As competition in the steel industry intensifies, steel companies are pursuing extreme energy efficiency to reduce production costs while developing new products to increase profits. Molten iron or steel will drop in temperature during transportation, and the materials and thermal insulation of ladles, torpedo tanks, ladles, and tundishes are closely related to the temperature drop.
At present, most manufacturers use the method of sticking insulation boards along the inner surface of the steel shell for the insulation of ladles and tundishes. However, insulation boards or nano insulation boards have problems of powdering and shrinkage during use, and thermal conductivity increases accordingly, and the insulation effect becomes worse. Some manufacturers use lightweight insulation bricks as insulation layers, but because of their low density and many pores, there are safety hazards when the working lining is damaged and the permanent layer cracks. Moreover, the thickness of lightweight insulation bricks will not be too thick due to the limitation of inclusion. Although there are studies on semi-lightweight castables containing porous spherical mullite or corundum, laboratory analysis results show that the thermal conductivity of semi-lightweight castables at around 1000°C is higher than that at room temperature. The refractory materials used in the water-cooled beams of the rolling mill heating furnace of Nippon Steel Corporation have developed from refractory bricks in the 1970s to plastics, ceramic fibers and thermal insulation castables, and then gradually developed into calcium hexaaluminate castables and prefabricated blocks, which are now called the fourth generation of thermal insulation materials. The main reason is that calcium hexaaluminate (CA₆) thermal insulation refractory materials have micron-level pores, and their thermal conductivity is kept at a low level from room temperature to 1500℃, and they have excellent high-temperature volume stability, thermal shock resistance, slag resistance, etc.
According to the characteristics of a 200t ladle in a certain factory, thermal insulation panels are used to assist calcium hexaaluminate castables as permanent layer materials. The effects of the permanent layer materials and structural changes of the ladle on reducing the temperature drop of molten steel are analyzed, and the economic and use effects of its application are analyzed and discussed.
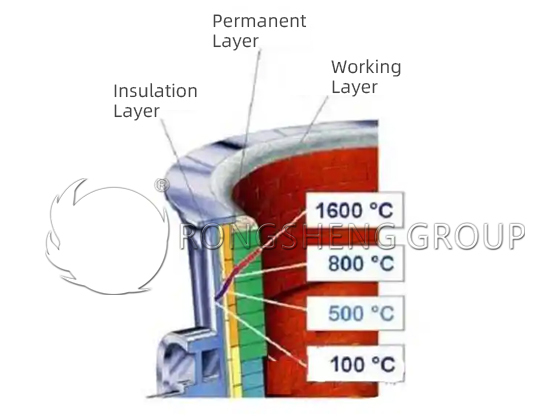
Application of Calcium Hexaaluminate Castable in Permanent Layer of Ladle
After the capacity of 200t ladle of a steel plant was expanded, its permanent layer used high-aluminum castable, which was thinned from 120mm to 90mm. The working layer of the ladle wall uses corundum prefabricated bricks, and the thickness of the ladle wall is thinned from 200mm to 170mm, and the thickness of the slag line magnesium carbon brick is thinned from 220mm to 190mm. After the expansion, the heat dissipation of the ladle increases, the steel shell is deformed, and the temperature drop of the molten steel increases. In order to improve the insulation effect of the ladle, the thickness of the permanent layer remains unchanged, and the rest does not change. Only the material and structure of the permanent layer are changed to reduce its thermal conductivity. The permanent layer is insulated by an insulation board close to the steel shell, and calcium hexaaluminate castable is used inside. The thermal conductivity of the insulation board is ≤0.2W·m⁻¹·K⁻¹, there is no obvious crack after burning, the strength is high, and the maximum use temperature is 1200℃. According to the matching of the thickness of the insulation board of 10mm and the thickness of the castable of 80mm, the thermal simulation calculation is carried out.
The simulation results show that the temperature drop of the molten steel of a single ladle using 80mm thick calcium hexaaluminate castable + 10mm thick insulation board as the permanent layer is 45℃. The temperature drop of the molten steel of a single ladle using 80mm thick high-aluminum castable + 10mm thick insulation board as the permanent layer is 49℃. The temperature drop of the molten steel of a single ladle using only 90mm thick high-aluminum castable and no insulation board as the permanent layer is 86℃.
Therefore, using calcium hexaaluminate castable + insulation board as the permanent layer reduces the temperature drop of the molten steel by 4℃ compared with using high-aluminum castable + insulation board, and reduces the temperature drop of the molten steel by 41℃ compared with using only high-aluminum castable.
After the insulation board is pasted on the inner wall of the ladle shell, the bottom permanent layer is poured first, then the inner formwork is installed, and then the straight section of the hexaaluminate calcium castable is poured. The inner wall of the permanent layer after demoulding is smooth, crack-free, and has good integrity. After using a working layer overhaul cycle (170 furnaces), the inner wall of the permanent layer after overhaul was checked. Except for a small number of discontinuous cracks, there was no peeling damage and it can continue to be used. After the permanent layer uses low thermal conductivity hexaaluminate calcium castable, the shell temperature of the ladle for the 1st to 3rd heats is 199℃, and the slag line temperature is 251℃. The shell temperature of the ladle for the 6th heat is 224℃, and the slag line temperature is 262℃. Compared with the original high-aluminum castable permanent lining, the average temperature of the stabilized ladle shell is reduced by 30 to 50℃. The data of tracking the ladle with permanent layer using calcium hexaaluminate castable and high alumina castable shows that the temperature of the ladle with low thermal conductivity calcium hexaaluminate castable in the permanent layer drops by 0.46℃·min⁻¹ during vacuum treatment. The temperature of the ladle with high alumina castable drops by 0.97℃·min⁻¹ during vacuum treatment, and the insulation effect is significantly improved.
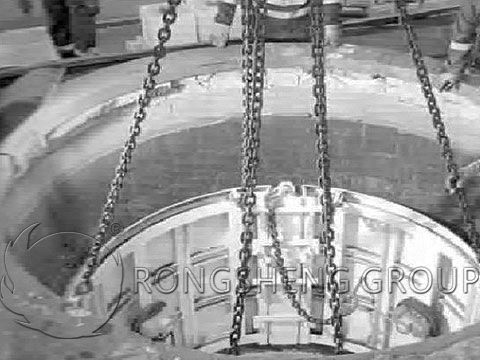
Economic Analysis of the Application of Calcium Hexaaluminate Castables in Permanent Layers
Due to the fierce competition among steel companies, they need to reduce production costs and develop low-carbon and zero-carbon products, so the ladle is under pressure to add scrap steel and expand capacity. However, adding more scrap steel will cause the temperature of the molten steel to drop, and the scrap steel needs to be supplemented or preheated. From the perspective of the enterprise, reducing the temperature drop of the molten steel can add more scrap steel, reduce supplementary heat, and reduce costs. Through the LF process, the electrode heats the molten steel. It is estimated that the power consumption per ton of steel is 0.4kWh for 1℃ increase in temperature, and the cost of 1℃ increase in temperature per ton of steel is about 0.3 yuan. In comparison, reducing the temperature drop of the molten steel by 1℃ will reduce the cost of 1 ton of steel by 0.3 yuan. Taking a 200t ladle as an example, according to the existing permanent layer overhaul furnace service, the cost of a ton of steel using insulation board + calcium hexaaluminate castable is about 0.49 yuan, and the cost of a ton of steel using high-aluminum castable is about 0.25 yuan, so the cost of a ton of steel is increased by 0.24 yuan. For steel mills, it is a favorable choice to use new permanent layer materials (insulation board + calcium hexaaluminate castable) to reduce the temperature drop of molten steel. For example, according to calculations, the temperature drop of molten steel can be reduced by 4°C, which reduces the cost of ton steel by 1.2 yuan. After deducting the cost of ton steel of new materials of 0.49 yuan, it is still 0.46 yuan less than the cost of ton steel of 0.25 yuan using high-aluminum castables, which is very beneficial to steel mills. However, for refractory suppliers, if there is no price compensation, they are not actively using new permanent layer materials.
The volume density of the calcium hexaaluminate castable in this test is 2.82g·cm⁻³. If moderately lightweight aggregates are used to reduce the volume density to 2.0~2.5g·cm⁻³, the cost will be reduced by about 11%~29%. If the density is moderately reduced, the thermal conductivity of the castable will also decrease, and the safety as a permanent layer will also increase. As for the insulation layer, the price will be lower if aggregates with lower bulk density (such as 0.8-1.5g·cm⁻³) are used as spray coatings. Under this condition, nano insulation boards or insulation boards can be eliminated. Through the use of calcium hexaaluminate materials and changes in structure, the cost per ton of steel with insulation layer refractory materials is expected to be reduced to 0.32-0.39 yuan, which is close to the cost of 0.25 yuan per ton of steel using high-aluminum castables as permanent layers. Coupled with the benefit of reducing the temperature drop of molten steel, steel mills and refractory suppliers can achieve a win-win situation. Therefore, calcium hexaaluminate materials have good development potential and application prospects.
Advantages of Calcium Hexaaluminate Castables in Permanent Layers
(1) The thermal conductivity of calcium hexaaluminate castables for permanent layers is about 0.631W·m⁻¹·K⁻¹ at 500, 800, and 1000℃, and the influence of temperature changes is small. The thermal conductivity of high-aluminum castables increases with increasing temperature, and the thermal conductivity at 1000℃ is 1.028W·m⁻¹·K⁻¹. Calcium hexaaluminate castables have better thermal insulation effect than high-aluminum castables at high temperatures.
(2) After the permanent layer of a 200t ladle is made of low-thermal-conductivity calcium hexaaluminate castable + thermal insulation board, the temperature of the ladle wall and slag line is reduced by an average of 30 to 50℃ compared with the original permanent lining of high-aluminum castables.
(3) It is expected that the volume density of calcium hexaaluminate castables can be reduced to 2.0-2.5 g·cm⁻³ by using moderately lightweight aggregates, and the cost will be reduced by 11%-29%. The reduced density can also reduce thermal conductivity. The moderate lightweighting of aggregates can reduce the amount of materials used, and combined with structural changes, it is expected that the cost of calcium hexaaluminate insulation materials can be reduced by 20%-35%. At the same time, the temperature drop of molten steel is reduced, the benefits are increased, and the synergistic effect can significantly reduce the production cost of steel mills.