Silicon carbide refractory castable has stable properties and excellent corrosion resistance and wear resistance. It is not corroded by boiling hydrochloric acid, sulfuric acid, or hydrofluoric acid. SiC 75-80% castable. Silicon carbide refractory castable for reducing atmosphere furnace lining. It will not oxidize when used in a reducing atmosphere with a temperature of 1600°C, but oxidation will occur in an oxidizing atmosphere.
The Optimal Operating Temperature of Silicon Carbide Castables in Reducing Atmosphere Furnaces
Silicon carbide castable is used at a temperature of 800-1140℃, rather than 1300-1500℃. Because within the range of 800-1140°C, the oxide film formed by oxidation has a loose structure and cannot play the role of silicon carbide. Above 1140°C, especially between 1300-1500°C, the oxide film formed by oxidation covers the surface of the silicon carbide substrate, preventing oxygen from contacting the silicon carbide. Therefore, the antioxidant capacity is the best within the temperature range of 1300-1500°C. However, when the temperature exceeds 1500°C, the oxidation protective layer will be destroyed. At this time, the silicon carbide castable will be strongly oxidized and the matrix will be decomposed and destroyed.
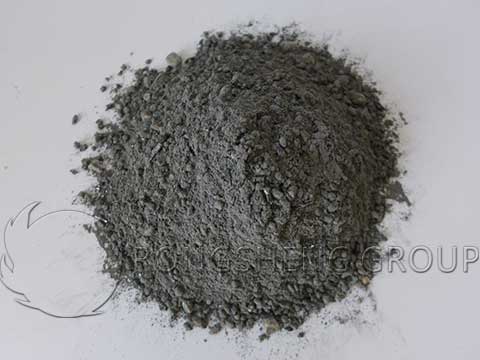
Application Advantages of Silicon Carbide Castables
Silicon carbide castable is a hard material with high hardness. It has good creep resistance, thermal shock resistance, and wear resistance, but has high thermal conductivity. However, silicon carbide castables also have different qualities, that is, different proportions of silicon carbide are added. However, no matter what type of castable it is, metal silicon powder must be added to adjust it to resist oxidative decomposition. Including refractory bricks, they must also be adjusted to prevent oxidation.
In fact, silicon carbide castable is a composite castable, which is made of alumina aggregate and powder, mixed with a certain proportion of silicon carbide and binder. So they are all composite.
Generally used in furnace linings with severe erosion. If the temperature is below 1300°C for the furnace lining, do not use silicon carbide refractory castables. Furnace linings in oxidizing atmosphere are also not suitable for this castable. Silicon carbide refractory castables are best used in reducing atmosphere furnace linings at 1300-1500°C.
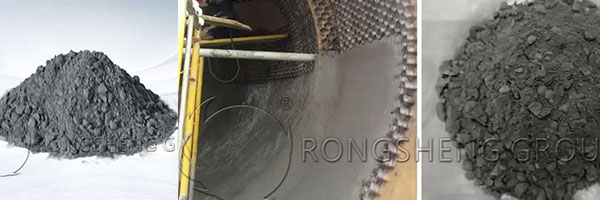
Silicon Carbide and Its Application in Refractory Materials
Silicon carbide can maintain high strength and high wear resistance at high temperatures. After adding a certain proportion of silicon carbide, refractory castables have good chemical stability and will not be corroded by acid and alkali solutions. Silicon carbide has a larger wetting angle with molten metal and slag. Compared with oxide refractory castables, it has good corrosion resistance to various furnace lining solids, liquids and gases.
Wear-resistant
The hardness of silicon carbide is second only to diamond, and it has strong wear resistance. It is an ideal material for wear-resistant pipes, impellers, pump chambers, cyclones, and linings of ore hoppers. Its wear resistance is 5-20 times that of cast iron and rubber, and it is also one of the ideal materials for aviation runways. Using a special process to coat silicon carbide powder on the inner wall of the turbine impeller or cylinder block can improve its wear resistance and extend its service life by 1 to 2 times.
Thermal shock resistance
Due to the high thermal conductivity and small thermal expansion coefficient of silicon carbide, silicon carbide refractory materials have good thermal shock resistance. The thermal shock resistance of silicon carbide products is also closely related to the type and nature of the bonding base material. In actual application, since silicate-bonded silicon carbide products can be observed to expand, crack, and deform after being subjected to thermal shock, the service life of the material can be easily predicted.
High thermal conductivity
Since silicon carbide itself has good thermal conductivity, refractory materials with high silicon carbide content have higher thermal conductivity. Most of their thermal conductivity exceeds 14.4W/(m·K). Used in heat exchangers, saggers, water-cooled walls of coal gasification furnaces, indirectly heated kiln furniture products, etc. During the use of silicon carbide products, the thermal conductivity of the particle surface will gradually become smaller. The properties of the bonding base material have a certain impact on the thermal conductivity of silicon carbide products. The thermal conductivity of silicon oxynitride bonded and silicon nitride bonded silicon carbide is higher, and the thermal conductivity of silicate bonded silicon carbide is smaller.
Anti-oxidation
Silicon carbide has good oxidation resistance. Oxidation is weak below 1300°C. Significant oxidation does not occur until the temperature is above 1300°C. The oxidation generates a SiO2 glass protective film, which can inhibit the oxidation of silicon carbide.
The oxidation resistance of silicon carbide refractory products also varies significantly with the type of binding base material. The lower oxidation resistance of silicon nitride-bonded silicon carbide products can be explained by their microstructural characteristics. Because the base material of silicon nitride combined with silicon carbide products is in the form of interwoven fibers and has high air permeability, it plays a small protective role on silicon carbide particles. In silicate bonded and silicon oxynitride bonded silicon carbide products, the surface of the silicon carbide particles is wrapped by a continuous base material. Therefore, it has strong antioxidant properties. The antioxidant properties of silicate-bonded silicon carbide and silicon oxynitride-bonded silicon carbide show similar properties in the above tests, but the differences between them can be clearly shown in long-term use.
Resistance to slag
SiC is a compound with strong covalent bonds and maintains high bonding strength at high temperatures. Therefore, SiC has good chemical stability and will not be corroded by most acid and alkali solutions. Silicon carbide has a larger wetting angle with molten metal and slag. Compared with oxide refractory materials, it has good corrosion resistance to various solids, liquids and gases. Such as Al2O3-SiC-C castables and products used in iron-making systems, silicon molybdenum bricks and silicon carbide-containing castables used in cement kilns, various acid-base reaction vessels, etc.
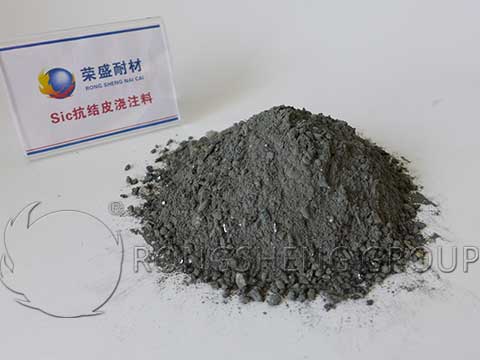
Application of Carbonaceous Castables Containing Silicon Carbide Raw Materials in Blast Furnace Bottom
Blast furnaces are the basis for stable and smooth ironmaking production, and the most important ones are carbon bricks and water cooling systems. Carbon bricks and molten iron are not easily wetted and have strong corrosion resistance. Water cooling is the key to ensuring the longevity of carbon bricks. During the blast furnace bottom masonry process, after the water-cooling pipes are laid, the existing technology mostly uses carbon ramming material to level and fill the carbon brick joints. In order to ensure the water cooling effect, the carbon ramming material is required to have high thermal conductivity, a certain strength, and good construction performance. Since the performance of ramming materials is closely related to the construction process and quality, and there are many human-influenced factors, the thermal conductivity often fails to meet the expected requirements. In recent years, the results of analyzing carbon castables show that the thermal conductivity of castables mainly made of carbon raw materials is relatively low, and some are less than 10W·(m·K)⁻¹. The thermal conductivity of carbonaceous castables containing silicon carbide raw materials is greater than 15W·(m·K)⁻¹. Its construction is more convenient than ramming material, and its operation is simple. It only needs vibration forming and quick smoothing, which can save a lot of man-hours. Performance of carbonaceous castables containing silicon carbide raw materials in blast furnace bottoms.
- (1) Carbonaceous castables using silicon carbide as the main raw material have higher strength. The compressive strength after 24 hours of insulation at 110°C is greater than 17MPa, and the compressive strength after 3 hours of insulation at 1450°C is greater than 70MPa. The thermal conductivity at 700°C measured using the laser method is 7.2W·(m·K)⁻¹. The compressive strength of imported carbon castables using carbon as the main raw material after being kept at 110°C for 24 hours is 18.3MPa. The compressive strength after being kept at 1450°C for 3 hours was significantly reduced. The thermal conductivity at 700℃ measured by laser method is 5.08W·(m·K)⁻¹. Its thermal conductivity is relatively low compared to the technical requirements of blast furnace bottom carbonaceous castables.
- (2) After the sol-bonded carbon castable with silicon carbide as the main raw material is soaked in water, the compressive strength and volume density increase, while the shape remains unchanged. After soaking in 2% (w) hydrochloric acid solution, the compressive strength after 30 days decreased. After immersion in 2% (w) sulfuric acid solution, the compressive strength decreased after 30 days, and the decrease was smaller than that in hydrochloric acid solution. After soaking in 2% (w) sodium hydroxide solution, it was completely loosened into powdered materials in 30 days. Carbon castables made of silicon carbide as the main raw material are not resistant to immersion in alkali solutions. In an environment where alkali metal vapor may penetrate into the blast furnace bottom, such carbonaceous castables should be used with caution if there is cooling water leakage.
Rongsheng Refractory Castable Manufacturer is a powerful refractory material manufacturer. Rongsheng Manufacturer has an environmentally friendly, fully automatic unshaped refractory material production line. The refractory lining materials products of Rongsheng manufacturer have been sold to more than 120 countries around the world, such as South Africa, Chile, Egypt, Colombia, Uzbekistan, Italy, Indonesia, Ukraine, Hungary, Spain, Kenya, Syria, Zambia, Oman, Venezuela, India, Peru, the United States, Ethiopia, etc. We can customize refractory lining materials according to the actual working conditions of high-temperature furnace linings. To purchase high-quality silicon carbide refractory materials, please choose Rongsheng Refractory Castable Manufacturer.