Attack of aluminosilicate refractories by molten aluminum. For example, in aluminum melting furnaces and holding furnaces, this usually results in the formation of aluminum oxide deposits on the refractory. The degree of attack is increased in the presence of alkalis and in reducing atmospheres. This is related to the conversion of alumina bricks into sodium aluminate in a reducing atmosphere. The formation of sodium aluminate promotes the formation of aluminum nitride. In melting furnaces and holding furnaces, the alkali may come from the metal charge.
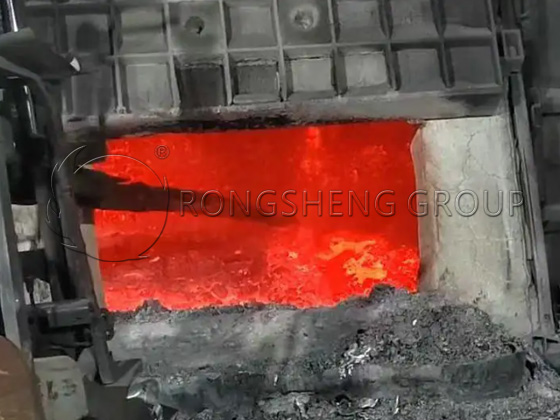
Erosion on 70 Refractory Castables in Aluminum Melting Furnace
In aluminum melting furnaces and holding furnaces, the contact of aluminosilicate refractories with liquid aluminum usually results in the formation of bonded interfacial deposits containing mainly aluminum oxide. Most of this aluminum oxide is the result of the reaction of aluminum with oxides in the refractory, especially with silicon dioxide. The reaction formula is as follows:
4AL+3SiO2→2AL2O3+3Si (1)
The kinetics of the reaction decreases rapidly after the deposit appears. It is concluded that this deposit becomes a barrier that prevents aluminum from penetrating into the refractory. The kinetics of this deposit are increased in a reducing atmosphere and in the presence of alkali. There are two sources of alkaline sodium oxides, in the aluminum ingots produced by the electrolytic cell or in the refractory. In the latter case, the active presence of Na2O cannot be determined. On the other hand, the relevant aspects of the reducing atmosphere have not yet been explained.
The main experiment this time was to determine the reaction of the aluminum silicate refractory to aluminum corrosion caused by alkali and reducing atmosphere, and to determine the reaction of high-aluminum castables (70% Al2O3) with aluminum fluoride (ALF3) as an infiltrant to such corrosion. The possible effects caused by the presence of alkali in the refractory, this product is a representative of amorphous refractory with non-wetting additives. It is used in industry as aluminum insulation furnace and aluminum smelting furnace lining.
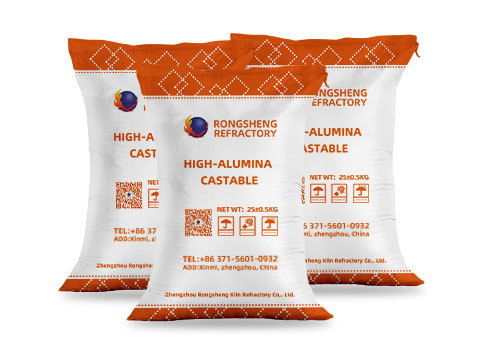
According to the operating temperature of the aluminum insulation furnace and aluminum smelting furnace, the test temperature is determined, and the temperature at the contact with the metal reaches 850℃, and the temperature at the flame radiation site reaches 1200℃~1500℃. The corrosion experiments on industrial high-alumina refractory castables with aluminum fluoride (ALF3) as a non-wetting agent have shown that the corrosion caused by aluminum and the role of basic oxides contained in the refractory material have been speculated.
It appears that, especially in the presence of a reducing atmosphere, beta alumina is the active phase in the refractory material in contact with liquid aluminum. From a thermodynamic point of view, the action of beta alumina on liquid aluminum leads to the formation of metallic sodium. The reaction equation is as follows:
6NaAL11O17+2AL→6Na+34AL2O3 (2)
When the oxygen partial pressure is higher than 10-19atm, the metallic sodium produced in the aluminum solution (aNa~0.1) will be oxidized. The reaction is as follows:
2Na+1/2O2→Na2O (3)
When the oxygen partial pressure is lower than 10-19atm, the presence of Na2O must be related to the action of refractory oxides (especially in silica) on metallic sodium. The reaction equation is as follows:
4Na+SiO2→2Na2O+Si (4)
On the other hand, in the presence of ALF3, metallic sodium may also be produced. The reaction formula is as follows:
6NaAL11O17+2ALF3→6NaF+34AL2O3 (5)
3NaF+AL→3Na+ALF3 (6)
Through analysis, when the liquid electrolyte with a temperature higher than 888℃ exists, reaction equations (5) and (6) can produce metallic sodium, which is conducive to the mutual exchange between the reactants. Under such conditions, a higher Na2O generation kinetics can be expected. Therefore, if the latter contains ALF3 as a wetting agent, aluminum will corrode the refractory material faster. The interface deposit mainly contains corundum (a-AL2O3) and also contains aluminum (AL) and aluminum nitride (ALN). It is believed that the aluminum nitride present in the deposit may participate in this corrosion process. This participation of aluminum nitride is consistent with the analysis of the reaction products obtained between aluminum and sodium carbonate in air and nitrogen. It was identified that at 900℃, the main reaction product obtained was sodium aluminate (NaALO2), which exists in the form of hydrate (NaALO2·3H2O). The specific gravity of sodium aluminate is 2.69g/cm³, while that of aluminum oxide is 3.96g/cm³. Therefore, the protective aluminum deposit should be accompanied by an increase in volume when it is converted into sodium aluminate. The increase in volume is conducive to the formation of cracks, which is conducive to the penetration of aluminum and thus the refractory is susceptible to corrosion.
Application of Cr2O3-Al2O3 Refractory Castables in Melting Furnaces
In principle, although melting furnaces can be lined with Cr2O3-Al2O3 bricks, they can also be lined with Cr2O3-Al2O3 refractory castables. However, for furnaces with complex structures, Cr2O3-Al2O3 refractory castables are often used for lining when considering cost and construction (convenience). Especially for thermal decomposition gasification melting furnaces, since the furnace walls are mostly boiler water pipes, it is very difficult to use refractory bricks for lining, but it is very convenient to use Cr2O3-Al2O3 refractory castables for lining.
When the melting furnace is lined with corundum refractory castables mixed with Cr2O3-Al2O3 powder and Al2O3 powder, it is believed that the Cr2O3-Al2O3 refractory castable with a high Cr2O3 content in the matrix material will also have high durability.
In order to confirm this, the corrosion resistance of refractory castables was compared and studied. The corrosion test was conducted in a rotary corrosion test furnace (1750℃). The results confirmed that the corrosion resistance of these refractory castables increased with the increase of Cr2O3 content in the matrix. The following conclusions can be drawn from the results of the slag resistance test:
- (1) The fact that the concentration of Cr2O3 near the working surface of the Cr2O3-Al2O3 refractory castable decreased confirmed that Cr2O3 had transferred to the slag. The slag contained Cr2O3 and increased its viscosity, which prevented the slag from further penetrating and corroding the Al2O3-Gr2O3 refractory castable.
- (2) At high temperatures, Cr2O3 reacted with Al2O3 to form a solid solution, which improved the high-temperature performance of the material while also improving the corrosion resistance of the material.
- (3) Since the slag containing Cr2O3 has a high viscosity, it also improves the slag resistance of the Al2O3-Cr2O3 refractory castable.