What is the bulk density of the refractory castable? Generally, this technical index will be given before the refractory castable leaves the factory. The unit of castable bulk density is usually g/cm3. The bulk density of the castable can range from 0.8g/cm3 (or even lower) to 3.2g/cm3 (or even higher). Which castable to choose depends on the production conditions of the high-temperature industrial furnace.
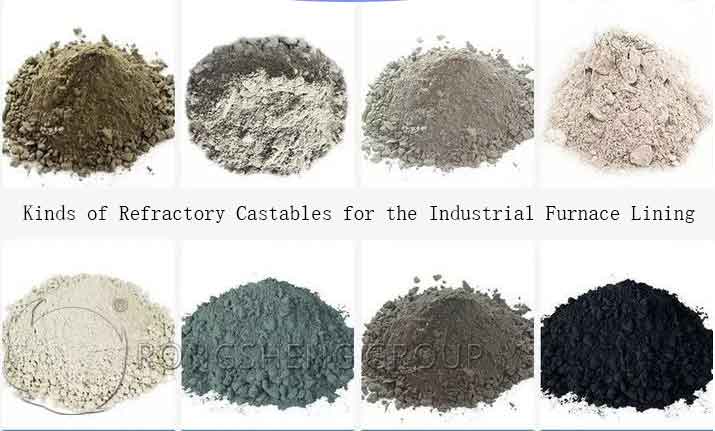
The bulk density of refractory castables refers to the mass per unit volume after adding a specified amount of water or liquid binder to the castables, stirring, pouring, curing, and hardening, and then drying at 110°C. It is one of the commonly used physical and chemical indicators of refractory castables. The difference between the unit volume dosage and bulk density of refractory castables. A test method for testing the dosage per unit volume of refractory castables is introduced. The test results intuitively reveal the difference between the unit volume dosage of refractory castables and their bulk density, and the differences between different types of castables. Taking the hydraulic refractory castable as an example, the reasons for this difference are analyzed.
What is the Proper Bulk Density of Refractory Castable?
The density of the castable affects the wear resistance, strength, service life and thermal insulation, and energy-saving effect. So, what is the appropriate density of the castable? Is the higher the density of the castable, the better? The density of the castable we use has a great influence on its performance, and some people think that the denser the castable, the better, which is wrong. It should be determined according to the occasion you use and the type of castable.
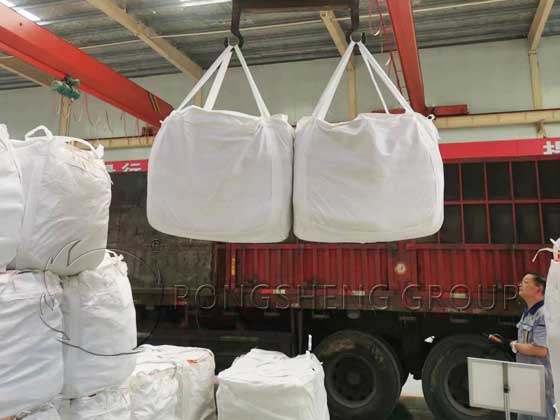
Now refractory castables are used in many industries, and different industries have different standards for the use of castables. The density of the castable is one of the most critical factors. The density of the castable has a great influence on its performance, so the requirements for the density of the castable are different in different situations.
The different industries used have different requirements for the wear resistance of castables. For example, tunnel kilns, such as mechanical equipment, have different requirements for wear resistance. Therefore, the density requirements for refractory castables are also different. In addition, different types of refractory castables also have great differences in construction density.
What is the appropriate density of castable? For parts that need to be exposed to flames and require high wear resistance, it is recommended to use corundum series products or corundum plastics with high density and good wear resistance. For those who require good heat preservation and heat insulation effect and have requirements on weight, light castables with low density and light weight are used.
Bulk Density and Apparent Porosity of Refractory Castables
In addition to the solid body, the prepared refractory castable sample also has many pores of different sizes and shapes, that is, the sample is a porous body. There are three types of pores: open pores that are closed on one side and open to the outside world, closed pores that are closed in the sample and not connected to the outside world, and penetrating pores that penetrate through several sides of the sample. The total porosity, that is, the true porosity, refers to the percentage of the total volume of the pores in the sample to the total volume of the sample; in general, the through pores are combined with the open pores, and the closed pores are less and difficult to measure directly. Therefore, the porosity is expressed by the open porosity, that is, the apparent porosity. Apparent porosity refers to the percentage of the total volume of open pores in the sample to the total volume of the sample.
Bulk density refers to the ratio of the amount of castable to the total volume of the sample after drying, that is, the ratio of the amount of castable to the total volume of the porous body, expressed in Kg/m3 or g/cm3.
Apparent porosity and bulk density are one of the basis for controlling the amount of castable in the construction of refractory castable. The two performance indicators can be measured with the same sample. The followings are the bulk density and apparent porosity of commonly used refractory castables.
- CA-50 cement high alumina castable bulk density 2.3–2.6g/cm3, apparent porosity 17-20%
- CA-50 cement clay castable bulk density 2.2-2.35g/cm3, apparent porosity 18-22%
- Clay combined with high alumina castable bulk density 2.25–2.45g/cm3, apparent porosity 16-21%
- Low cement high aluminum castable bulk density 2.4–2.7g/cm3, apparent porosity 10-16%
- Ultra-low cement high aluminum castable bulk density 2.3–2.6g/cm3, apparent porosity 10-16%
- CA-70 cement corundum castable bulk density 2.7–3.0g/cm3, apparent porosity 12-16%
- Water glass clay castable bulk density 2.10–2.35g/cm3, apparent porosity 15-19%
- High aluminum phosphate castable bulk density 2.3–2.7g/cm3, apparent porosity 17-20%
- Aluminum phosphate high alumina castable bulk density 2.3–2.6g/cm3, apparent porosity 16-20%
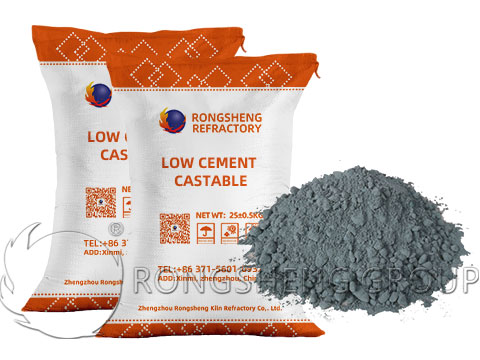
What is the Density of Low Cement Refractory Castables?
Before understanding the density of low cement refractory castables, it is necessary to understand the composition of low cement refractory castables. Low-cement castables use calcium aluminate cement as the binder, and castables with a CaO content of less than 2.5% are collectively referred to as low-cement castables. Different from traditional castables, low-cement castables are used to replace most or all of the high-alumina cement with coagulated ultrafine powder (particle size less than 10 microns) with the same or similar chemical composition as the main material. Optimize particle gradation, fine powder, particle shape, and other factors. At the same time, it is formulated by adding a small amount of dispersant (water-reducing agent) and an appropriate amount of retarder and other compound admixtures.
- The density of clay low cement refractory castable is about 2.26g/cm³.
- The density of high alumina low cement refractory castables is around 2.3~2.6g/cm³.
- The density of corundum low cement refractory castable is about 2.65~2.9g/cm³.
The density of low-cement castables is that if the content of alumina is 51%, its density is 1.3g/m3; if it is 60%, its density is 1.52g. The alumina content is 63%, its density is 1.51g; 65%, its density is 1.78g. The smaller its volume density, the lower its thermal conductivity and absorption, and the better its thermal insulation performance. Its scope of use plays a role in heat preservation and heat insulation in industrial kilns and thermal equipment, and its withstand temperature is 600 °C. It can be divided into low-temperature lightweight low-cement castables that can withstand below 900 °C. Medium-temperature lightweight low-cement castables can withstand temperatures between 900-1200°C. High-temperature lightweight low-cement castables can withstand temperatures above 1200°C.
This product is formulated by adding a small amount of dispersant (water reducer) and a certain amount of slow-acting retarder. Because the cement content of this product is low, the eutectic phase is reduced, thereby improving refractoriness, high-temperature strength, and slag resistance. And when heated, the strength can also increase with the increase of heat treatment temperature. The small amount of cement also allows low-cement castables to achieve the corresponding effect without pouring too much water. The service temperature of low cement castables and ultra-low cement castables is higher than that of ordinary refractory castables of the same material. In the glass kiln tin tank bottom, cement kiln front and rear kiln door cover cooler front and other high-temperature resistant parts, front and rear kiln mouth, coal injection pipe, etc. Heating furnaces, soaking furnaces, and other heat treatment furnaces. The lining of the intermediate frequency induction furnace, the high-temperature wear-resistant lining of the petrochemical catalytic cracking reactor, and the lining of other industrial kilns have been fully applied.
Regarding the appropriate density of castables, Rongsheng monolithic refractory castable manufacturers provide refractory castables with various volume densities(lightweight refractory castables 0.5g/cm3、0.6g/cm3、0.8g/cm3、1.0g/cm3、1.2g/cm3、1.5g/cm3; dense refractory castables 2.0g/cm3、2.2g/cm3、2.3g/cm3、2.4g/cm3、2.5g/cm3、2.6g/cm3、2.7g/cm3、2.8g/cm3, etc. ), which can be selected for high-temperature industrial kilns. Purchase kiln lining refractory bricks and monolithic refractory castables find suitable refractory manufacturers, high-quality construction teams for refractory lining materials, and perfect customer service from Rongsheng manufacturers. Help you solve all-around services from refractory production and construction after-sales. Let your high-temperature kiln run smoothly on the road of high efficiency and long life. Look forward to working with you.