Micro-expansion refractory plastic is made of water glass as a binder and sodium fluorosilicate as a coagulant. It was originally used in wall-through pipes of pulverized coal furnaces. It has the characteristics of strong plasticity at room temperature, strong adhesion, high fire resistance, good sealing performance, and convenient construction. It has high strength after natural drying, and its volume can expand slightly at high temperatures. It can be widely used in industrial kilns such as CFB boilers and pulverized coal furnaces, such as top wall-penetrating pipes, flame angles in the furnace, complex parts of the furnace wall, etc. It mainly plays a sealing role. Currently, this material can be used in boiler flues, chimneys, and other pipes containing acidic gases.
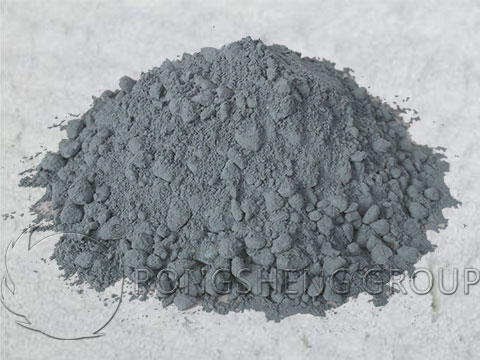
Micro-Expansion Refractory Plastic for Power Plant Boilers
With the continuous development of modern industry, the power industry plays an increasingly important role in people’s lives. As an important part of power plant boilers, the performance of the lining material has a great impact on the operating efficiency and life of the boiler. Therefore, the emergence of micro-expansion wear-resistant and refractory plastic has become an important lining material and is favored by power plant boiler manufacturers and maintenance engineers.
Micro-expansion wear-resistant refractory plastic has the characteristics of low thermal conductivity, high-temperature resistance, good thermal shock stability, wear resistance, corrosion resistance, and not susceptible to mechanical vibration. Its obvious feature is that under high-temperature conditions, the formation of an oxide layer can effectively protect the lining material, thereby extending the service life of the boiler. In addition, the micro-expansion properties allow the material to have better crack resistance and wear resistance at high temperatures, further improving the boiler’s operating efficiency and performance.
In the application of power plant boilers, micro-expansion wear-resistant, and refractory plastics are widely used in lining materials, patch materials and supplementary materials. As a lining material, it replaces traditional hard materials and can reduce the noise and vibration of the boiler and extend the life of the boiler. Patch materials are often used for boiler lining repairs and will not peel off the base material or affect thermal conductivity during the repair process. Supplementary materials refer to adding micro-expansion wear-resistant refractory plastic to the lining of the boiler to improve overall performance and life.
In short, the application of micro-expansion wear-resistant and refractory plastics in power plant boilers has become a trend. It is known for its high performance and excellent fire resistance. The range of applications is getting wider and wider. In the future, we believe that this material will play a more important role in the power industry and continue to provide a strong guarantee for the operating efficiency and performance of boilers.
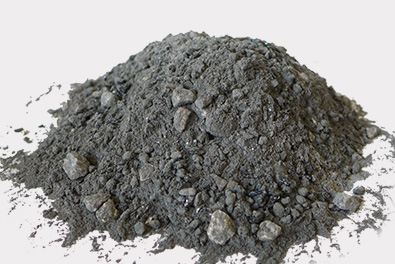
How to Identify Refractory Plastic and Refractory Clay
Refractory plastics are made of refractory aggregates and powders, raw clay, chemical composite binders, and admixtures, which are mixed and extruded into brick shapes. Refractory materials that still have good plasticity after being packaged and stored for a certain period of time can be constructed using the tamping method. Commonly used bonding methods include chemical bonding, ceramic bonding, polycondensation bonding, etc.
Refractory mud, also known as refractory mud or joint material, is a joint material used for the masonry of refractory products. According to the material, it can be divided into clay, high alumina, silica and magnesia refractory clay. It is composed of refractory powder, binder, and admixture. Almost all refractory raw materials can be made into powders used to prepare refractory mud. Ordinary refractory clay, which is made from refractory clinker powder and an appropriate amount of plastic clay as a binder and plasticizer, has low strength at room temperature. Only when it forms a ceramic bond at high temperatures does it have higher strength. Chemically bonded refractory mud, which uses hydraulic, gas-hardening or thermo-hardening bonding materials as binding agents, hardens through a certain chemical reaction before the temperature drops below the temperature at which ceramic bonding occurs. The particle size of refractory mud varies according to the use requirements. Its limit particle size is generally less than 1mm, and some are less than 0.5mm or finer. When selecting the material of refractory mud, it should be consistent with the material of the refractory products of the masonry. In addition to being used as a joint material, refractory mud can also be used as a protective coating for the lining by applying or spraying.
Refractory mud properties and applications. 1. Good plasticity and convenient construction. 2. High bonding strength and strong corrosion resistance. 3. The refractoriness is relatively high, reaching up to (around 1650℃). 4. Good resistance to slag erosion. 5. Good thermal peelability. Refractory mud is mainly used in coke ovens, glass kilns, blast furnaces, and other industrial kilns.
Rongsheng Unshaped Refractory Material Manufacturer
Rongsheng Refractory Castable Manufacturer is a powerful manufacturer and seller of unshaped refractory materials. Rongsheng’s environmentally friendly, fully automatic unshaped refractory castable production line reliably guarantees the production and supply of refractory castables for high-temperature industrial furnaces. Rongsheng Refractory Castable Manufacturer already has customers in more than 120 countries, such as South Africa, Chile, Egypt, Colombia, Uzbekistan, Italy, Indonesia, Ukraine, Hungary, Spain, Kenya, Syria, Zambia, Oman, Venezuela, India, Peru, the United States, Ethiopia, etc. If you have the need to purchase unshaped refractory castables, or micro-expansion refractory plastics for power plant boiler maintenance, please contact us. Get free samples and quotes.