SiC is widely used in key areas of the steel and nonferrous metallurgy industries due to its stable high-temperature chemical properties, excellent high-temperature strength, high wear resistance, and good thermal shock resistance. Examples include blast furnace tuyere, inner wall, ceramic cups, various furnace wall linings, and kiln furniture. Compared to metals and intermetallic compounds, silicon carbide refractories have higher high-temperature strength and creep resistance. Compared to oxide ceramics, they have higher thermal conductivity and thermal shock resistance. The high-temperature properties of silicon carbide refractories are as follows:
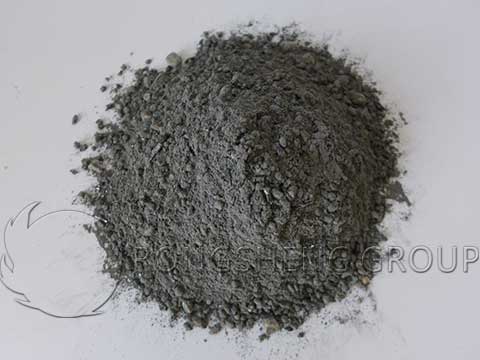
High-Temperature Oxidation Resistance of SiC Refractories
Although SiC offers excellent performance, it is susceptible to oxidation during long-term use. Extensive research has been conducted on the oxidation process of SiC. Results indicate that high-temperature oxidation of SiC can be divided into two types: passive oxidation and active oxidation. When the O₂ partial pressure is below 10⁻⁴Pa, SiC undergoes active oxidation, with the product being SiO₂ gas and the net weight decreasing. When the O₂ partial pressure is above 10⁻⁴Pa, SiC undergoes passive oxidation, with the product being SiO₂ and the net weight increasing. The formation of a SiO₂ protective film prevents further oxidation. However, at oxidation temperatures above 1473K, SiO₂ converts to cristobalite at high temperatures. This volume expansion destroys the structure of the oxide film, causing cracks, which in turn leads to internal oxidation, severely shortening the service life of the SiC material. Therefore, improving the oxidation resistance of SiC materials is an essential consideration in the design and preparation of SiC refractories.
The high-temperature oxidation behavior of a self-bonded SiC material with a porosity of 11.5% in air at 1573K was studied. Research results show that the amorphous SiO2 formed during the initial oxidation process can passivate pores and crack tips within the material, resulting in an increase in the room-temperature strength of the material with increasing oxidation time. The refractory material achieved its highest strength, reaching 293 MPa, at an oxidation time of 22.5 h. As oxidation time continues, the amorphous SiO2 crystallizes to form cristobalite, destroying the structure of the oxide film and generating new surface cracks during cooling, resulting in a decrease in the room-temperature strength of the material.
The effects of adding varying amounts of calcium oxide, aluminum oxide, and zirconium oxide to SiC on its oxidation resistance at different temperatures were investigated. Experimental results show that a 2 wt% aluminum oxide addition yields the best oxidation resistance. Mullite coatings were generated on recrystallized SiC materials of varying particle sizes using a sol-gel method. The effects of coating thickness and particle size on the high-temperature oxidation behavior of the recrystallized SiC at 1773 K were investigated. Results show that the formation of mullite coatings significantly improves the high-temperature oxidation resistance of the recrystallized SiC. Furthermore, increasing coating thickness increases the oxidation resistance of the recrystallized SiC material. Al₂O₃, SiO₂, and Mullite coatings were applied to SiC whiskers using a sol-gel method. Anti-oxidation experiments showed that all three coatings improved the oxidation resistance of SiC.
In summary, while silicon carbide refractories possess relatively good oxidation resistance, oxidation to a certain degree can be fatal to the material’s structure. Therefore, studying the mechanism and control of the oxidation process in silicon carbide refractories, as well as its impact on the material’s structure and properties, is of great significance.
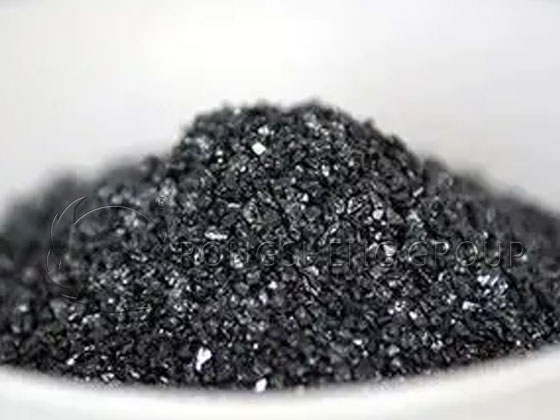
Thermal Shock Resistance of SiC Refractories
As an important high-temperature industrial structural material, silicon carbide refractories have high requirements for thermal shock resistance. The thermal shock resistance of SiC materials is not only related to their microstructure, grain size, and the shape and distribution of internal defects, but also to physical properties such as strength, elastic modulus, thermal conductivity, thermal expansion coefficient, Poisson’s ratio, and porosity. Improving and enhancing the thermal shock resistance of SiC materials is crucial for their safe and stable use.
The Effect of Different Bonding Methods on the Thermal Shock Resistance of SiC Kiln Furniture. Si2N2O-bonded SiC kiln furniture exhibits superior thermal shock resistance to mullite- and Si3N4-bonded SiC kiln furniture. When the Si2N2O content is ≤20%, the thermal shock resistance of Si2N2O-bonded SiC samples improves with increasing Si2N2O content. When the Si2N2O content exceeds 20%, the thermal shock resistance of the samples decreases.
Si3N4-SiC and Sialon-SiC materials were prepared by reaction sintering. The results show that the in-situ formation of Si3N4 or Sialon bonding phases can increase the toughness of SiC materials, influence crack propagation, and modulate stress distribution at high temperatures, improving the material’s plastic deformation capacity at high temperatures and, consequently, enhancing the thermal shock resistance of SiC materials.
The thermal shock resistance of reaction-sintered SiC materials was also studied. The results show that materials with low residual Si content and small SiC particles exhibit superior thermal shock resistance to materials with high residual Si content and large SiC particles.
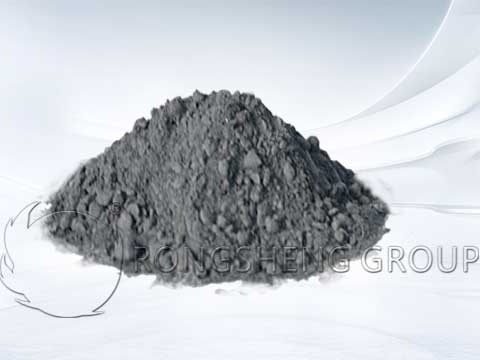
SiC Refractories’ Resistance to Cryolite Attack
SiC is used as the bottom material for aluminum electrolytic cells because it is non-wettable by molten aluminum and exhibits high thermal conductivity, chemical stability, and excellent oxidation resistance. Aluminum smelting typically uses cryolite (Na₃AlF₆) as a flux, and is carried out by electrolytic reduction of aluminum oxide in the electrolytic cell at a temperature typically between 1173 and 1273 K. Therefore, studying the resistance of SiC materials to cryolite attack is of great practical significance.
The attack of cryolite on various non-oxides, such as BN, SiC, Si₃N₄, Al₁N, and TiN, was studied. The results showed that these non-oxides exhibited good resistance to cryolite attack. Cryolite melt enters the pores of Si₃N₄-bonded SiC refractory materials and reacts with the binder phase. Erosion of the binder phase causes SiC particles to fall into the cryolite melt, resulting in corrosion of the material.
The crucible method was used to study the cryolite melt corrosion resistance of Si3N4-bonded SiC refractory materials. The results showed that after 20 hours of corrosion at 1273K, only a small amount of corrosion was observed on the inner wall of the crucible of the Si3N4-bonded SiC refractory prepared in an air atmosphere. This indicates that the material has good cryolite corrosion resistance.
The static crucible method was also used to study the cryolite corrosion resistance of alumina-based Sialon-bonded corundum-SiC composite refractory materials at 1273K. The results showed that under these conditions, cryolite erosion of the composite material was minimal, with an erosion layer thickness of approximately 1mm, and the erosion product being NaAlSiO4. The penetration layer depth was approximately 6mm, and the penetration rate decreased with increasing Sialon content.
In summary, silicon carbide refractory materials have excellent cryolite corrosion resistance. The corrosion mechanism suggests that corrosion primarily occurs between cryolite and oxides in the binder phase. Reducing or eliminating the oxide content in the binder phase could further improve the cryolite corrosion resistance of silicon carbide refractory materials.
To purchase high-quality silicon carbide refractory materials, please contact Rongsheng Refractory Materials Factory for free samples and quotes.