of repairing circulating fluidized bed cyclone separators, it’s super strong bonding performance can repair any irregular wear parts at will. There is no need to use steel formwork or moulds, and it can be ignited immediately after construction is completed without special maintenance. Thereby shortening the construction period and saving costs.
Refractory materials for circulating fluidized beds, refractory plastics for circulating fluidized beds, wear-resistant refractory castables, etc. RS refractory material manufacturer can provide high-quality refractory materials products and comprehensive customer service. Product quality is guaranteed and the delivery cycle is short. Effectively ensures the long life and safe operation of high-temperature industrial furnace linings.