The blast furnace iron trench is a channel for guiding high-temperature molten iron and molten slag. Its refractory lining is subject to high temperature, mechanical and chemical erosion by molten iron and slag liquid. The first is the scouring effect on the surface of the refractory material when iron and slag flow. Secondly, due to the frequent alternation of hot and cold during tapping or the long-term action of high temperature, micro-cracks occur in the refractory material. Such microcracks promote the penetration and structural damage of molten iron and slag. Therefore, the iron trench lining material is required to have strong resistance to the erosion of molten iron and slag, good thermal expansion stability, small change in burnt volume, and strong oxidation resistance. It is easy to construct and does not adhere to slag iron, making it easy to repair and dismantle. It has a uniform, highly dense structure and high strength. It does not produce harmful gases and is conducive to environmental protection.
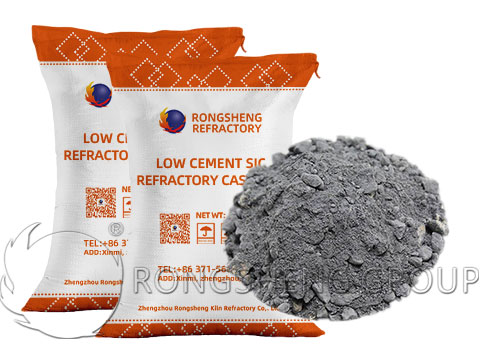
Service Life of Blast Furnace Tap Trough Refractory Materials
After the blast furnace became larger, the usage conditions of the tap trough also changed, and the erosion and wear of the trough wall by molten iron increased. Increasing the generation gap, reducing costs and reducing the work pressure of workers behind the furnace are the main goals of the work behind the furnace. For the main iron trench and different parts, the erosion conditions are different, and the selection of materials should be different to achieve a comprehensive and balanced economic life. For iron ditches, efforts should be made to improve the anti-penetration properties of the material. As far as the construction technology and maintenance process are concerned, some operating methods are also closely related to the service life of the material.
Damage Mechanism of Blast Furnace Iron Trench Refractory Materials
The damage to refractory materials used in blast furnace iron trenches is mainly due to cracks, chemical erosion, penetration, and erosion caused by thermal shock of high-temperature molten iron and slag.
The first is the effect of high-temperature molten iron. Since the blast furnace has a certain pressure, the molten iron with a temperature of up to 1500°C spurting out from the blast furnace directly impacts the working surface of the iron trench. This results in erosion and damage of trench lining materials, especially within the impact zone. The vortex formed here not only intensifies the thermal impact of molten iron and slag on the trench lining, but also intensifies the erosion and erosion of the iron trench lining. The most severe damage is to the trench lining material. Therefore, the damage here determines the service life of the tap hole.
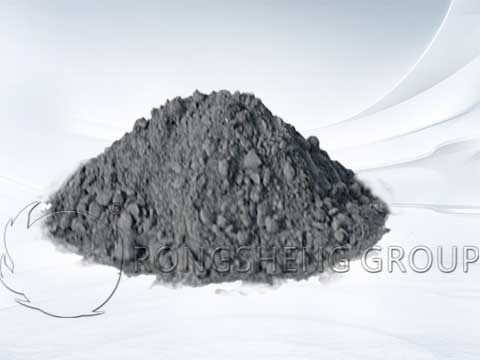
Secondly, in the metallurgical industry, the damage caused by molten slag to refractory materials is the most serious. Since the slag contains relatively complex chemical components, it is easy to react with components in refractory materials to form low melting point substances. Causes damage to the structure of the refractory material and reduces the corrosion resistance, erosion resistance and other properties of the refractory material. When the blast furnace taps iron, in addition to high-temperature molten iron, there is also high-temperature slag entering the tap trough. Slag not only aggravates the erosion of the iron trench lining, but also tends to adhere to the trench wall. It is the main factor that damages the trench lining material. In addition, the damage to the iron trench lining material caused by molten slag also varies depending on the structure of the tap trench. For molten iron tap trenches, the main damage caused by molten slag is erosion and erosion. As for the non-molten iron tap trough, in addition to the above functions, more and more slag adheres to the trench wall and is deposited, which hinders the normal use of the tap trough. Therefore, slagging operations must be carried out in front of the furnace. When slag removal is carried out, the refractory material of the trench wall will be removed together with the bonded slag, which is the greatest damage to the non-molten iron tapping trench lining.
Third, although the blast furnace is a high-temperature equipment that operates continuously, tapping is an intermittent operation, causing the trench lining refractory material to withstand rapid changes in temperature. At this point, the molten iron tap trough also has advantages over the non-molten iron tap trough. Therefore, rapid changes in temperature reduce the thermal shock stability of iron trench lining refractory materials.
In addition to the above damage, the penetration of molten iron into the iron trench lining material is also one of the factors that destroys the material structure. It causes the material to erode and peel off, thereby reducing erosion resistance.
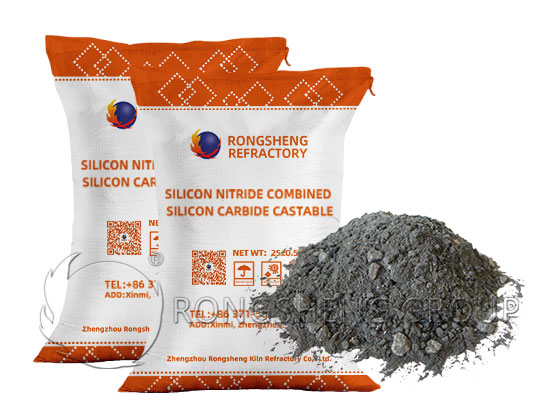
Ferrosilicon Nitride is Used in Al2O3-SiC-C Blast Furnace Iron Trench Castables
In the past, the iron trenches of small and medium-sized blast furnaces were mainly artificial ramming materials mixed with coke, clay clinker and clay, mixed with tar or syrup, and were manufactured by each ironworks. This kind of iron trench lining has a short service life and the iron flow capacity is less than 10,000 tons. In long-term production practice, people have gradually realized that adding silicon carbide and graphite can significantly increase the service life of the tap hole. In terms of refractory aggregates, corundum materials, high-aluminum vanadium clay, magnesia-aluminum spinel materials, etc. have been tested. In terms of binders, various iron trench materials including resin bond, cement bond, and clay bond were tested. After continuous attempts, various types of iron trench materials suitable for large, medium and small blast furnaces have been gradually formed. For high-temperature and high-pressure operations, the tapping volume is large, the flow rate is fast, the temperature is high (1500°C), the tapping times are frequent, the time is long, the amount of slag is large, and the tap trough lining material is used in harsh conditions. To this end, a new generation of iron trench materials based on Al2O3-SiC-C has been developed, which basically meets the production requirements, and the iron throughput ranges from tens of thousands to 100,000 tons. Blast furnace trench castables.
Al2O3-SiC-C castable has good slag erosion resistance and erosion resistance. It has been widely used in the main trench, skimmer and branch trench of blast furnace tap trench. However, due to the development of smelting technology, the continuous improvement of blast furnace utilization coefficient and the requirement of longevity of blast furnace, it is urgent to further improve the service life of Al2O3-SiC-C iron trench castables. However, the current Al2O3-SiC-C iron trench castables are prone to falling off due to periodic chemical erosion of slag and molten iron, thermal shock and erosion of slag and iron. At the same time, the oxidation of silicon carbide and carbonaceous materials in the castables at high temperatures will also cause structural damage to the materials, which will lead to the damage of the castables.
Ferrosilicon Nitride Al2O3-SiC-C Iron Trench Castable
In recent years, research on the use of ferrous silicon nitride in Al2O3-SiC-C iron trench castables has been increasing. Si3N4 in ferrosilicon nitride has the advantage of not being completely wetted with slag and iron, which can improve the corrosion resistance of iron trench castables. The oxidation product of Si3N4 will form a SiO2 protective film on the surface of the sample, hindering further oxidation of the material and enhancing its anti-oxidation performance. The metallic phase Fe has the effect of assisting sintering and can improve the mechanical properties of the castable. It has better antioxidant properties than pure Si3N4. At the same time, the N2 generated by the oxidation of Si3N4 in ferrosilicon nitride at high temperatures and the CO generated by the oxidation of carbon materials will block the internal pores of the material, thus effectively preventing further oxidation.