Lightweight Thermal Insulation acid-resistant refractory castables are usually used for the lining of the chimney wall of the circulating fluidized bed boiler. On the lining of the chimney wall of the circulating fluidized bed boiler, the castable is used not only as an acid-resistant lining, but also as a refractory and heat-insulating layer, and no insulation layer is added.
The light acid-resistant castable is composed of light aggregate, powder, binder, and additives, and the main component of the binder is water glass. The lightweight aggregate structure has a large porosity, a rough surface, and a particle size of about 5mm, and the aggregate and powder have high water absorption and hygroscopicity.
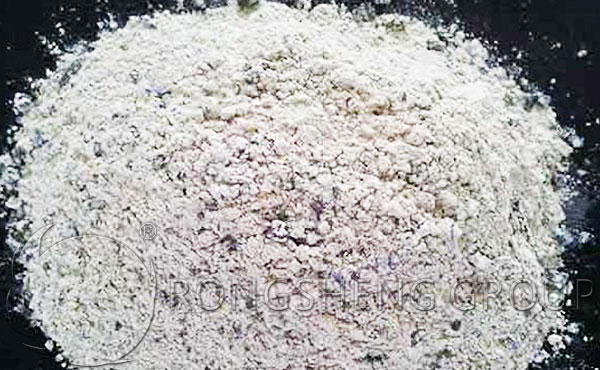
Lightweight acid-resistant castables have the characteristics of low bulk density, fast solidification, high service temperature, increased compressive strength with the increase of temperature and acidity, small thermal conductivity, and a small coefficient of linear expansion. However, lightweight Thermal Insulation acid-resistant castables have relatively high requirements for transportation and storage. This is because the manufacturer has prepared the aggregate and powder into a mixture when leaving the factory, and then packed it in a woven bag. When transported to the site, it needs to be temporarily stored in a warehouse with good drainage measures, rain-proof, moisture-proof, and dry.
Need Lightweight Thermal Insulation Acid-Resistant Castables??? Send Us An Email Now!!!
Features of Lightweight Thermal Insulation Acid-Resistant Castables
Lightweight Thermal Insulation acid-resistant castables are unshaped refractories that can be directly cast into linings as needed, and can also be made into prefabricated bricks.
Lightweight heat-insulating acid-resistant castables have the characteristics of high compressive strength, acid and acid gas corrosion resistance, light volume, and low water absorption. Thermal Insulation acid-resistant refractory castables fully play a role in thermal insulation in tall chimneys, high-temperature flues, and pipe linings. The light acid-resistant castable can ensure the compactness of the masonry when it is used in places with severe acid corrosion. It can also be used in acid-resistant projects such as acid-resistant pools and tanks in petroleum, chemical, non-ferrous metallurgy, and other industries.
Lightweight Thermal Insulation acid-resistant castables are easy to construct, have strong cohesion, and have a long initial setting time and construction operation time. The strength of the castable increases rapidly, the impermeability is strong, and no acid treatment is required. It is convenient to ensure the dense and full masonry ash joints, and can significantly improve the air tightness and integrity of the chimney lining wall and the anti-corrosion ability of the lining.
Lightweight Thermal Insulationacid-resistant castables need to be poured in layers, and the layered vibrating time should be shorter than the vibrating time of the castable. The amount of water added to the castable also needs to be strictly controlled, and the amount of water determines the performance and strength of the castable. Therefore, attention must be paid to the construction of the castable, and the mixed water should be added according to the construction standards of the castable.
Get the High-Temperature Chimney Wall Lining Lightweight Thermal Insulation Acid-Resistant Refractory Castables??? Free Quote Here Now!!!
Matters needing attention in the construction of light acid-resistant castables
In the construction of castables, it is necessary to choose a more suitable construction environment, and a suitable temperature is a key to the construction of refractory materials. How much should the construction temperature of acid-resistant castables be controlled? Let’s find out together.
In the preparation of lightweight thermal insulation and acid-resistant castables, the main raw materials used are aluminate cement and light aggregates. Raw materials such as perlite aggregates are made by adding various additives such as high alumina fine powder and silicon powder. The product has the characteristics of light volume, high compressive strength, alkali resistance, acid gas resistance, heat insulation, heat preservation, and low water absorption. The lightweight Thermal Insulation acid-resistant refractory castable has the characteristics of convenient construction and convenient construction in the preparation process and is an ideal product for the construction of high-temperature acid-resistant components.
After talking about the characteristics of so many lightweight Thermal Insulation acid-resistant refractory castables, according to the structural characteristics of acid-resistant castables, what temperature should the construction temperature be controlled at? In the construction of castables, the construction temperature can be flexibly selected according to seasonal changes. In the summer construction environment, the construction temperature is about 20 to 30 ℃. When the temperature is too high in summer, the setting speed of the acid-resistant castable will be accelerated, but the strength of the castable will be affected. When the castable is prepared, a small amount of retarder can be added to slow down the setting process of the castable. In the winter construction environment, the construction temperature should be between 5°C and 10°C at room temperature, and the construction temperature should not be lower than 0°C. When the temperature is too low, an accelerator needs to be added to accelerate the setting of the castable.
High-Temperature Chimney Wall Thermal Insulation Lining Lightweight Acid-Resistant Refractory Castables??? Get a Free Sample Now!!!
Thermal Insulation Acid Resistant Refractory Castable for High-Temperature Chimney Wall Lining. High-quality lightweight heat-insulating acid-resistant refractory castables, free samples, and quotations, please contact us.