Lightweight castables have lower thermal conductivity than heavy castables and significantly reduce the weight of the furnace lining. The diffusion rate of combustion temperature in industrial furnaces can be reduced by about 30% compared to heavy castables. Therefore, using lightweight insulating castables as insulation layers can effectively reduce the heat loss of industrial furnace linings.
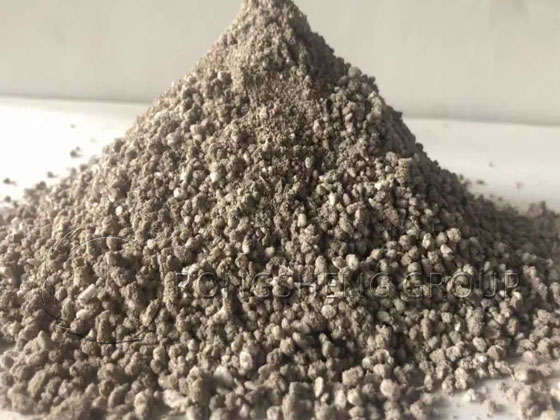
Lightweight Castables as Insulation for Industrial Furnaces
Lightweight castables are the first layer of material that adheres to the furnace shell in the kiln lining. High-end lightweight castables, such as hollow alumina sphere castables and lightweight mullite refractory castables, can also be used directly as a working layer on the lining of some lightweight kilns. This reduces furnace weight, lowers heat consumption, and saves energy costs.
The thickness of lightweight castables used as insulation should be 80mm-150mm. Thicknesses below 50mm will result in poor installation and ineffective insulation. Using lightweight castables for lining pipes and chimneys is also a poor choice. Castables with a specific gravity of approximately 1.5 can serve as both an insulation layer and a working layer. This reduces weight while meeting the requirements for chimney and pipe linings.
Lightweight castables are used at different temperatures: low temperatures (600-900°C), medium temperatures (900-1200°C), and high temperatures (1200°C). High-temperature insulation layers require high-quality lightweight materials, such as lightweight mullite and hollow alumina sphere castables. Commonly used materials include vermiculite, perlite, and ceramsite. These materials have an operating temperature of approximately 1000°C and cannot be used at high temperatures. Lightweight mullite and corundum-mullite castables can be used at temperatures between 1350°C and 1500°C, allowing for direct use in the working layer.
Lightweight castables lack the refractoriness, compressive strength, and flexural strength of heavier castables. However, their low thermal conductivity provides excellent insulation. Choosing the right lightweight material for different temperatures and kiln linings can effectively insulate and reduce energy consumption.
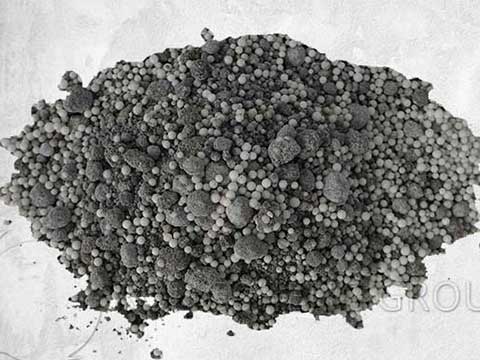
Significant Features of Low Thermal Conductivity Castables
Low thermal conductivity castables are unique refractory materials that maintain low bulk density and low thermal conductivity even at high temperatures, while also offering excellent thermal insulation. Unlike conventional lightweight castables, whose bulk density increases with increasing temperature, low thermal conductivity castables maintain a low bulk density even at high temperatures. Their light weight effectively reduces the weight of equipment, which is crucial for the installation and operation of large-scale industrial equipment. Furthermore, their excellent thermal insulation properties ensure more uniform furnace temperature distribution, thereby saving energy and reducing production costs.
In terms of technical performance, low thermal conductivity castables offer the dual advantages of low bulk density and high refractory strength, a true innovation in themselves. They offer strong overall performance, excellent spalling resistance, a long service life, and can be repaired and processed into various shapes as needed. They can also be used to construct integral furnace linings, greatly facilitating the maintenance and construction of industrial furnaces.
Wide Application Areas and Energy-Saving Advantages
Low thermal conductivity castables have a wide range of applications across numerous industries. They are widely used in industrial furnaces and thermal equipment in industries such as metallurgy, machinery, power generation, chemicals, and petroleum. Compared to conventional lightweight castables, using low thermal conductivity castables can achieve energy savings of over 20%, a significant saving for energy-intensive industries. Especially in applications such as petroleum and petrochemical furnaces, where material performance requirements are more stringent, low thermal conductivity castables require a lower bulk density and adhere to stricter quality standards. Therefore, compared to lightweight castables used in other industries, low thermal conductivity castables for petroleum and petrochemical furnaces are of higher quality and relatively higher price. However, the energy-saving benefits and equipment protection they provide are well worth the effort.
Easy Construction
Low thermal conductivity castables are relatively easy to apply. Manufacturers carefully select the aggregate particle size. An appropriate particle size helps enhance the compressive strength of lightweight castables. Excessively large particle sizes can negatively impact the construction process. By optimizing the particle size, low thermal conductivity castables can be constructed more smoothly, reducing difficulties and problems during construction, improving construction efficiency, and ensuring construction quality.
Considerations for Lightweight Castable Pipe Installation
Lightweight castables provide insulation. For pipe use, their bulk density generally must be no less than 1.2 kg/m³. Specific gravity of 1.5 is more common. When used in pipes, installation is limited by the pipe diameter, making it difficult for workers to work within the pipe.
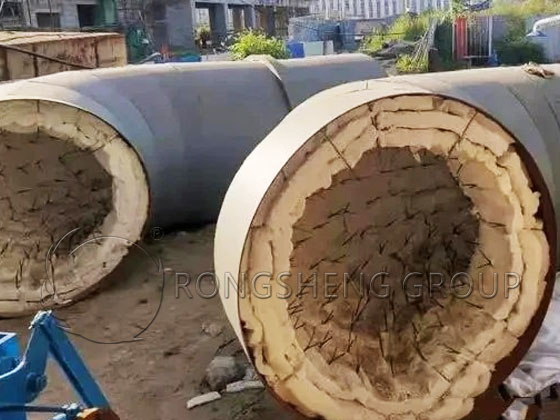
1. Pay attention to the insulation layer.
Applying the insulation layer to the insulation is also challenging. The pipe insulation in the image above is applied irregularly, and the anchors are not suitable for use. Anchors must be painted. If not, plastic caps must be placed on them. Otherwise, rust will occur, shortening their lifespan.
If this occurs, there is a remedy: apply a layer of plastic film to the surface of the insulation. This prevents moisture from penetrating the insulation during baking after the lightweight castable is applied. If moisture seeps into the insulation, even after drying, the insulation’s effectiveness will be reduced.
2. Pay attention to the proportions added during construction.
When applying lightweight materials, the water ratio must be carefully considered. If too little water is added, some of the base materials, due to their light weight, will be difficult to apply and will not set easily. Adding too much water will affect the strength of the material in the final application.
3. Mix the aggregate and powder before construction.
During on-site construction, first mix the aggregate and powder, then add the binder. Then, strictly follow the manufacturer’s water ratios and mix the lightweight castable. After mixing, verify that the castable has good fluidity before vibrating. Generally, the water content for lightweight castables is 15-17%. Some manufacturers, due to the light weight of the lightweight castable, may sprinkle some water during production to facilitate production control.