At this stage, most blast furnaces use alumina-silicon carbide-carbon iron trench castables. With the advancement of smelting technology, the amount of iron passed through at one time has increased from the initial tens of thousands of tons to hundreds of thousands of tons, which has also put forward higher requirements for the performance of iron trench materials. The fastest eroding part of the tap trench is the impact zone. In addition to thermal shock, molten iron erosion, and oxidation, the main damage to the iron trench is the high-temperature erosion of molten iron and iron slag.
During the smelting process of molten iron, more silica will be generated. Calcium oxide (the main source of calcium oxide is cement), silica and alumina will react together to form anorthite and anorthite (liquid phase at the operating temperature). Or low melting phase such as calcium aluminate. These low melting phases greatly reduce the high-temperature performance of the iron trench material. Seriously affects the corrosion resistance of the product, thereby affecting its service life. When the low-melting phase is generated, the alumina powder used as the matrix is also consumed. After the matrix is consumed and eroded, the aggregate particles that serve as the skeleton will loosen and peel off, causing the product structure to be destroyed.
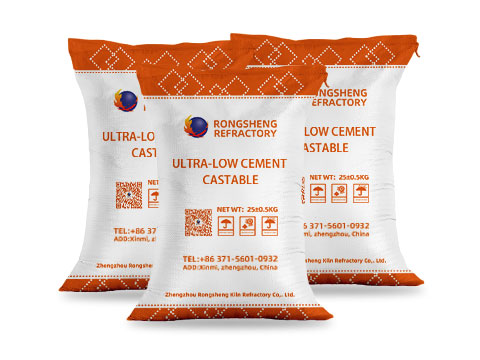
Ultra-Low Cement Bonded Al2O3-SiC-C Iron Trench Castable
At present, most blast furnace trenches use alumina-silicon carbide-carbon castables with high-purity calcium aluminate cement as the binding agent. Calcium oxide is inevitably introduced, thus forming a low-melting phase during high-temperature use. If cement is not used and only ultrafine powders such as alumina powder and silica powder are used, the demoulding strength at room temperature will be low and cannot meet the Stinging requirements. Although there are reports using P-Al2O3 combination (hydraulic alumina) and sol-gel (silicon and aluminum) combination to make iron trench castables. However, there are problems such as fast solidification and difficult control during on-site construction, so it has not been widely used. Cement is still the main binding agent for iron trench materials at this stage. Develop ultra-low cement-bound Al2O3-SiC-C iron trench castables and combine them with ultra-fine powder to minimize the introduction of calcium oxide while ensuring the demoulding strength at room temperature. It not only ensures that it will not be damaged after casting and demoulding, but also improves the high-temperature strength and performance of the material by reducing the low melt content of the castable at high temperatures. It can well resist the erosion of molten iron and slag, thereby extending the service life of the iron trench.
Through experiments, it was found that if the amount of cement added is too small, the demoulding strength at room temperature cannot be guaranteed, and if the amount added is high, the high-temperature performance will deteriorate. Based on the above properties, the optimal addition amount of cement in Al2O3-SiC-C iron trench castable is 0.6%.
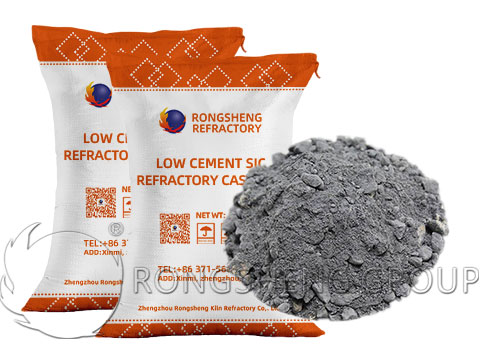
Industrial testing and applications. On the basis of laboratory research results, a plan to add 0.6% cement will be carried out industrial testing in a steel company. The blast furnace capacity is 1080m3, the length from the main trench to the small pit is 14.5m, the slag trench is 11m, and the shared material is 73t. Among them, the main ditch uses 49t. From use to the next set-up, it was used for a total of 84 days, and the iron output was about 165,000 tons, which achieved good results.
in conclusion. Reducing the amount of cement added can improve the high-temperature performance of iron ditch castables. The main reason is to reduce the formation of eutectic anorthite and generate staggered network mullite crystals in the castable to improve high-temperature performance. When the cement addition amount is 0.6%, the overall performance of the castable is better. The iron ditch castable produced on this basis has achieved good industrial test results.
The Castables used in Copper Smelting Trenches Must Have the Following Properties:
According to the working environment and conditions of the copper tapping trench, the castables used for the copper tapping trench must have the following properties.
- (1) It has good thermal shock stability.
- (2) Resistant to corrosion and erosion, and resistant to structural spalling.
- (3) It has suitable expansion properties, anti-permeability, and does not stick to copper liquid.
- (4) It has lower porosity and higher strength.
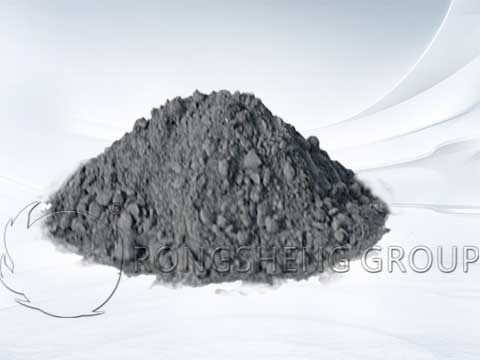
High Alumina-SiC Ultra-Low Cement Castable
In response to usage requirements, refractory material manufacturers have cooperated with enterprises to develop high-aluminum-SiC ultra-low cement castables.
The Adding Amount of Silicon Carbide
Silicon carbide has the advantages of excellent slag resistance, small thermal expansion coefficient, high thermal conductivity, and good wear resistance. Adding an appropriate amount of silicon carbide to high-aluminum ultra-low cement castables can improve its resistance to copper liquid erosion and structural spalling. For the sample with SiC added, as the silicon carbide content in the matrix increases, the compressive strength of the castable first increases and then decreases. The linear change rate after burning increases with the temperature, from shrinkage to expansion, and changes with the SiC content. increases with the increase. This is because as the temperature continues to increase, the oxidation rate of SiC accelerates.
The Adding Amount of Silica Powder
The addition of silica powder can improve the normal temperature strength and post-fired strength at medium and high temperatures of the castable, and reduce the apparent porosity of the material. Microsilica powder can effectively reduce the oxidation rate of SiC at high temperatures. Because silica powder not only forms a siliceous protective film on SiC, but also sinters easily at high temperatures, increasing the thickness of the protective siliceous layer. Therefore, silica powder has a protective effect in inhibiting SiC oxidation when the temperature is above 1000°C. The results show that when the SiC addition amount is optimal and an appropriate amount of silica powder is added, the various properties of the sample are the best and the oxidation rate of SiC is the lowest.
Sintering Agent
The temperature of copper extraction is between 1150 and 1300°C. At this time, the bonding phase of the general castable is at the weak link. That is, a strong ceramic bond is not formed, and erosion often occurs. In order to improve the erosion resistance of the castable and the oxidation resistance of SiC, appropriate sintering agents should be added. To this end, the types and amounts of sintering agents were studied. The results show that when the adding amount of composite sintering agent is 10%, products with excellent performance can be obtained.
Application of High-Aluminum-SiC Ultra-Low Cement Castable in Copper Channel of Copper Converter
Based on the above experimental results, high-aluminum-SiC ultra-low cement castables were used for industrial testing on the copper tapping channel of the blister copper converter. The service life has reached more than three times that of the original magnesia ramming material. The main reason for the damage of high-aluminum-SiC ultra-low cement castables is that the surface layer is oxidized, followed by slag hanging, and peeling off due to thermal shock. The new surface layer oxidizes, slags, and peels off, over and over again, and is finally destroyed. Due to the superior oxidation resistance of this castable, oxidation is limited to the surface layer, so the damage rate is much slower than that of magnesia ramming materials.