Application cases of RS refractory prefabricated parts. Refractory prefabricated parts are most commonly used in small high-temperature kiln equipment. The products required at the construction site are produced in advance by the manufacturer to facilitate customer construction. Used for special-shaped or special-shaped refractory products. Refractory prefabricated parts are widely used in various industrial kilns due to their irreplaceable advantages. Its biggest advantage is that it can be pre-baked and directly hoisted, so the construction period is greatly shortened, and the quality is stable and easy to control.
Application Solutions for Refractory Precast Shapes
Refractory prefabricated parts are an important variety of refractory materials, and their applications account for an increasing proportion. Refractory prefabricated parts are made by dividing the parts of the high-temperature kiln to be constructed into small pieces in advance. And design it into a special shape, and make the mold according to the shape. In the factory, refractory castables and other materials are pre-cast, cured, and baked before being transported to the site for hanging and assembly before use.
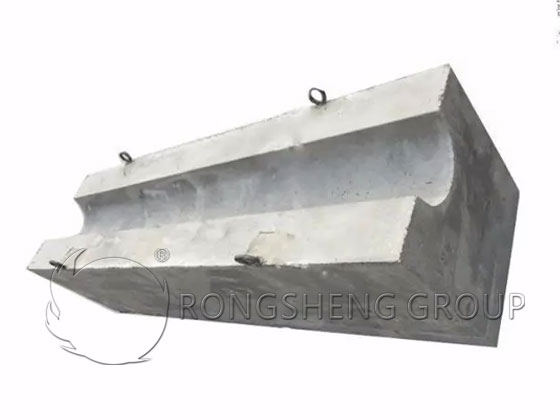
Castable precast shape refractories can be preformed into various shapes at will, with good thermal shock stability, high strength, and good spalling resistance. No joints, good air tightness, less heat loss, and energy saving. It can quickly repair the kiln and improve the furnace operation rate. It can realize direct hoisting and mechanized furnace construction, and the construction efficiency is high. It can solve technical problems in furnace construction for users and can be customized according to user requirements and furnace-type conditions. Consider lining body design and multiple construction options for users.
There are the following solutions for the shaping of unshaped refractory materials in cement kilns. As a result, the unshaped refractory materials used in special parts of the cement kiln are customized and produced. The product has the following characteristics:
- (1) There is no need for on-site pouring construction or formwork pouring, which reduces labor costs and material costs.
- (2) Heat-resistant anchors are not required, eliminating the material and construction costs of anchors.
- (3) The pouring, curing, drying, and baking steps of prefabricated parts have been completed when delivered, saving a lot of construction time.
- (4) It is not restricted by environmental and climatic conditions, which solves the problem that castable materials cannot be constructed on-site under natural conditions during hot summer and severe winter.
- (5) It can be made into various special products with different sizes and shapes. Such as grate cooler low wall, tertiary air duct elbow, lifting gate valve, kiln tail smoke chamber, coal injection pipe, kiln mouth, and other refractory materials.
- (6) Maintenance is easy to replace, has little waste loss, and saves labor and time. Corundum, fused mullite, special grade bauxite aggregate, and special wear-resistant materials are added to the material, and a certain proportion of special additives are added. Vibration forming. Therefore, the product has high strength, wear resistance, corrosion resistance, good mechanical impact resistance, and excellent thermal shock resistance. It has excellent peeling resistance and cracking resistance, long service life, convenient construction, safety, and reliability, and greatly shortens the construction period.
Application Advantages of Refractory Prefabricated Parts
Refractory Preforms refer to components with a certain shape and size made of refractory materials according to specific ratios and process conditions. The main raw materials of refractory precast shapes usually include refractory castables, refractory bricks, refractory fibers, and other special refractory materials. Refractory prefabricated parts are prepared under certain process conditions, which usually include mixing, molding, curing, and drying.
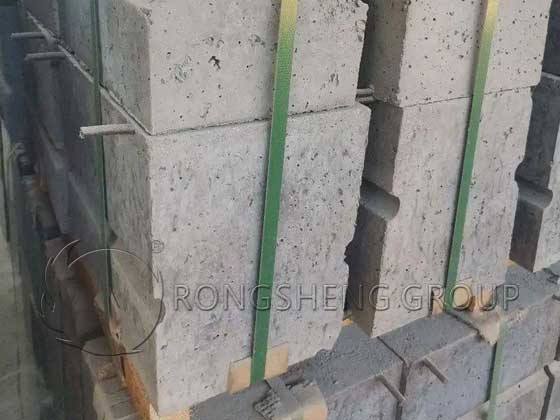
Refractory Precast Shapes have the Following Advantages
- stable quality. During the production process of prefabricated components in the factory, raw materials, proportions, and process conditions are strictly controlled. Therefore, product quality is stable and reliable.
- Save construction time. The use of refractory prefabricated parts can significantly shorten the construction period and improve construction efficiency.
- Reduce on-site labor. Prefabricated components are produced in factories, reducing the workload of construction workers and material handling on-site.
- Good performance. Because the production process of prefabricated components is strictly controlled, their performance is often better than that of refractory materials constructed on-site.
Refractory prefabricated parts are widely used in various industrial furnaces and equipment in petrochemicals, metallurgy, building materials, electric power, and other industries. Such as heating furnaces, smelting furnaces, converters, gas generators, glass kilns, etc. Depending on the actual application environment and needs, refractory prefabricated parts can be customized with different shapes, sizes, and properties. When selecting refractory prefabricated parts, factors such as the working environment, usage conditions, performance of refractory materials, and construction requirements should be considered.
When using refractory prefabricated parts, you need to pay attention to the following points.
- Storage and transportation. During storage and transportation, prefabricated parts should be protected from moisture, heat, and external force damage. It is recommended to store prefabricated parts in a dry, ventilated, and cool warehouse. And pay attention to reasonable stacking to avoid extrusion and deformation.
- Install. When installing refractory prefabricated parts, design requirements, and construction specifications should be strictly followed. For different types of prefabricated parts, corresponding installation methods and connection methods need to be adopted. During the installation process, it should be ensured that the position of the prefabricated parts is accurate and that good connection and sealing properties are maintained.
- Seam treatment. Seams between precast parts should be kept clean and tight to prevent heat loss and the penetration of aggressive gases. Depending on the actual working conditions and precast material, appropriate filling materials can be used for joint treatment. Such as refractory mud, refractory fiber, etc.
- temperature control. During the initial heating and operation of the furnace, the heating rate and temperature should be strictly controlled. To prevent the refractory prefabricated parts from being damaged due to thermal stress caused by excessive heating. At the same time, regularly check the use of prefabricated parts to detect and deal with potential problems in a timely manner.
- Maintenance and overhaul. During use, the refractory prefabricated parts should be inspected and maintained regularly. If damage, cracks, and other problems are found, they should be repaired or replaced in time. For prefabricated parts with a long service life, timely cleaning and maintenance can be carried out to extend their service life.
- With proper selection, installation, and maintenance, refractory prefabricated components can provide efficient and stable performance for industrial furnaces. Save construction time and cost at the same time. In the continuously developing industrial field, the application of refractory prefabricated parts will continue to expand to meet the needs of various working conditions and environments.
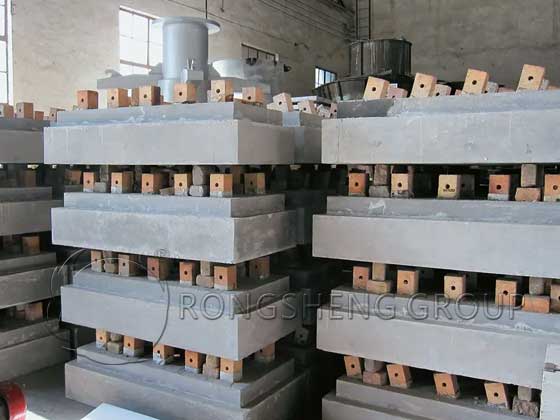
What Should We Do if These Problems Arise with Refractory Castables and Castable Precast Shapes?
Unshaped refractory castables and castable refractory precast shapes have the advantages of convenient and fast construction and low labor intensity. It has been widely used in more and more high-temperature industrial kilns.
However, many corporate users have discovered some abnormal phenomena in refractory castables or prefabricated parts during storage or maintenance. For example, some have chalking, some have white hair, etc. In fact, these are caused by the contact between the high alumina cement hydration products in the refractory castable and the acidic gases in the atmosphere. As the water in the castable evaporates, salt substances continue to migrate and precipitate to the surface, and then slowly intensify the damage process of the refractory castable. Powdering occurs during the storage of prefabricated parts made from cement-containing refractory castables. Some of them have “white hair” growing on the surface, commonly known as white alkali, which causes the surface of the castable to become powdery. In severe cases, the strength of the castable will decrease.
Solution
- Dry the castables as soon as possible after construction to remove moisture. Eliminate the carrier of sodium salt in the pouring body, so that the alkali stays in the construction body and no longer migrates to the surface.
- When the construction conditions do not allow for timely drying, the castable environment must be sealed and the surface covered with plastic film to prevent moisture from carrying alkali from migrating to the surface.
- Use refractory raw materials with low alkali content in the refractory castable to increase the viscosity and rapid hardening of the refractory castable, which can reduce the migration speed of sodium salt. Strengthen quality management and strictly control the amount of water added during construction.
Tips: Leave a message to ask your questions about kiln refractory castables, and we can provide solutions for free.
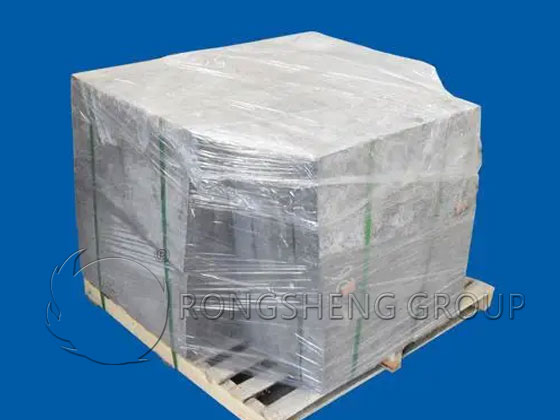
RS Unshaped Refractory Castable Manufacturer
RS unshaped refractory castable manufacturer is a powerful manufacturer of refractory materials production and sales. Our environmentally friendly, fully automatic unshaped refractory material production line customizes unshaped refractory lining materials for high-temperature industrial furnaces. Extend the service life of the kiln lining, save the cost of production energy, and improve economic benefits. Customize refractory precast shapes, wear-resistant refractory castables, insulation castables, refractory plastics, refractory ramming materials, etc. from Rongsheng unshaped refractory material manufacturer. Contact us to get a free customized plan and quote.