Due to the structure and working characteristics of the rotary kiln, as well as the diversity and complexity of the materials it handles, the requirements for the temperature of the outer wall of the rotary kiln are also different. From the perspective of environmental protection and energy saving, reducing the temperature of the outer wall of the rotary kiln as much as possible, doing a good job in the insulation layer of the rotary kiln, and the configuration of the refractory lining material of the rotary kiln are all the enterprises that operate the rotary kiln expect. Rongsheng monolithic refractory manufacturer has rich experience in the production, sales, and application of monolithic refractory materials. We have served various types of rotary kilns, which can help you solve the problem of rotary kiln insulation lining. Get pricing information for free.
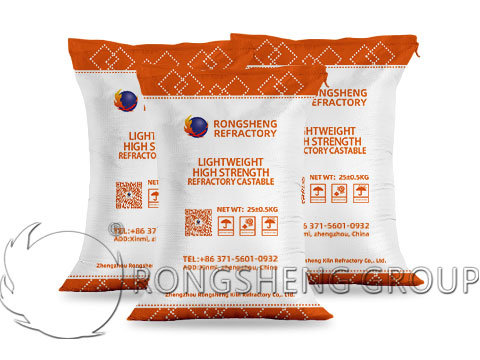
There are also various designs for the thermal insulation lining of the rotary kiln, and the types of refractory materials used are also various. According to the specific needs of customers, we can provide customers with insulating castables, lightweight castables, lightweight plastics, dense refractory plastics, heavy wear-resistant castables, phosphate-bonded composite insulation bricks, ceramic fiber products, etc.
Working Layer and Thermal Insulation Layer of the Rotary Kiln Lining
When the rotary kiln lining refractory material is selected, the next step is to evaluate the heat loss of the rotary kiln body.
When we realize that the working temperature in the rotary kiln is high, and the material has serious erosion and wear on the inner lining, then the inner lining design must consider the double-layer inner lining, and the two inner linings are respectively called the working layer and the thermal insulation layer.
The working layer is made of heavy refractory materials to meet the resistance to high-temperature flames and material erosion and wear; the heat insulation layer is made of light refractory materials to improve the thermal insulation performance of the inner lining and reduce the heat loss of the rotary kiln body.
The inner lining of the rotary kiln has a thermal insulation layer, which can effectively reduce the heat loss of the rotary kiln and also help protect the rotary kiln shell and other shell components.
Generally speaking, the rotary kiln lining with a thermal insulation layer is often used for rotary kilns with high operating temperatures. The refractories of the inner lining of the thermal insulation layer and the inner lining of the working layer have similar chemical compositions, and the difference between Rongsheng refractory materials lies in their respective strength and thermal conductivity. The refractory material lining the thermal insulation layer has a low density and low strength, but its thermal resistance is relatively large, which can effectively reduce the heat loss of the rotary kiln body.
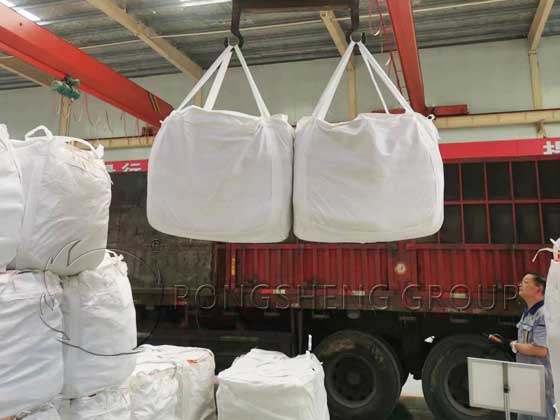
What Refractory Castables are Used for Each Part of the Cement Rotary Kiln?
Refractory castables are used as the main insulation material for the new dry-process rotary kiln. If it is properly configured, it can protect the normal operation of production equipment at high temperatures and effectively reduce system energy consumption.
Cement Rotary Kiln Refractory Castable
- Kiln mouth with refractory castables. At the kiln mouth in front of the rotary kiln, the clinker outlet temperature is around 1400°C, and the temperature of the secondary air entering the kiln changes frequently due to kiln conditions. With the expansion of the scale of the cement plant, the amount of clinker at the kiln mouth is also increasing, and the thermal stress and mechanical stress on the refractory castable at the kiln mouth increase accordingly. For this reason, the kiln mouth refractory castable should have sufficient refractoriness, mechanical strength, thermal shock stability, and alkali resistance under high-temperature environments. It is recommended to use high-performance kiln mouth special refractory castable or improved kiln mouth special refractory castable. The product has excellent anti-stripping performance, high temperature and alkali resistance, and cement clinker erosion resistance.
- Refractory castables for burners. The working environment of the burner is about 1400°C, the flame temperature is about 2000°C, and it works in an alkaline atmosphere for a long time. Compared with the front kiln mouth, the temperature changes more frequently and the temperature difference is larger. Therefore, the requirements for its thermal shock resistance are higher. The front end of the burner is always scoured by the high-temperature airflow entrained with clinker dust, especially the lower part is more severely scoured. Therefore, burner refractory castables need sufficient wear resistance. It is recommended to use special castables for burners or special refractory castables for improved burners. The product has excellent spalling resistance and thermal shock stability.
- Refractory castables for kiln hood and grate cooler. For some large rotary kilns, the heat load on the lower part of the kiln hood is relatively high. If the general high-alumina refractory castable is not well controlled for curing and temperature rise, it is prone to bursting and falling off. The top of the kiln hood is close to the tertiary air duct, and the erosion of the dusty airflow is relatively serious, and the construction of the top castable is relatively difficult, and the requirements for the fluidity and early strength of the material are relatively high. The working temperature at the top of the front end of the grate cooler is high, and the temperature changes greatly. The low walls on both sides of the front end have been worn by the high-temperature clinker coming down through the kiln mouth for a long time, and they are also damaged by certain mechanical stress and thermal stress. It is recommended that these two parts use high-strength wear-resistant castables with good high-temperature performance, strong thermal shock resistance, and wear resistance.
- Refractory castables for tertiary air pipe elbows and air valves. This part has a large change in heat and cold and is washed by high-temperature clinker particles. The castable is prone to loosening and peeling, and it is the most prone to wear and tear during the operation of the cement plant. It is recommended to use wear-resistant refractory castables.
- Refractory castables for C4 and C5 cones and their discharge pipes, calciner cones, and smoke chambers. These areas are prone to crusting and are difficult to remove. Cleaning needs to be done manually with iron tools, which will inevitably cause mechanical damage to the refractory castable. Once severe skinning occurs, the kiln needs to be stopped for treatment. It is recommended to use high-strength anti-skinning silicon carbide castables.
- Refractory castables are used for other parts of the cement rotary kiln. It is recommended to use high-strength alkali-resistant castables for C1~C3, high-temperature high-strength alkali-resistant castables for C4 and C5 (except for the cone), and high-strength wear-resistant castables for the decomposition furnace.
Rongsheng Insulation Castable Manufacturer
The application and development of refractory and insulating castable refractory should conform to the concept of environmental protection and circular economy. Reasonable selection of thermal insulation castables can prolong the service life of the rotary kiln castable lining, effectively protect equipment, reduce system heat loss, reduce system crust blockage, reduce kiln shutdown times and maintenance time, and improve system operation rate. To achieve the purpose of stable production, high production, and low energy consumption of the kiln system. For a case study on the configuration of thermal insulation and refractory materials for the rotary kiln project, please contact us. We will provide you with the most suitable thermal insulation refractory solutions for your production needs according to your working conditions.