Ladle castables are used in steelmaking plants and foundries to receive molten steel and carry outpouring operations in front of open-hearth, electric furnace, or converter. Ladle castable is a kind of granular and powdery material made of refractory materials and a certain amount of binder for a ladle. Ladle castable is an unshaped refractory made of high alumina bauxite, corundum, and magnesia as the main materials, using composite micro powder and adding some additives.
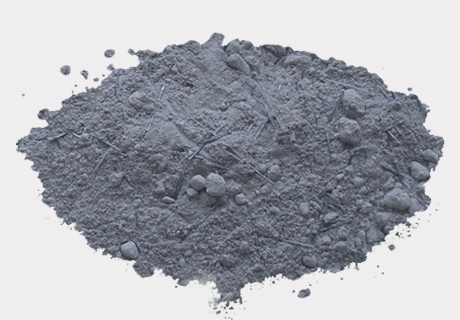
Ladle castables are made of bauxite clinker, corundum, magnesia, magnesium spinel, and ultrafine powder, etc., with different binders and additives. Its characteristics are strong corrosion resistance, good thermal shock resistance, good volume stability, suitable for medium and small ladle use, and long life. Good explosion-proof performance, high-temperature strength, slag corrosion resistance, and strong erosion resistance.
Al2O3-MgO·Al2O3 Refractory Material for Ladle
Al2O3-MgO·Al2O3 refractory materials are selected for the sidewalls and bottom of the ladle. The most common form is Al2O3-MgO·Al2O3 castables. The design of its chemical composition is mainly to use the eutectic phase region of the MgO·Al2O3-Al2O3 sub-system in the Al2O3-MgO binary system, and the area of MgO about 5%. As shown in Figure 5-26, its Al2O3 content is about 90%.
This castable not only has good corrosion resistance (see Figure 5-27), but also has excellent resistance to slag penetration, as shown in Figure 5-28 and Figure 5-29. Figures 5-27 and 5-29 show that the more spinel is added, the more spinel with high MgO content is added, the better the corrosion resistance. The resistance to slag penetration is preferably 90% Al2O3 spinel castable. This type of Al2O3-MgO-Al2O3 castable has a thin slag layer and fewer nodules during use, which protects the inner refractory material. Therefore, its durability is good.
The ω (MgO) in the spinel used in this type of Al2O3-MgO·Al2O3 castables is 10% to 30%, and ω (Al2O3) is 70% to 90%. The choice of spinel particles in castables is usually determined by test results.
The particle size of MgO·Al2O3 (20% content) has an effect on the infiltration of slag into the Al2O3-MgO·Al2O3 system. This shows that only when MgO·Al2O3 is added in the form of fine powder, the thickness of the slag soaked layer is the smallest. It can be seen that only when MgO·Al2O3 is evenly dispersed in the matrix of the Al2O3-MgO·Al2O3 brick can the slag penetrate into the deep part of the brick more effectively. The relationship between the amount of spinel added and the melt loss index and slag penetration thickness can be obtained for castables containing 10% to 30% MgO·Al2O3. The small thickness of the slag impregnated layer is an important basis for guiding the design formula.
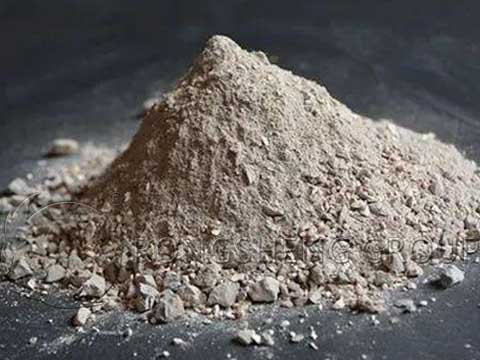
When the mixing amount of spinel is below 20% (mass fraction), fine powder less than 1mm is used. Under this condition, when the amount of spinel added increases, it has the effect of inhibiting slag penetration. When the amount of spinel is greater than 30% (mass fraction), particles larger than 1mm are used. Under these conditions, when the amount of spinel added increases, it has the effect of improving corrosion resistance. The damage of the castable due to structural spalling is much greater than that of Al2O3-C bricks, and the damage rate of the former is 1.3 to 2.5 times that of the latter. Compared with Al2O3-C bricks, the damage rate of castables is reduced by about 30%, showing better results.
At the most severely damaged ladle impact location, the damage rate of Al2O3-C bricks increases with the increase in the ratio of stainless steel to steel. Castable C has the same damage rate and service life as Al2O3-C bricks. When the Al2O3-MgO-Al2O3 series castable containing 20% spinel fine powder is applied to the sidewall of the ladle and the impact part of molten steel, it will not produce cracks and peeling damage during use, and has the characteristics of stability and durability.
The above research results show that the amount of spinel added has an important impact on the performance of aluminum-spinel fired bricks. This kind of fired brick also has the problem that the joints of the bricks are corroded first. To this end, a certain amount of fused magnesia particles can be added to the ingredients to cause residual linear expansion during use. Therefore, the problem of the brick joints being corroded first is prevented, and the service performance of the aluminum-spinel brick can be improved.
In addition, due to the high CaO content of dolomite, it has excellent impurity purification ability. Therefore, the lining of asphalt combined with dolomite bricks is the most economical material for smelting clean steel. The other is to use fired dolomite bricks as lining to produce ultra-low carbon steel.
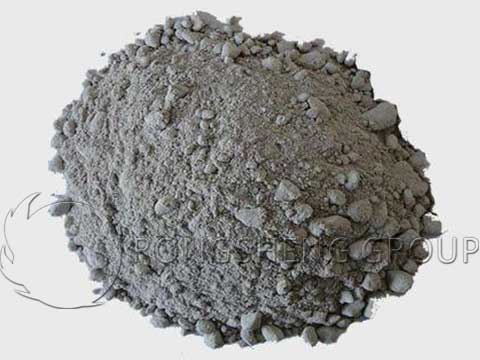
Rongsheng Unshaped Refractory Manufacturer
Rongsheng is an experienced manufacturer of refractory materials. Rongsheng not only sells various refractory brick products to customers all over the world but also provides overall refractory material solutions and refractory materials for various thermal furnace linings. Rongsheng’s advanced fully automatic monolithic refractory production line has an annual output of 80,000 tons. Rongsheng’s best-selling products include various alumina bricks, magnesia bricks, silica bricks, corundum bricks, mullite bricks, thermal insulation bricks, and other refractory brick products. There are also monolithic refractory products such as high-aluminum refractory castables, refractory plastics, refractory ramming materials, and refractory spray coatings. We also provide customers with high-quality refractory bricks and refractory castables for ladle lining. To get the price of Rongsheng refractory materials for free, please contact us. We will provide you with refractory lining materials that best suit your production needs based on your specific furnace conditions.