Low cement silicon carbide refractory castable is a special refractory material. Made of low cement ratio, silicon carbide aggregates and powders, ultrafine powder, CA-70 cement and antioxidants. It is suitable for thermal equipment such as power generation boilers, non-ferrous metallurgical furnaces and incinerators. It has low linear expansion coefficient, high thermal conductivity, high strength and good wear resistance. Low-cement silicon carbide refractory castables can improve the fire resistance and thermal efficiency of the equipment under reasonable proportions and use under appropriate conditions, and the application effect is good.
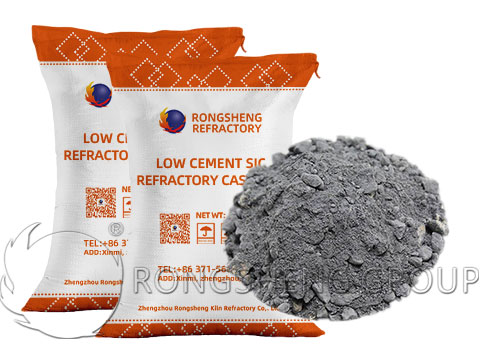
Low Cement Silicon Carbide Refractory Castable
Low cement silicon carbide refractory castable is a special refractory material suitable for thermal equipment such as power generation boilers, non-ferrous metallurgical furnaces and incinerators. This silicon carbide refractory castable has the following characteristics:
- Low coefficient of linear expansion. As the main refractory aggregate and powder, silicon carbide has a low coefficient of linear expansion, which can reduce the possibility of thermal stress.
- High thermal conductivity. Silicon carbide has good thermal conductivity and can effectively conduct heat and improve the thermal efficiency of the equipment.
- High strength. The use of low cement ratio and reasonable binder can improve the strength of the castable and increase its compression and flexural resistance.
- Good wear resistance. Due to the use of silicon carbide with SiC greater than 97% as refractory aggregate, the castable has excellent wear resistance.
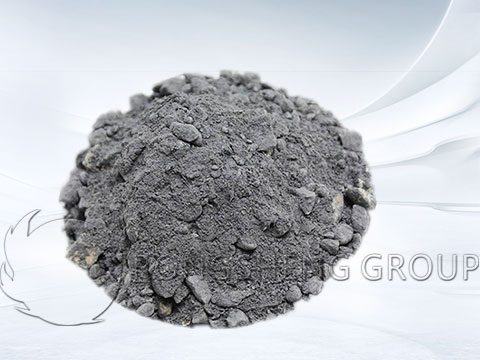
Raw Material Composition of Low Cement Silicon Carbide Refractory Castable
The preparation of low cement silicon carbide refractory castable includes the following ingredients:
- Refractory aggregates and powders mainly use silicon carbide with SiC greater than 97%, which has excellent refractory properties.
- Ultra-fine powder. Adding SiO2 ultrafine powder can improve the density and refractoriness of the castable.
- Binder, using CA-70 cement as the binder, can ensure that the castable has a certain strength and durability.
- Antioxidants. Metallic silicon antioxidants are used to prevent the oxidation of silicon carbide.
The performance test results of the castable at different temperatures are as follows:
- After drying at 110℃, the bulk density is 2.5g/cm³, the compressive strength is 45MPa, and the flexural strength is 9MPa.
- After firing at 1000℃, the linear change is -0.2%, the compressive strength is 107MPa, and the flexural strength is 24MPa.
- After firing at 1450℃, the linear change is +0.3%, the compressive strength is 130MPa, and the flexural strength is 54MPa.
- The thermal conductivity at 400℃ is 12.2W/(m·K).
In summary, low cement silicon carbide refractory castable has a low linear expansion coefficient, high thermal conductivity, high strength and good wear resistance. Through reasonable proportions and the use of appropriate materials, the fire resistance and thermal efficiency of the equipment can be improved. The castable has good application results in thermal equipment such as power generation boilers, non-ferrous metallurgical furnaces, and incinerators.
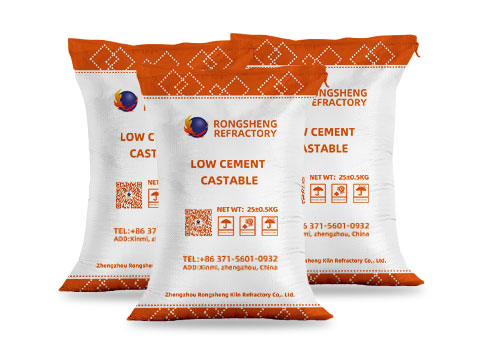
Low Cement Mullite Corundum Castable
Low-cement mullite-corundum refractory castables use sintered or electro-fused mullite, brown corundum, alumina-based corundum and white corundum as refractory bone powder. Sometimes special-grade alumina clinker powder is also used, and ultra-fine powder is mixed with α-Al2O3 and silica fume. It is formulated with aluminate cement as binder and additional dispersant. This material is used for steel rolling heating furnace lining, water cooling pipe wrapping and burner bricks. The use effect is good on thermal equipment such as tundish slag weir, medium and small blast furnace tap trough and electric furnace cover.
Does Low Cement Castable Need to Add Steel Fiber when Used in Settling Chamber?
When low-cement castables are used in settling chambers, steel fibers are usually not required. When the design of the settling chamber is unreasonable, the discharge opening of the cone section is too small and the smoke dust needs to be beaten. At this time, steel fibers can be added to the low cement castable to enhance wear resistance and extend the service life. Under special circumstances, the settling chamber can be lined with clay bricks or high-aluminum castables with high-voltage electrical porcelain added.
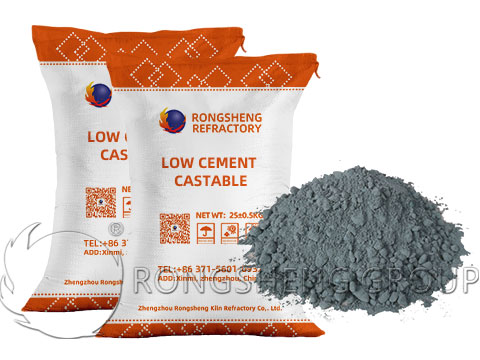
If low-cement castables are used in settling chambers, there is generally no need to add steel fibers.
If the lower opening of the cone section of the settling chamber is too small and needs to be beaten during use, just add steel fibers to the low-cement castable used in the cone section to increase traction, wear resistance, and erosion resistance. However, if the discharge port of the settling chamber is reasonable, and the size of the settling chamber and the rotary kiln are also reasonable, there is no need to add steel fiber to the castable.
The temperature of the settling chamber is not high, and it mainly plays the role of dust removal. The dust has fallen to the bottom before the flue gas flows out of the settling chamber, and is collected by the ash hopper at the bottom of the settling chamber. The unsettled dust is brought out with the flue gas. General low-cement castables can be used.
Generally, it is common to use high-aluminum castables and low-cement castables. However, clay bricks are also used as linings for settling chambers. There is also the use of high-aluminum castables with a certain proportion of high-voltage electrical porcelain added to the castables to create a glazed surface to facilitate the fall of smoke and dust.
Adding steel fibers to low-cement castables is rarely used in settling chambers. In recent years, the settling chambers of some white ash rotary kilns and zinc volatilization kilns are often lined with clay bricks. However, the size design of some settling chambers is not reasonable. If the settling chamber is too small, and the cone section discharge opening is also too small, there will be a situation of beating during the production process to make the smoke and dust sink. This will speed up the service life of the cone section lined with clay bricks or low-cement castables.
Therefore, under special circumstances, a reasonable proportion of steel fibers is added to the low-cement castable to increase the wear resistance of the cone section and extend its service life.