The boiler furnace is a three-dimensional space surrounded by furnace walls for fuel combustion. Its function is to ensure that the fuel is burned as much as possible and to cool the flue gas temperature at the furnace outlet to a temperature that allows the convection heating surface to work safely. Rongsheng Refractory Material Manufacturer can provide high-quality boiler furnace refractory materials – refractory lining maintenance services for high-temperature industrial furnaces. Contact Rongsheng for detailed information.
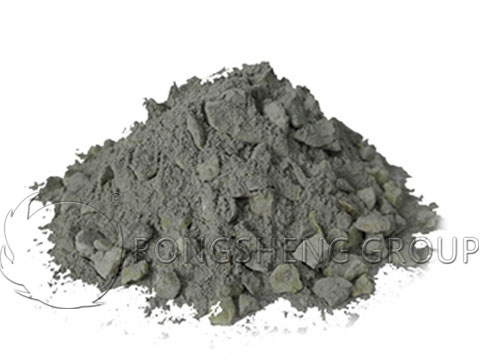
Refractory Castables for Furnace Lining
Common refractory castables for furnace lining include steel fiber, special high aluminum, brown corundum, silicon carbide, mullite, etc. Aggregates and powders made of high-temperature resistant or high-temperature wear-resistant products, with binders, ultrafine powders, and other products added, are mixed and made. They can be cast or made into high-temperature-resistant prefabricated parts and hoisted for construction.
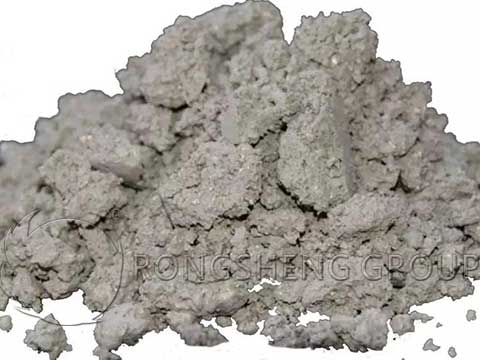
High-Temperature Resistant Plastic Refractory for Furnace Lining
High temperature resistant plastic for furnace High temperature resistant plastic for furnace is basically the same as castable material, but the combination and construction methods are different. It is composed of 80% to 85% high-strength aggregate and fine powder. After adding binder and plasticizer, a small amount of blending agent is added. After sufficient mixing, it is a kind of hard mud paste, which can be made of various high temperature resistant raw materials. It belongs to a more plastic and shape-changing refractory material.
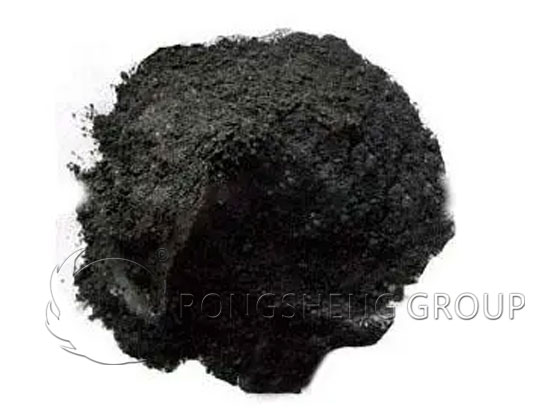
Ramming Material Refractory for Furnace Lining
Compared with other amorphous refractory materials of the same material, ramming material for furnaces is dry or semi-dry and loose. The dense structure is obtained by strong ramming, and the combination will have density only when it is heated to the sintering temperature. Compared with castables and plastics, it has more reliability and corrosion resistance at high temperatures. However, its service life depends to a large extent on the pre-burning before selection or the sintering amount during the first use. If the heating surface is sintered as a whole without cracks and does not separate from the bottom layer, the service life can be improved.
The refractory materials for furnaces should not only look at the product quality, but also the furnace drying is an important link. The furnace should not only be baked, but also the necessary furnace boiling should be implemented. The heating boiler in winter should also be baked before it is put into operation to drive away the moisture in the furnace body and chimney flue. Boil the furnace means to put scientifically proportioned chemicals into the furnace to dissolve and remove the oil, dirt, rust, etc. attached to the inner wall of the heating surface during the manufacturing or transportation of the boiler, so as to ensure the safe operation of the boiler and the quality of steam and hot water.
Causes of Damage to Refractory Castables for Furnaces and Methods of Repairing Castables
Speaking of the current structure of boilers, it is estimated that a large part of the structure is selected refractory castables. Refractory castables not only have high performance and good performance. In many cases, refractory castables can be modified to produce different properties of refractory materials, which is one of the reasons why refractory castables are very popular now.
However, one of the puzzling problems is that refractory castables are used for a long time, or a considerable part of the products are extremely vulnerable to damage during the curing process. When building boilers, the use of aluminate cement refractory castables is mainly caused by the combination of aluminate cement and castables.
-
Surface crushing caused by alkaline impurities
In the material, the presence of soluble alkali increases solubility and accelerates the reaction as an important prerequisite. In cement castables, the increase in cement content and the increase in system alkalinity will lead to larger hydrated minerals, which is conducive to the reaction. Curing environment temperature and humidity are important factors for damage. Generally, the greater the humidity, the easier it is to wet the pores in the casting body. Under humid conditions, dissociation is easier and the reaction is smoother. The density of the green body is also an important factor. When the porosity of the green body is high, water in the air is more likely to diffuse into the green body, so that the damage reaction continuously enters the depth of the green body, resulting in casting. The crushing of the table and the inside will damage the material. In addition, the shape and thickness of the blank also affect the progress of the reaction. In addition, the quantity and quality of construction water will also affect the damage.
-
Surface pulverization caused by carbonation reaction
Surface pulverization caused by carbonation reaction can be divided into two types. One is direct carbonation, where carbon dioxide directly reacts with the hydration products of cement to form a calcium carbonate-calcium aluminate complex. It closes the surface pores and causes surface hardening, thereby inhibiting pulverization. The other is carried out by the catalysis of sodium ions in the presence of soluble alkali metal oxides. This is similar to the mechanism of sodium ion damage, which may lead to the destruction of the castable lining.
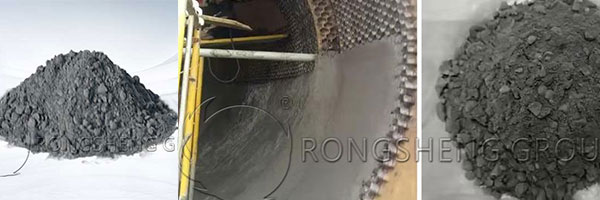
Repair of Furnace Lining Refractory Castables
The damage and repair methods of furnace lining refractory castables are mainly used to solve surface damage.
- Wash high-purity raw materials to reduce the content of soluble alkali metals. When preparing refractory castables, choose high-quality refractory aggregates as much as possible, and choose washed and baked raw materials with low alkali content (such as bauxite and corundum). If the raw materials are not calcined (such as andalusite), choose more cautiously and try to use composite sodium and low concentration mixtures. The dispersion effect and filling effect of micropowder are conducive to improving the density of castables. However, when selecting micropowder, the impurity content of micropowder should be properly controlled to minimize the amount of cement containing high alkali metal impurities.
- Strengthen the control of construction water quality.
- Reduce the contact between the surface of the castable and the air. Surface coatings, coverings, etc. can be used to close the surface pores and minimize the diffusion of CO2 and water vapor into the castable to prevent damage reactions.
- Accelerate hardening, dry the green body as soon as possible, promote the development of green strength, and make the damage reaction lose conditions.
After a period of operation, the damage to the original furnace lining has been restored, and the damage to the furnace lining material has not been aggravated. Therefore, when using castables, we should take correct measures in time to make good transformation of the boiler. Rongsheng amorphous refractory castable manufacturer is a powerful manufacturer and seller of refractory materials. To purchase refractory castable products for furnace lining, please contact Rongsheng for free samples and quotations.